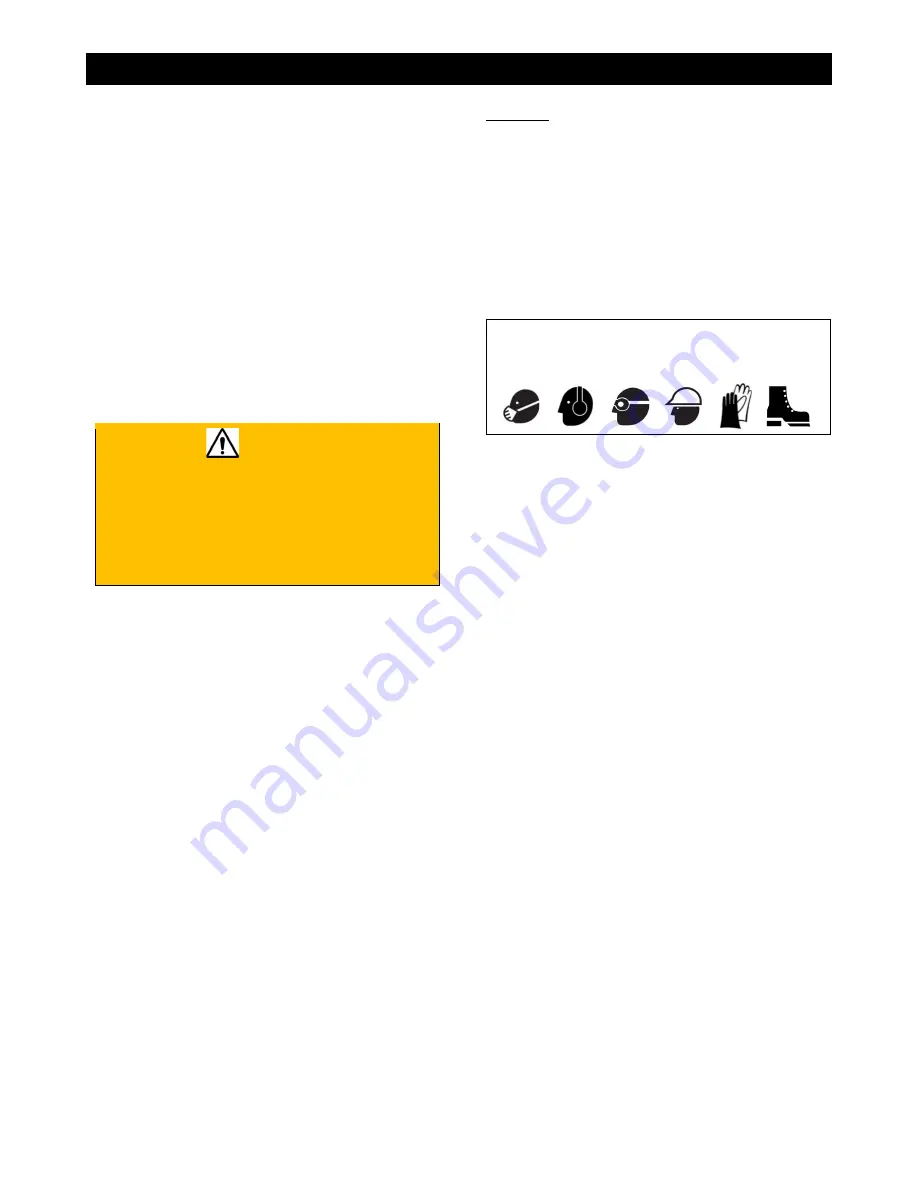
SAFETY PRECAUTIONS
General Safety
•
Read and understand all safety,
operations, and maintenance instructions
provided in this manual prior to operating or
servicing the saw.
•
Keep equipment components clean and
free of slurry, concrete dust, and debris.
•
Inspect water hoses prior to operating the
equipment. Clean, repair, or replace
damaged components.
•
Raise the equipment to a proper height for
access when working underneath the
equipment. Use chocks to block the
wheels, and fit blocks or jacks under the
frame edges.
WARNING
Do NOT work on equipment using the
hydraulic lift system to keep the equipment
in the raised position for maintenance or
repair. Accidental loss of hydraulic pressure
could cause the equipment to drop
suddenly, resulting in serious injury or death.
•
When using a jack to raise the equipment,
place the jack against a solid, flat area
under the frame base to properly support
the equipment.
•
Repair the equipment immediately when a
problem arises.
•
Replace equipment decals if unreadable.
•
Dispose of all hazardous waste materials
according to city, state, and federal
regulations.
•
Always have a phone nearby, and locate
the nearest fire extinguisher and first aid kit
prior to operating the equipment.
•
Operate the equipment wearing flame
resistant clothing.
•
Always wear safety glasses when removing
retaining rings.
•
Underage or non-trained personnel should
not operate the equipment.
•
Keep all body parts away from rotating
machinery.
•
Replace all guards and access panels
(unless stated otherwise) prior to operating
the equipment.
•
Always pivot front of blade guard fully
closed to avoid serious injuries.
DO NOT:
•
Assume the equipment will remain still
when in neutral or when parking/stopping
the equipment on a slope. Chock the
wheels to help prevent unnecessary
movement.
•
Drop equipment, supplies, tools, etc., when
handling to help prevent injuries.
•
Lift and carry equipment, supplies, tools,
etc., that are too heavy and/or cannot be
lifted easily.
•
Operate the equipment without using the
appropriate safety equipment required
for the work task.
•
Operate or service the equipment with any
clothing, hair, or accessories that can snag
in the machinery, which could lead to
serious injuries or death!
•
Operate the equipment using attachments
not associated with or recommended for
the equipment.
•
Operate the equipment around combustible
materials.
•
Operate the equipment with anyone near
the work area or within the direct line of the
blade.
•
Operate the equipment until all
unnecessary materials have been removed
from the work area.
•
Operate the equipment with loose nuts,
screws, and bolts.
•
Operate the equipment when ill or fatigued.
•
Operate the equipment under the influence
of drugs and/or alcohol.
•
Operate the equipment on steep slopes.
•
Cut concrete with guards and access
panels removed.
•
Grease the equipment with the engine
running.
•
Touch hot components when operating the
equipment.
•
Leave the equipment unattended until the
engine is off and the blade has stopped.
•
Place the equipment into storage until it
has cooled down.
•
Service the equipment until it has cooled
down.
•
Service the equipment with the engine
running.
13
Summary of Contents for CC5049D
Page 1: ...CORE CUT OPERATOR S MANUAL CC5049D Rev 21 00 Part 1802721...
Page 2: ......
Page 8: ...INTRODUCTION CC5049D Controls 8...
Page 11: ...INTRODUCTION CC5049D Specifications 11...
Page 58: ...REFERENCES 58...
Page 59: ...REFERENCES 59...
Page 60: ...REFERENCES 60...
Page 67: ......