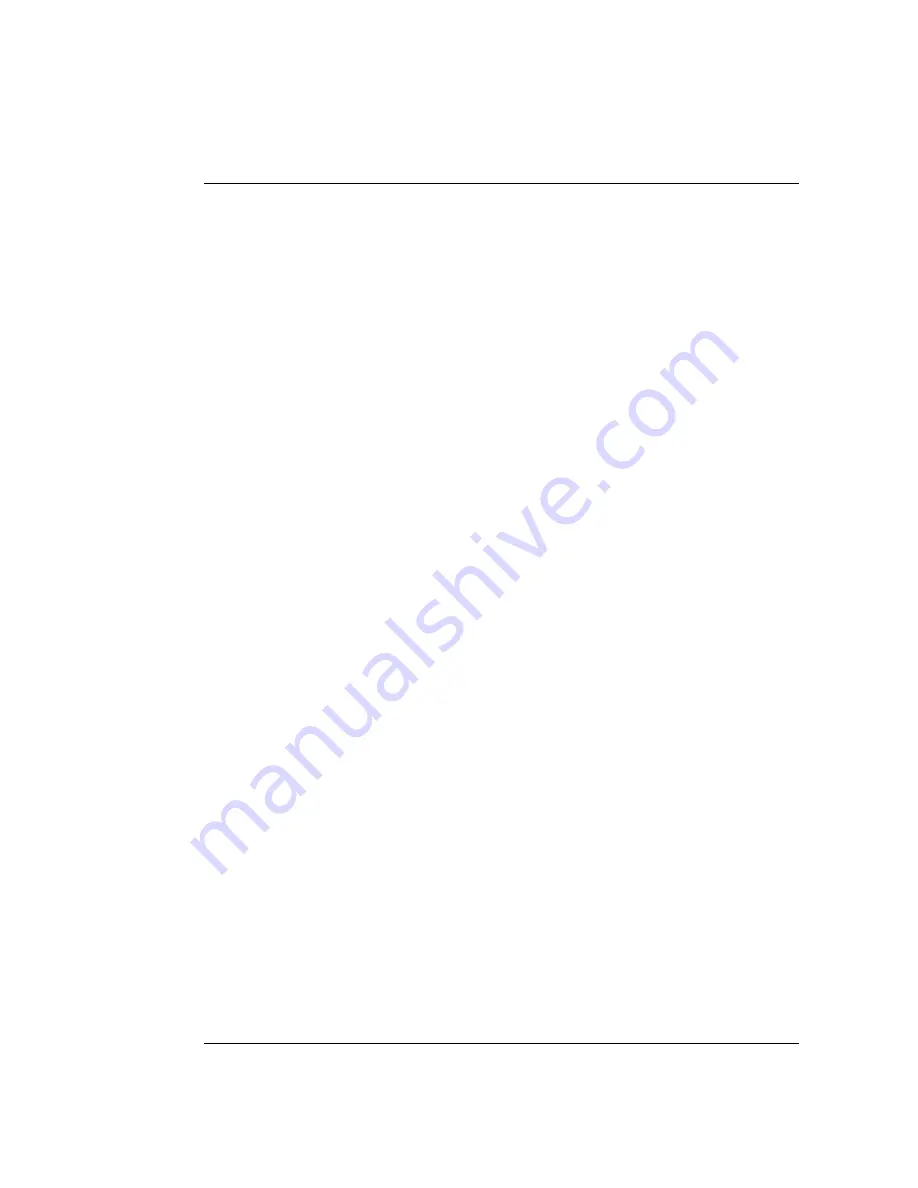
The LC20 Ship Kit includes two accessories for the
Rheodyne injection valves: a 25
µ
L gas-tight syringe
(P/N 041389) and a 25
µ
L sample loop (P/N 042857). For
more information about the valve, including important
operating precautions, refer to the Rheodyne Valve Operator’s
Manual (Document No. 034468), included in the LC20 Ship
Kit.
2.3.3 Self-Regenerating Suppressor
The Self-Regenerating Suppressor (SRS
) is held in place
by a special support plate. Align the two slots on the bottom
of the SRS case with the tabs on the support plate. Press in
and then down to lock the SRS in place. Pull up and then out
to remove (see Figure B-8 in Appendix B).
2.3.4 Leak Sensor
This sensor detects leaks and spills in the bottom of the
enclosure, and generates a signal when a leak occurs. The
sensor is located at the lower front corner of the left wall in
the bottom tray. Its cable exits through the rear service chase,
and must be connected to the GP40 pump.
2.3.5 Separator Columns
The column mount near the front of the component panel can
accommodate up to two separator columns. The column
mount supports 4-mm columns on one side and 2-mm
columns on the other. The column mount can be removed by
pressing on each side of its mounting tab and pulling away
from the slot in the panel. You can then reverse it and press it
back into the panel to change column size and maintain the
columns at the outer position (see Figure B-7 in Appendix B).
2.3.6 Guard Columns
The smaller guard columns (if used) are held in place by the
tubing below the separator columns.
2
•
Description
Doc. 034859-02 9/93
2-7
Summary of Contents for LC20
Page 6: ...Contents iv Doc 034859 02 9 93 ...
Page 8: ...LC20 Chromatography Enclosure 1 2 Doc 034859 02 9 93 ...
Page 12: ...LC20 Chromatography Enclosure 2 2 Doc 034859 02 9 93 ...
Page 24: ...LC20 Chromatography Enclosure 2 14 Doc 034859 02 9 93 ...
Page 26: ...LC20 Chromatography Enclosure 3 2 Doc 034859 02 9 93 ...
Page 29: ...Figure 3 7 Drawing Sample 3 Operation and Maintenance Doc 034859 02 9 93 3 5 ...
Page 32: ...LC20 Chromatography Enclosure 3 8 Doc 034859 02 9 93 ...
Page 34: ...LC20 Chromatography Enclosure 4 2 Doc 034859 02 9 93 ...
Page 40: ...LC20 Chromatography Enclosure 4 8 Doc 034859 02 9 93 ...
Page 42: ...LC20 Chromatography Enclosure 5 2 Doc 034859 02 9 93 ...
Page 50: ...LC20 Chromatography Enclosure 5 10 Doc 034859 02 9 93 ...
Page 52: ...LC20 Chromatography Enclosure A 2 Doc 034859 02 9 93 ...
Page 56: ...LC20 Chromatography Enclosure B 2 Doc 034859 02 9 93 ...
Page 65: ...Figure B 6 Electrochemical Cell Plumbing Schematic B Installation Doc 034859 02 9 93 B 11 ...