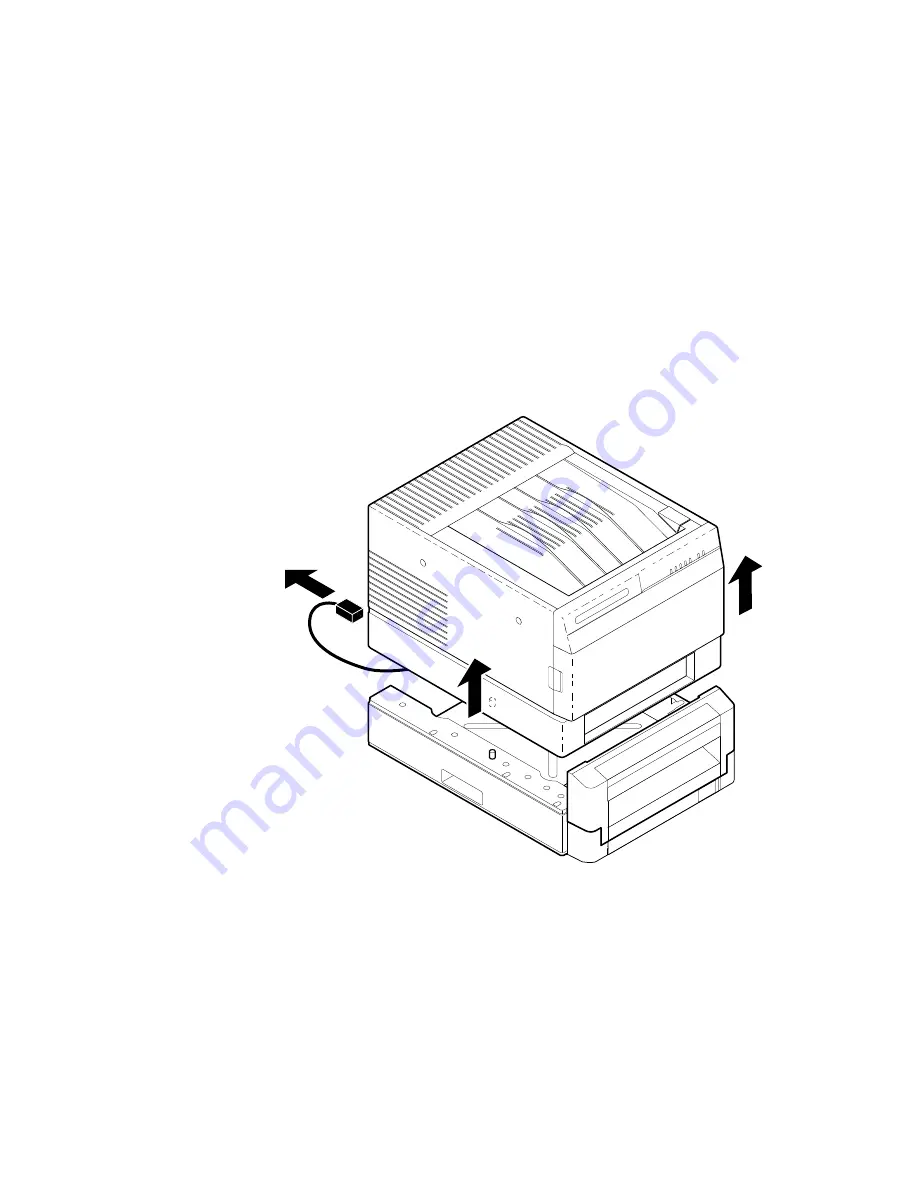
8-2
DECcolorwriter 1000
8
FRU Disassembly/Assembly
Lower tray assembly
The Lower Tray Assembly, sometimes referred to as the second feeder, is serviced and
replaced as a unit. Its construction and operation is very similar to the paper feed unit in
the print engine.
1.
Turn off the printer.
2.
Unplug the Lower Tray Assembly cable from the rear of the printer.
3.
Lift the printer off of the Lower Tray Assembly.
Reverse these steps to reinstall the Lower Tray Assembly making sure that the printer is
fully seated over the Lower Tray Assembly's guide pins.
Figure 8-1 Removing the Lower Tray Assembly
8699-56
3
3
2
Summary of Contents for DECcolorwriter 1000
Page 11: ...Service Manual xi...
Page 16: ...Service Manual xv...
Page 56: ...2 24 DECcolorwriter 1000 2 Installing the Printer and Drivers...
Page 64: ...3 8 DECcolorwriter 1000 3 Verifying the Printer and Host Connections...
Page 70: ...4 6 DECcolorwriter 1000 4 Key Operator Training...
Page 170: ...8 46 DECcolorwriter 1000 8 FRU Disassembly Assembly...
Page 190: ...9 20 DECcolorwriter 1000 9 Checks and Adjustments...
Page 195: ...Service Manual A 5 Field Replaceable Units List A...
Page 198: ...A 8 DECcolorwriter 1000 A Field Replaceable Units List...
Page 204: ...C 6 DECcolorwriter 1000 C Wiring Diagrams...
Page 208: ...D 4 DECcolorwriter 1000 D Test Pattern Generator...