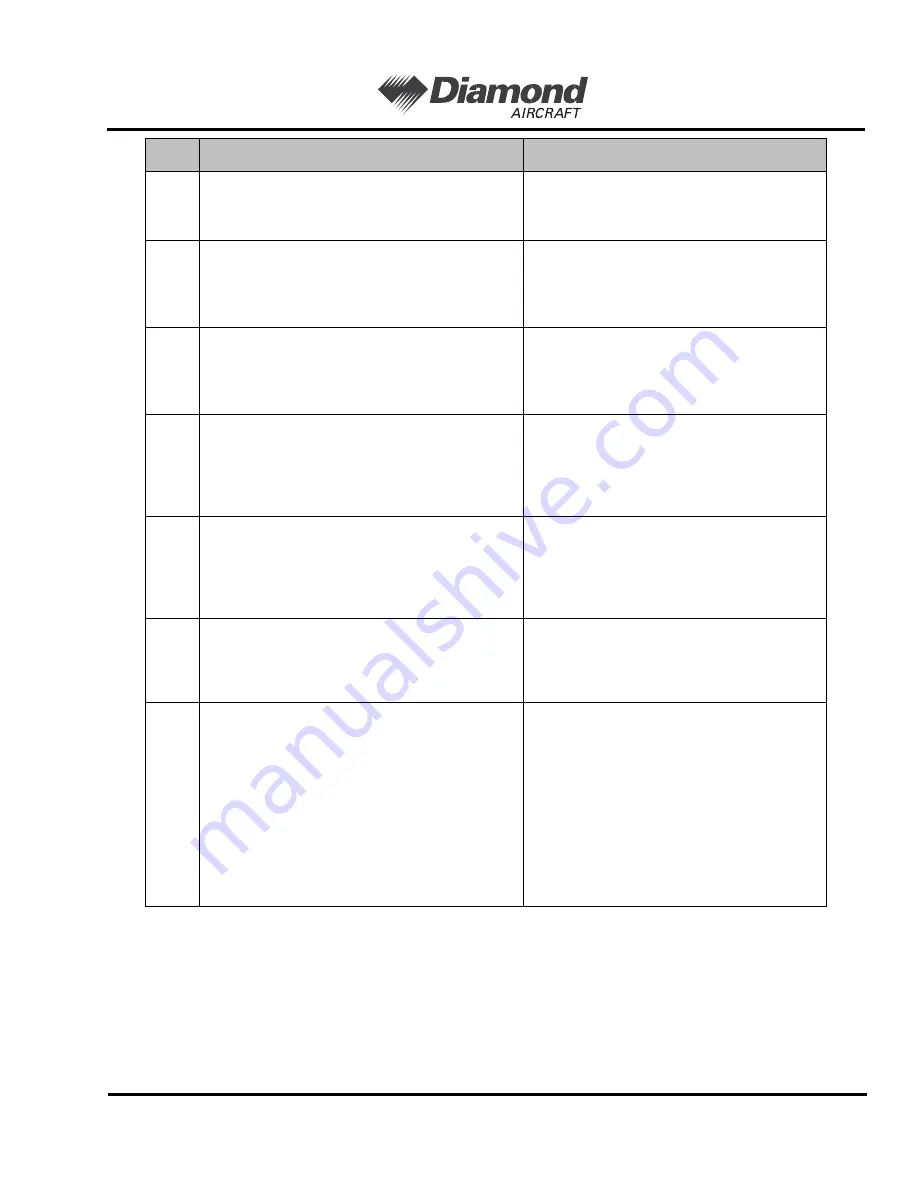
Page 205
Rev 16
71-00-00
Maintenance Practices
DA20-C1 AMM
DA201-C1
30 Oct 09
16.
Remove the two worm drive clamps from the
flexible pipe between the oil cooler and the aft
baffle. Remove the flexible pipe.
17.
Disconnect the inlet and return oil pipes from
the oil cooler.
Put the caps on the two oil hoses and put
the caps on the two oil cooler connections.
This will stop contamination going into the
oil system.
18.
Disconnect the vacuum hose from the firewall
connection.
Put a cap on the firewall adapter and put a
cap on the vacuum feed hose. This will stop
contamination going into the vacuum
system.
19.
Remove the shield from the right side of the aft
baffle.
- Remove the manifold fuel pressure hose
clear of the aft baffle/engine.
20.
Remove the two worm drive clamps from the
flexible pipe between the muffler and the cabin
heat control valve.
- Remove the flexible pipe.
21.
Remove the engine exhaust system.
Refer to Chapter 78-00.
- Remove the eight nuts from the four
exhaust port flanges.
Discard the nuts.
22.
Remove the heat shield from the right side of
the engine:
- Remove the two screws and the spring
washers from the two brackets at the
cylinder heads
- Remove the heat shield with the fuel pipes
and electrical cables attached
- Move the heat shield clear of the engine.
Detail Steps/Work Items
Key Items/References
Summary of Contents for DA20-C1
Page 25: ...Page 1 Rev 16 52 TITLE Doors DA20 C1 AMM DA201 C1 30 Oct 09 CHAPTER 52 00 DOORS ...
Page 26: ...Doors DA20 C1 AMM 52 TITLE 30 Oct 09 Page 2 DA201 C1 Rev 16 Intentionally Left Blank ...
Page 28: ...52 TOC DA20 C1 AMM Doors 14 Jan 13 Page 2 DA201 C1 Rev 21 Intentionally Left Blank ...
Page 30: ...Doors DA20 C1 AMM 52 00 00 14 Jan 13 Page 2 DA201 C1 Rev 21 Intentionally Left Blank ...
Page 34: ...Doors DA20 C1 AMM 52 10 00 30 Oct 09 Page 4 DA201 C1 Rev 16 Intentionally Left Blank ...
Page 48: ...Doors DA20 C1 AMM 52 40 00 30 Oct 09 Page 2 DA201 C1 Rev 16 Intentionally Left Blank ...
Page 49: ...Page 1 Rev 16 53 TITLE Fuselage DA20 C1 AMM DA201 C1 30 Oct 09 CHAPTER 53 00 FUSELAGE ...
Page 50: ...Fuselage DA20 C1 AMM 53 TITLE 30 Oct 09 Page 2 DA201 C1 Rev 16 Intentionally Left Blank ...
Page 52: ...53 TOC DA20 C1 AMM Fuselage 14 Jan 13 Page 2 DA201 C1 Rev 21 Intentionally Left Blank ...
Page 54: ...Fuselage DA20 C1 AMM 53 00 00 14 Jan 13 Page 2 DA201 C1 Rev 21 Intentionally Left Blank ...
Page 67: ...Page 1 Rev 16 55 TITLE Stabilizers DA20 C1 AMM DA201 C1 30 Oct 09 CHAPTER 55 00 STABILIZERS ...
Page 68: ...Stabilizers DA20 C1 AMM 55 TITLE 30 Oct 09 Page 2 DA201 C1 Rev 16 Intentionally Left Blank ...
Page 72: ...Stabilizers DA20 C1 AMM 55 00 00 14 Jan 13 Page 2 DA201 C1 Rev 21 Intentionally Left Blank ...
Page 74: ...Stabilizers DA20 C1 AMM 55 10 00 30 Oct 09 Page 2 DA201 C1 Rev 16 Intentionally Left Blank ...
Page 80: ...Stabilizers DA20 C1 AMM 30 Oct 09 Page 2 DA201 C1 Rev 16 55 20 00 Figure 1 Elevator Structure ...
Page 93: ...Page 1 Rev 16 56 TITLE Windows DA20 C1 AMM DA201 C1 30 Oct 09 CHAPTER 56 00 WINDOWS ...
Page 94: ...Windows DA20 C1 AMM 56 TITLE 30 Oct 09 Page 2 DA201 C1 Rev 16 Intentionally Left Blank ...
Page 96: ...56 TOC DA20 C1 AMM Windows 14 Jan 13 Page 2 DA201 C1 Rev 21 Intentionally Left Blank ...
Page 98: ...Windows DA20 C1 AMM 56 00 00 14 Jan 13 Page 2 DA201 C1 Rev 21 Intentionally Left Blank ...
Page 103: ...Page 5 Rev 16 56 10 00 Windows DA20 C1 AMM DA201 C1 30 Oct 09 Figure 3 Crack Repairs ...
Page 109: ...Page 1 Rev 16 57 TITLE Wings DA20 C1 AMM DA201 C1 30 Oct 09 CHAPTER 57 00 WINGS ...
Page 110: ...Wings DA20 C1 AMM 57 TITLE 30 Oct 09 Page 2 DA201 C1 Rev 16 Intentionally Left Blank ...
Page 112: ...57 TOC DA20 C1 AMM Wings 14 Jan 13 Page 2 DA201 C1 Rev 21 Intentionally Left Blank ...
Page 114: ...Wings DA20 C1 AMM 57 00 00 14 Jan 13 Page 2 DA201 C1 Rev 21 Intentionally Left Blank ...
Page 119: ...Page 5 Rev 16 57 10 00 Wings DA20 C1 AMM DA201 C1 30 Oct 09 Figure 2 Wing Structure Ribs ...
Page 120: ...Wings DA20 C1 AMM 57 10 00 30 Oct 09 Page 6 DA201 C1 Rev 16 Intentionally Left Blank ...
Page 132: ...Wings DA20 C1 AMM 30 Oct 09 Page 2 DA201 C1 Rev 16 57 50 00 Figure 1 Flap Structure ...
Page 138: ...Wings DA20 C1 AMM 30 Oct 09 Page 2 DA201 C1 Rev 16 57 60 00 Figure 1 Aileron Structure ...
Page 141: ...Page 1 Rev 16 61 TITLE Propeller DA20 C1 AMM DA201 C1 30 Oct 09 CHAPTER 61 00 PROPELLER ...
Page 142: ...Propeller DA20 C1 AMM 61 TITLE 30 Oct 09 Page 2 DA201 C1 Rev 16 Intentionally Left Blank ...
Page 144: ...61 TOC DA20 C1 AMM Propeller 14 Jan 13 Page 2 DA201 C1 Rev 21 Intentionally Left Blank ...
Page 146: ...Propeller DA20 C1 AMM 61 00 00 14 Jan 13 Page 2 DA201 C1 Rev 21 Intentionally Left Blank ...
Page 148: ...Propeller DA20 C1 AMM 61 10 00 30 Oct 09 Page 2 DA201 C1 Rev 16 Intentionally Left Blank ...
Page 157: ...Page 1 Rev 16 71 TITLE Power Plant DA20 C1 AMM DA201 C1 30 Oct 09 CHAPTER 71 00 POWER PLANT ...
Page 158: ...Power Plant DA20 C1 AMM 71 TITLE 30 Oct 09 Page 2 DA201 C1 Rev 16 Intentionally Left Blank ...
Page 162: ...Power Plant DA20 C1 AMM 14 Jan 13 Page 2 DA201 C1 Rev 21 71 00 00 Figure 1 Power Plant ...
Page 166: ...Power Plant DA20 C1 AMM 71 00 00 14 Jan 13 Page 6 DA201 C1 Rev 21 Intentionally Left Blank ...
Page 192: ...Power Plant DA20 C1 AMM 30 Oct 09 Page 2 DA201 C1 Rev 16 71 10 00 Figure 1 Engine Cowlings ...
Page 202: ...Power Plant DA20 C1 AMM 71 20 00 30 Oct 09 Page 2 DA201 C1 Rev 16 Intentionally Left Blank ...
Page 214: ...Power Plant DA20 C1 AMM 71 70 00 30 Oct 09 Page 4 DA201 C1 Rev 16 Intentionally Left Blank ...
Page 221: ...Page 1 Rev 16 72 TITLE Engine DA20 C1 AMM DA201 C1 30 Oct 09 CHAPTER 72 00 ENGINE ...
Page 222: ...Engine DA20 C1 AMM 72 TITLE 30 Oct 09 Page 2 DA201 C1 Rev 16 Intentionally Left Blank ...
Page 224: ...72 TOC DA20 C1 AMM Engine 14 Jan 13 Page 2 DA201 C1 Rev 21 Intentionally Left Blank ...
Page 226: ...Engine DA20 C1 AMM 14 Jan 13 Page 2 DA201 C1 Rev 21 72 00 00 Figure 1 Engine ...
Page 247: ...Page 1 Rev 16 74 TITLE Ignition DA20 C1 AMM DA201 C1 30 Oct 09 CHAPTER 74 00 IGNITION ...
Page 248: ...Ignition DA20 C1 AMM 74 TITLE 30 Oct 09 Page 2 DA201 C1 Rev 16 Intentionally Left Blank ...
Page 250: ...74 TOC DA20 C1 AMM Ignition 14 Jan 13 Page 2 DA201 C1 Rev 21 Intentionally Left Blank ...
Page 254: ...Ignition DA20 C1 AMM 74 00 00 14 Jan 13 Page 4 DA201 C1 Rev 21 Intentionally Left Blank ...
Page 269: ...Page 1 Rev 16 75 TITLE Air DA20 C1 AMM DA201 C1 30 Oct 09 CHAPTER 75 00 AIR ...
Page 270: ...Air DA20 C1 AMM 75 TITLE 30 Oct 09 Page 2 DA201 C1 Rev 16 Intentionally Left Blank ...
Page 272: ...75 TOC DA20 C1 AMM Air 14 Jan 13 Page 2 DA201 C1 Rev 21 Intentionally Left Blank ...
Page 290: ...76 TOC DA20 C1 AMM Engine Controls 14 Jan 13 Page 2 DA201 C1 Rev 21 Intentionally Left Blank ...
Page 343: ...Page 1 Rev 16 78 TITLE Exhaust DA20 C1 AMM DA201 C1 30 Oct 09 CHAPTER 78 00 EXHAUST ...
Page 344: ...Exhaust DA20 C1 AMM 78 TITLE 30 Oct 09 Page 2 DA201 C1 Rev 16 Intentionally Left Blank ...
Page 346: ...78 TOC DA20 C1 AMM Exhaust 14 Jan 13 Page 2 DA201 C1 Rev 21 Intentionally Left Blank ...
Page 348: ...Exhaust DA20 C1 AMM 14 Jan 13 Page 2 DA201 C1 Rev 21 78 00 00 Figure 1 Exhaust ...
Page 355: ...Page 1 Rev 16 79 TITLE Oil DA20 C1 AMM DA201 C1 30 Oct 09 CHAPTER 79 00 OIL ...
Page 356: ...Oil DA20 C1 AMM 79 TITLE 30 Oct 09 Page 2 DA201 C1 Rev 16 Intentionally Left Blank ...
Page 358: ...79 TOC DA20 C1 AMM Oil 14 Jan 13 Page 2 DA201 C1 Rev 21 Intentionally Left Blank ...
Page 364: ...Oil DA20 C1 AMM 79 00 00 14 Jan 13 Page 6 DA201 C1 Rev 21 Intentionally Left Blank ...
Page 379: ...Page 1 Rev 16 80 TITLE Starting DA20 C1 AMM DA201 C1 30 Oct 09 CHAPTER 80 00 STARTING ...
Page 380: ...Starting DA20 C1 AMM 80 TITLE 30 Oct 09 Page 2 DA201 C1 Rev 16 Intentionally Left Blank ...
Page 382: ...80 TOC DA20 C1 AMM Starting 14 Jan 13 Page 2 DA201 C1 Rev 21 Intentionally Left Blank ...
Page 392: ...Wiring Diagrams DA20 C1 AMM 92 TOC 14 Jan 13 Page 4 DA201 C1 Rev 21 Intentionally Left Blank ...