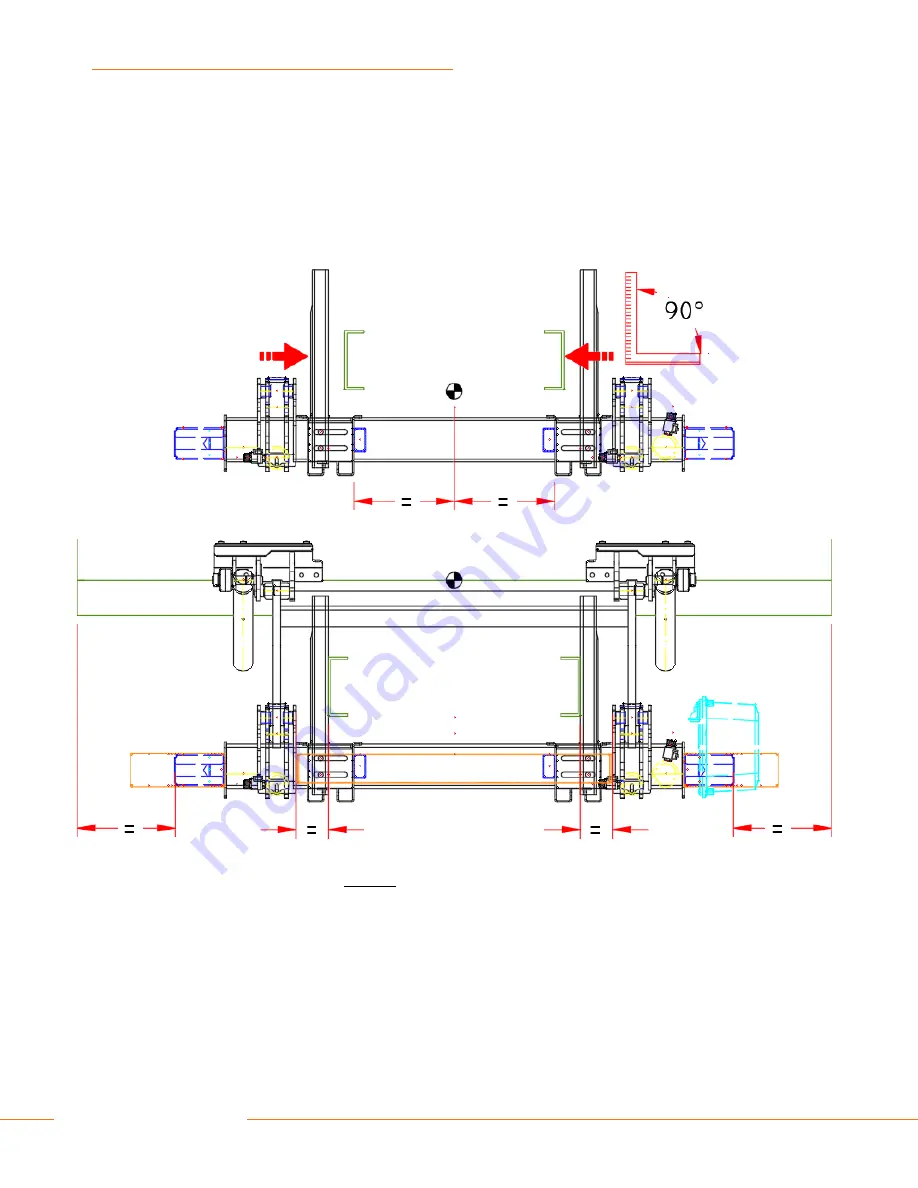
26
DHOLLANDIA
8.3
FIXATION OF THE MOUNTING PLATES OAM010
•
Except lifts equipped with premounted mounting plates (DH-LV, etc.), the mounting plates are designed as bolt-on system, both where
the plates are joined to the lift frame, as where they are mounted to the vehicle chassis.
•
If you intend to weld anyhow, note that liftgate might be equipped with thermoplastic hoses. Observe the important precautions in 4
on page 6.
•
Ensure that the lift frame is correctly centered under the vehicle chassis and body.
•
Adjust the mounting plates to the width of the vehicle.
•
Straighten the mounting plates, and make sure they stand perpendicular to the lift frame.
•
The mounting plates should be bolted to the lift frame according to the instructions included in the bolt kit supplied with the liftgate
(see below).
Summary of Contents for DH-L 3300 lbs
Page 17: ...16 DHOLLANDIA LMS 55 66...
Page 28: ...27 DHOLLANDIA...
Page 49: ...48 DHOLLANDIA...
Page 52: ...51 DHOLLANDIA 11 3 1 Installation of 3 Button Wander Lead OAE002 E0784 M S...
Page 53: ...52 DHOLLANDIA 11 3 2 Installation of cabin cutoff switch OAE510 15 E0393 S 15...
Page 59: ...58 DHOLLANDIA EF0583 LM EN EF0565 EN EF0620 EN EF0580 EN CAP...
Page 60: ...59 DHOLLANDIA EF0585 US Serial Number EF0581 EN EF0563 EN EF0616 EF0562 EN...
Page 68: ...67 DHOLLANDIA...
Page 69: ...68 DHOLLANDIA...