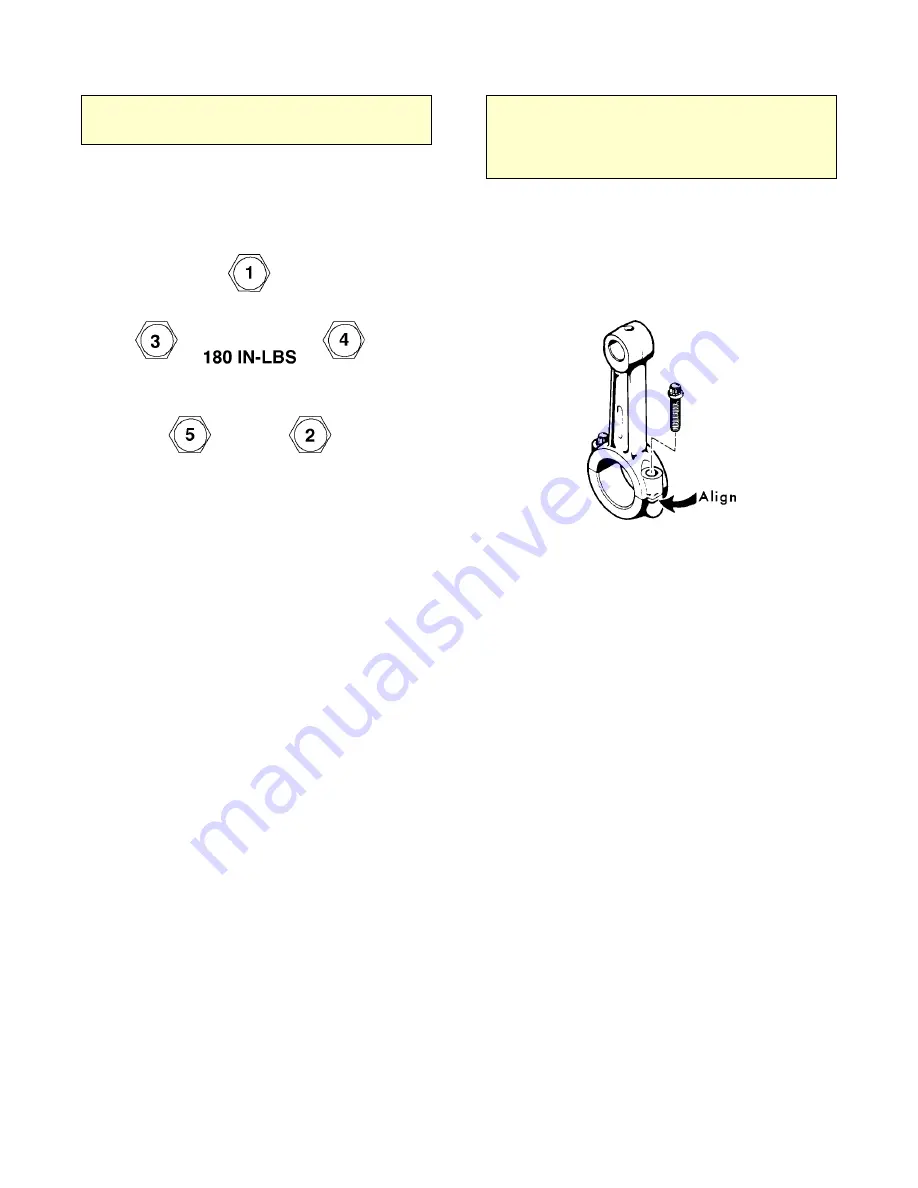
DA435HA: 99901219:
5-3
NOTE
THE CRANKSHAFT SHOULD HAVE NEW BEARINGS
INSTALLED. IF NOT, PRESS THE NEW BEARINGS
INTO POSITION ON THE CRANKSHAFT.
10. Generously oil the front bearing race and install
the front bearing housing with gasket. Torque the
bolts to 180 in-lbs. Torque the bolts as shown in the
pattern below.
11. Slide the crankshaft into the crankcase.
Generously lubricate the bearing race and install the
rear bearing housing and gaskets.
FIGURE E-3. BEARING HOUSING
TORQUE SEQUENCE
NOTE
GASKET KITS ARE SUPPLIED WITH TWO (2) EACH OF
.006, .010, .015, AND .020 GASKETS. USE THESE
REAR BEARING GASKETS IN ANY COMBINATION AND
QUANTITY TO LIMIT ALL PLAY FRONT TO REAR, BUT
STILL ALLOW THE CRANKSHAFT TO TURN FREELY.
12. Install the oil pump (See paragraph 5-3).
13. Install the connecting rods. Thoroughly oil the
crankshaft and rods before installing them. When
installing the rods, make certain that the tabs are
aligned on the same side of the rod as shown below.
14. Install the pistons, rings, heads and pulsation
tank.
FIGURE E-4. ROD ALIGNMENT
19980930