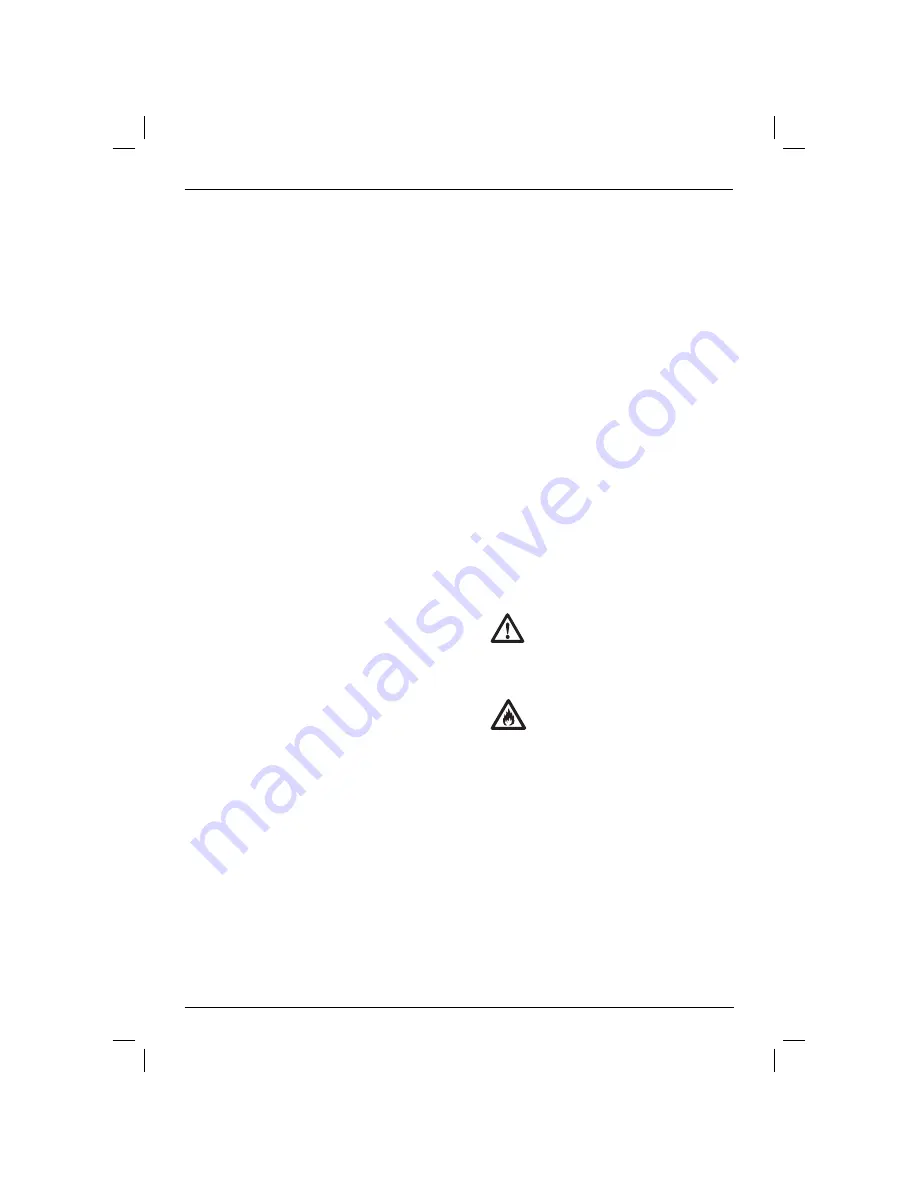
ENGLISH
32
5. To minimize stalling or breaking through the
material, reduce pressure on drill and ease the
bit through the last fractional part of the hole.
6. Keep the motor running when pulling the bit
back out of a drilled hole. This will help prevent
jamming.
7. With variable speed drills there is no need to
center punch the point to be drilled. Use a
slow speed to start the hole and accelerate by
squeezing the trigger harder when the hole is
deep enough to drill without the bit skipping
out.
DRILLING IN METAL
An SDS Plus
®
to round shank adapter chuck is
required. Ensure that tool is in drill-only mode. Start
drilling with slow speed and increase to full power
while applying firm pressure on the tool. A smooth
even flow of metal chips indicates the proper drilling
rate. Use a cutting lubricant when drilling metals.
The exceptions are cast iron and brass which should
be drilled dry.
NOTE:
Large [7.9 mm to 12.7 mm (5/16" to 1/2")]
holes in steel can be made easier if a pilot hole
[4 mm to 4.8 mm (5/32" to 3/16")] is drilled first.
DRILLING IN WOOD
An SDS Plus
®
to round shank adapter chuck is
required. Ensure that tool is in drill-only mode. Start
drilling with slow speed and increase to full power
while applying firm pressure on the tool. Holes in
wood can be made with the same twist drills used
for metal. These bits may overheat unless pulled out
frequently to clear chips from the flutes. For larger
holes, use spade bits, power auger bits, or hole
saws. Work that is apt to splinter should be backed
up with a block of wood.
Screwdriving (fig. 1)
1. Set the mode selector switch (g) to the rotary
drilling position.
2. Select the direction of rotation.
3. Insert the special SDS Plus
®
screwdriving
adaptor for use with hexagonal screwdriver bits.
4. Insert the appropriate screwdriver bit. When
driving slotted head screws always use bits with
a finder sleeve.
5. Gently press the variable speed switch (a) to
prevent damage to the screw head. In reverse
(LH) rotation the tool speed is automatically
reduced for easy screw removal.
6. When the screw is flush with the workpiece,
release the variable speed switch to prevent
the screw head from penetrating into the
workpiece.
Hammerdrill Operation
1. When drilling, use just enough force on the
hammer to keep it from bouncing excessively
or “rising” off the bit. Too much force will cause
slower drilling speeds, overheating, and a lower
drilling rate.
2. Drill straight, keeping the bit at a right angle to
the work. Do not exert side pressure on the bit
when drilling as this will cause clogging of the
bit flutes and a slower drilling speed.
3. When drilling deep holes, if the hammer speed
starts to drop off, pull the bit partially out of
the hole with the tool still running to help clear
debris from the hole.
4. For masonry, use carbide-tipped bits or
masonry bits. A smooth even flow of dust
indicates the proper drilling rate.
Chipping and Chiselling
1. To switch from hammer drilling to chiselling, first
insert the SDS Plus
®
chisel and check if it is
properly locked.
2. When switching from hammer drilling mode to
chiselling mode, turn the chisel to the desired
position. If you find resistance during mode
change, turn the chisel slightly to engage the
spindle lock.
WARNING:
• The hammer is only for light chiselling
applications.
•
The forward/reverse switch must be in
the forward position when chiselling
WARNING:
• Do not use this tool to mix or pump
easily com busti ble or explosive fluids
(ben zine, alcohol, etc.).
•
Do not mix or stir inflammable liquids
labelled accordingly.
Various types of SDS Plus
®
drill bits and adaptors
are available as an option.
Consult your dealer for further information on the
appropriate accessories.
MAINTENANCE
Your D
E
WALT power tool has been designed to
operate over a long period of time with a minimum
of maintenance. Continuous satisfactory operation
depends upon proper tool care and regular cleaning.
Summary of Contents for SDS PLUS DWEN101
Page 1: ...DWEN101 www eu ...
Page 3: ...1 Figure 1 Figure 2 f g f g g f d h a c g i e f b ...
Page 4: ...2 Figure 3 b c ...