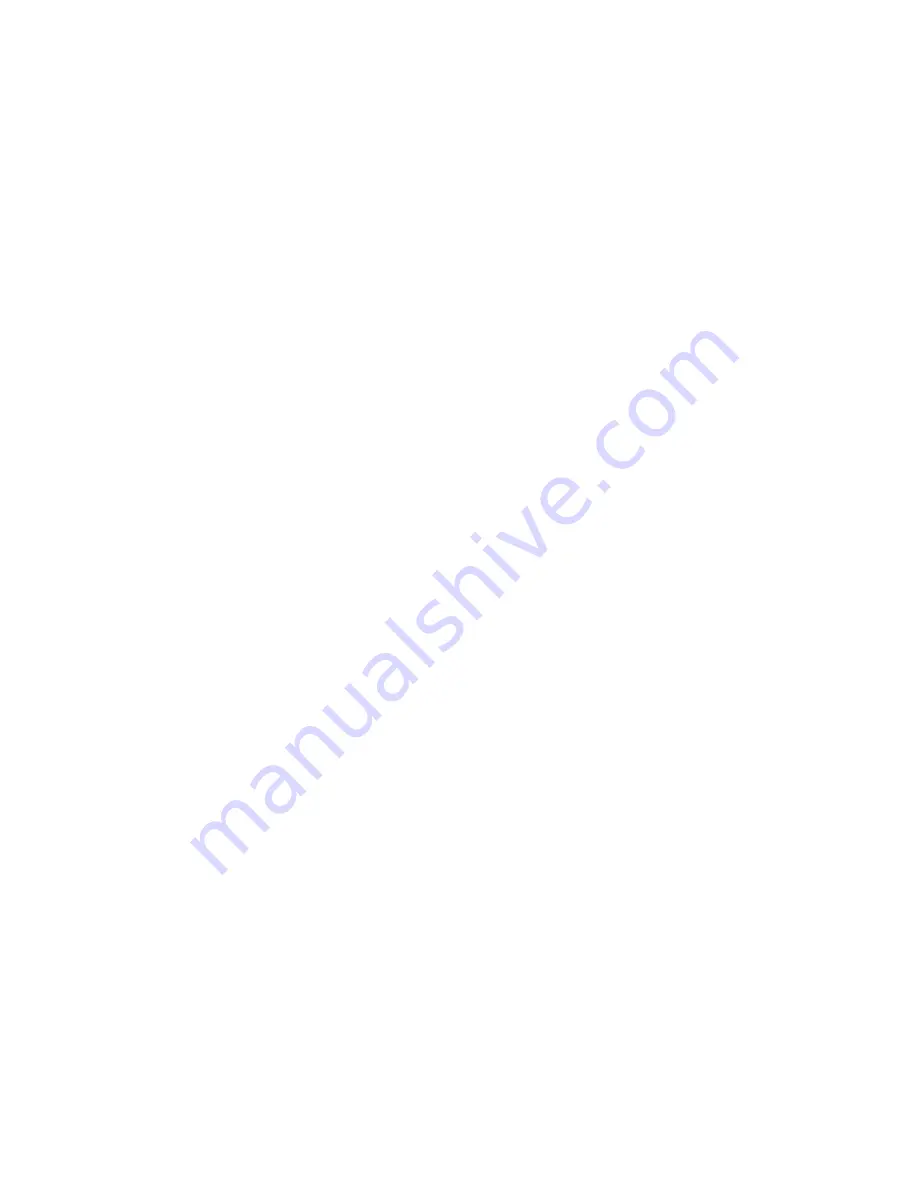
9
exhaust end of one pipe is inside the next one downstream. The addition of an exhaust pipe
tends to reduce the amount of air the blower can exhaust. This does not affect the dryer
operation if held within practical limits. For the most efficient operation, it is recommended that
no more than 14 ft (4.25m) of straight 8 in. (200 mm) diameter pipe with two right angle elbows
is used for each cylinder. When more than two elbows are used, 2 ft. (600 mm) of straight pipe
should be removed for each additional elbow. No more than four right angle elbows should be
used to exhaust a dryer. The design of the vent system shall be such that any condensate formed
when operating the dryer from cold shall either be retained and re-evaporated or discharged.
If the exhaust pipe passes through a wall, a metal sleeve of slightly larger diameter should be
set in the wall and the exhaust pipe passed through this sleeve. This practice is required by some
local codes and is recommended in all cases to protect the wall. This type of installation should
have a means provided to prevent rain and high winds from entering the exhaust when the dryer
is not in use. A hood with a hinged damper can be used for this purpose. Another method would
be to point the outlet end of the pipe downward to prevent entrance of wind and rain. In either
case, the outlet should be kept clear, by at least 24 in. (600 mm), of any objects that would cause
an air restriction.
Provide a screen or grill over the termination of the exhaust or flue outlet such as will
prevent the entry of a ball of 16 mm in diameter while the machine is not operating but will
allow entry of a ball 6 mm in diameter while operating.
When exhausting a dryer straight up through a roof, the overall length of the duct has the
same limits as exhausting through a wall. A rain cap must be placed on top of the exhaust and
must be of such a type as to be free from clogging. The type using a cone shaped “roof” over the
pipe is suitable for this application.
Exhausting the dryer into a chimney or under a building is not permitted. In either case,
there is a danger of lint build-up, which can be highly combustible.
Installation of several dryers, where a main discharge duct is necessary, will need the
following considerations for installation (see Figure 3). Individual 8 in. (200 mm) ducts from the
dryers into the main discharge duct should be at a 45-degree angle in the direction of discharge
airflow.
NOTE:
Never install the individual 8" ducts at a right angle into the main discharge duct.
The individual ducts from the dryers can enter at the sides or bottom of the main discharge duct.
Figure 3 indicates the various round main duct diameters to use with the individual dryer ducts.
The main duct can be rectangular or round, provided adequate airflow is maintained. For each
individual dryer, the total exhausting (main discharge duct plus duct outlet from the dryer)
should not exceed the equivalent of 14 ft (4.27m) and two elbows. The diameter of the main
discharge duct at the last dryer must be maintained to exhaust end.
NOTE:
A small diameter duct will restrict airflow; a large diameter duct will reduce air
velocity; both contributing to lint build up. An inspection door should be provided for periodic
clean out of the main duct.
Summary of Contents for DDAD30HC-59 Series Dryers
Page 3: ...3 Figure 1 30 Stack Dryer Dimensions inches mm ...
Page 11: ...11 ...