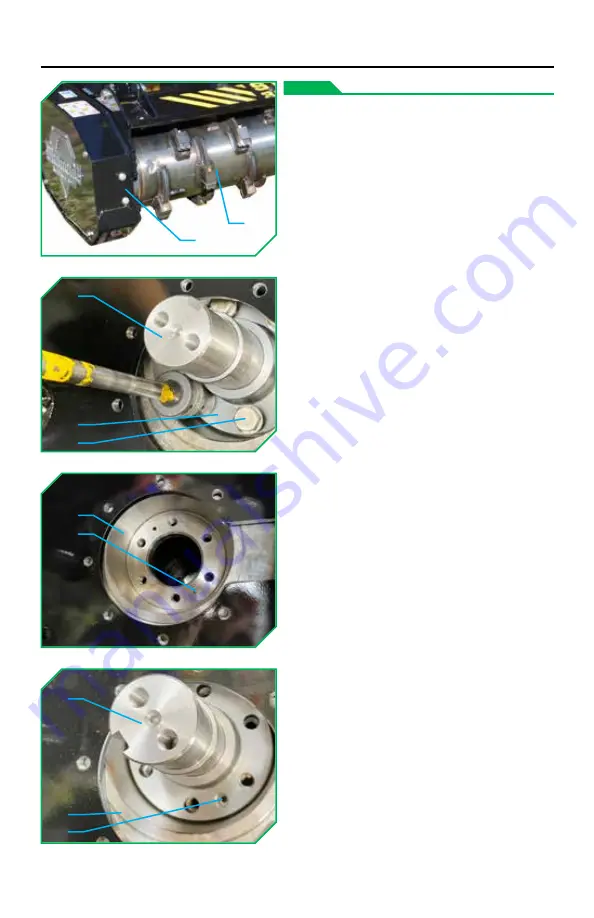
© Diamond Mowers®, LLC
DRUM
•
The drum
(1)
should be inspected
every 10 hours or daily.
•
Access covers
(6)
are provided on
each end of the drum
(1)
on the front
of the machine as illustrated to
allow for the removal of wrapped
wire and trapped debris.
•
Raise the attachment to inspect the
drum
(1)
for any cracks, damage, etc.
Replace the drum
(1)
as needed if
damage is found:
◦
Support the weight of the
drum, and remove the bearings
securing the drum
(1)
as described
in the
BEARINGS
section.
◦
Remove the hardware
(2)
retaining
the stub shafts
(3)
on the drum
(1)
.
-
Remove the stub shafts
(3)
and
set them aside with
their hardware
(2)
.
◦
Replace the drum
(1)
and
reassemble in reverse order.
-
NOTE:
Confirm the breather
holes
(5)
on the drum are
aligned and visible through
the non-threaded holes on the
stub shafts
(3)
as illustrated.
-
Use Loctite 262.
-
Torque the stub shaft
hardware
(2)
to
240ft-lbs (325Nm).
MAINTENANCE
(1)
(6)
(3)
(4)
(2)
(4)
(5)
(3)
(4)
(5)
28