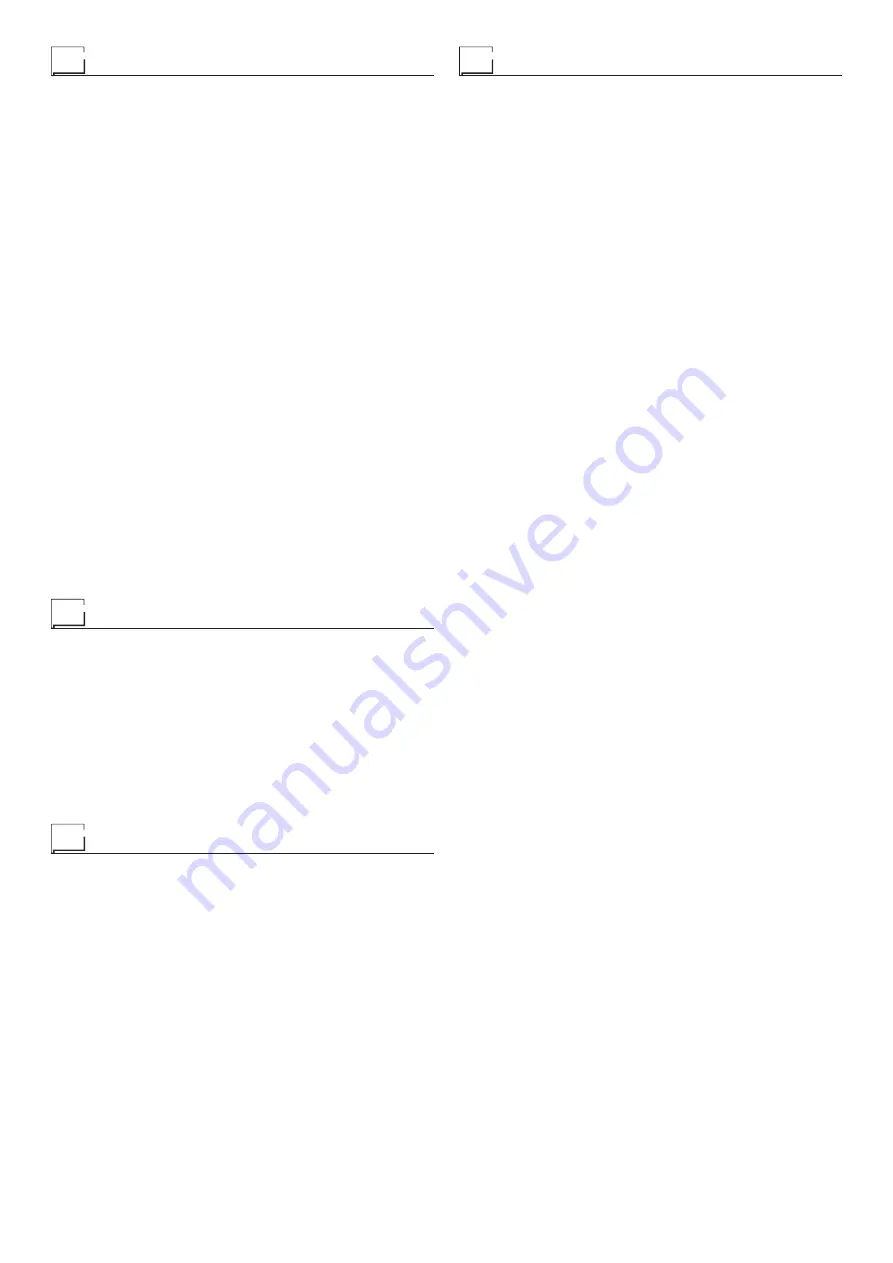
4
Optional
WARNING: The digital control unit of the welding power source
is fitted with a control recognition device which allows it to identify
which device is connected and take action accordingly.
REMOTE CONTROL ANALOG RC
This command:
•
Completely replaces the ENCODER - A knob on the DIX WF
793.M feeder’s front panel.
•
Partially (depending on the welding process selected) replac-
es the ENCODER - V knob on the DIX WF 793.M feeder’s front
panel.
AIR AND/OR WATER COOLED UP/DOWN TORCH
This command works as an alternative to:
•
The ENCODER - A knob on the DIX WF 793.M feeder’s front
panel. In “synergic” MIG MAG and “manual” MIG MAG welding
processes, by pressing the two right (+) and left (-) buttons you
can regulate the values for the synergic welding parameters.
•
The ENCODER - V knob on the DIX WF 793.M feeder’s front
panel. In the JOB welding process, by pressing the two right (+)
and left (-) buttons you can scroll the welding points set previ-
ously.
PUSH-PULL TORCH
The push-pull torch makes it possible to improve the aluminium
wire feed, using the motor on the torch itself. The parameters nor-
mally regulated using the ENCODER - A knob on the DIX WF
793.M feeder’s front panel, when this torch is on, are now regulat-
ed using the potentiometer on the torch itself.
DOUBLE FEEDER
Two feeders can be used, connected to the same welding power
source. Only the one activated by the corresponding torch button
will be available. It is
not
possible to weld with both simultaneous-
ly. For further details on installation, configuration and use, con-
tact your authorised dealer.
Maintenance and trouble shooting
SUPPLY WIRE FEEDER
The maintenance of this equipment is limited to the cleaning of
the inside of the frame and periodic inspection of worn cables or
loose connections. At regular intervals disconnect the welder from
the mains, take off the cover and use dry compressed air to re-
move possible accumulations of dirt and dust. During this opera-
tion do not direct the jet of air onto electronic components. Check,
that the gas circuit is completely free from impurities and that the
connections are tight and that there are no leaks. Carefully check
that the electric valve does not leak. Check the wire feeder rolls
periodically and replace them when wear impairs the regular flow
of the wire (slipping etc).
Replacing the motor control board
Proceed as follows:
•
Unscrew the 4 screws on the sides of the panel to loosen it.
•
Extract the panel pulling it towards you with a gentle movement.
•
Extract the back connectors.
•
Unscrew the 4 nuts at the sides of the electronic control board.
•
Unscrew the two nuts that secure the encoders.
•
Remove the faulty card.
•
Proceed the other way round for reassembly.
Simple automation
This paragraph describes how to interface the welding power
source with an automatic welding plant. The connection signs are
marked and available on the “17-pole connector for accessory /
optional extra connections” (Connector
CA
- see the “Wiring dia-
gram” and “Wiring Diagram Legend” paragraphs).
DIGITAL INPUTS
Activating a digital input signal means applying a clean closed
contact to it.
• TORCH BUTTON • Terminals
C / D (COM)
When this signal is activated, the welding power source starts
the welding process.
• UP SIGNAL • Terminals
D (COM) / F
When this signal is activated, the welding power source increas-
es the value set beforehand for the welding synergy parameters.
• DOWN SIGNAL • Terminals
D (COM) / E
When this signal is activated, the welding power source decreas-
es the value set beforehand for the welding synergy parameters.
ANALOGUE INPUTS
These inputs must be piloted by a direct voltage that can be regu-
lated between 0V and 10V.
Their input impedance exceeds 400 kΩ (to enable functionality of
these inputs the voltage between terminals
P(-)
and
R (+)
must
exceed 0,5V).
• PARAMETER REGULATION - A • Terminals
P(-) / R (+)
By regulating the voltage on this input between 1V and 10V the
welding synergy parameters (WELDING WORKPIECE THICK-
NESS, WELDING CURRENT, WIRE SPEED) are regulated from
the minimum to the maximum value.
• PARAMETER REGULATION - V • Terminals
P(-) / S (+)
By regulating the voltage on this input between 1V and 10V
the welding parameters (ARC LENGTH, WELDING VOLTAGE,
ELECTRONIC INDUCTANCE) are regulated from the minimum
to the maximum value.
DIGITAL OUTPUTS
Activating digital output signals means closing a clean contact.
• ARC ON • Terminals
T / L
The welding power source activates this signal when it detects
current passing through the welding circuit.
Summary of Contents for DIX WF 793.M
Page 6: ...6 Wiring diagram 2101FB65...