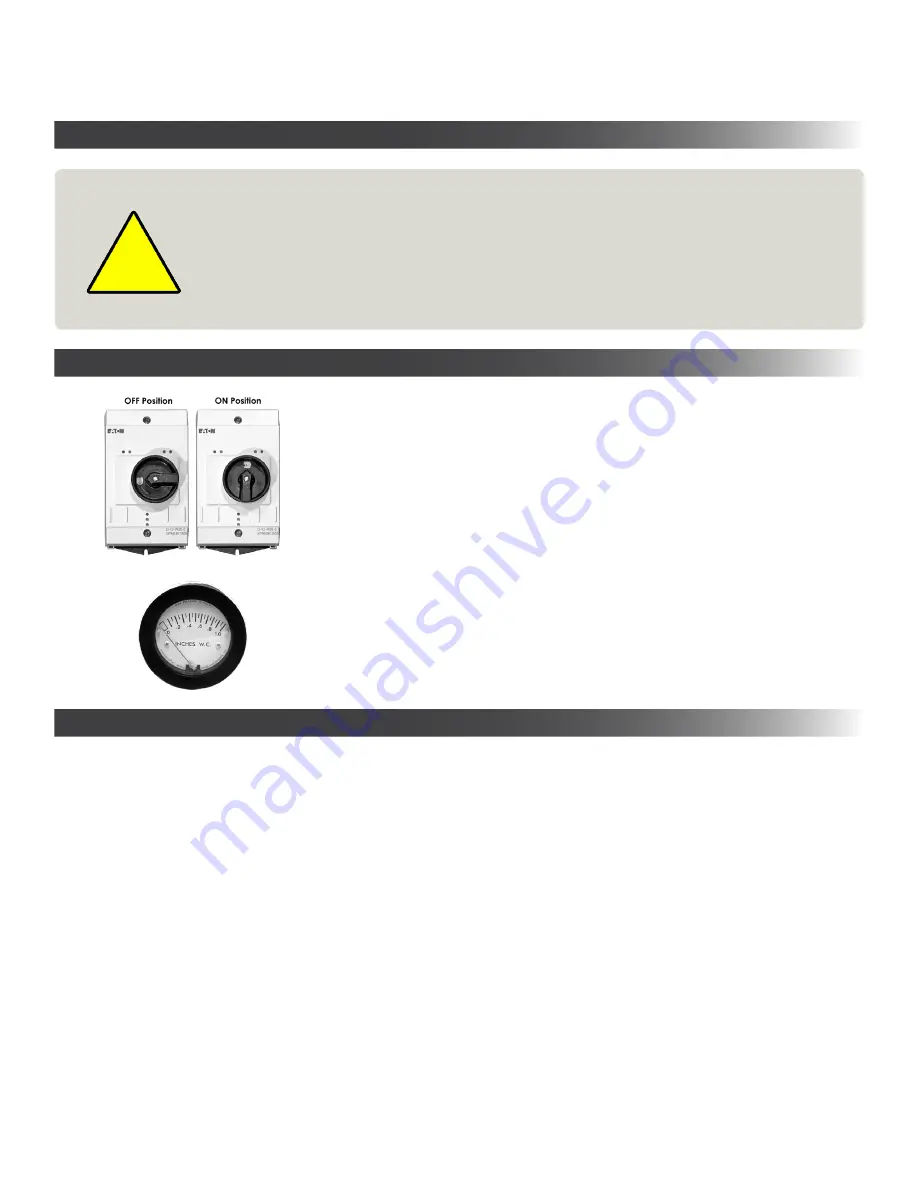
!
8
4.2 Controls
4.1 To Operate Safely
4.3 Pre-Use Checklist
• Read and understand
SECTION 1: Safety Precautions
and ensure
SECTION 3: Pre-Installation
has been followed.
• Before plugging unit in to an input power source, look at the manufacturer’s label located on the exterior of the unit
and ensure the source is correctly sized in terms of Voltage and Amperes.
• Prior to use in your application, turn the unit ON, and perform a function test. To do so:
1. LOOK: Have the front and back doors been closed properly.
2. Turn switch to ON position.
3. LOOK: Is the unit level, stable, and that nothing is obstructing the extraction path.
4. LISTEN: Does the motor and suction sound smooth and within expected volumes.
5. FEEL: Place your hand on top of the unit and sense for unexpected vibration. Place you hand in front of
the intake hood/surface and sense for expected level(s) of suction.
• Inform all potential users of this equipment where they may find and review this manual.
• The machine controls are basic, and consist solely of a power switch with ON and OFF positions.
• If the machine is equipped with a Minihelic differential pressure gauge, the Minihelic should
read between .8 and 4.2 inches W.C. during normal operation.
• For a reading of more than 4 inches W.C, consult
SECTION 5: Maintenance
and Troubleshooting
as filter servicing may be required.
• Read and understand
SECTION 1: Safety Precautions
and
SECTION 4: Operation before use
• Read and understand all Material Safety Data Sheets and Manufacturer’s instructions of all
process materials, consumables, and equipment used in conjunction with this equipment.
• Keep away from all mechanical moving parts including motor, gears, and other pinch points.
• Do not use product without first confirming if a Spark Arrestor is required and installed for
the type of dust, or fumes you are extracting and/or collection. If you are unsure, call a
Diversitech representative at 1-800-361-3733.
SECTION 4 - OPERATION
Summary of Contents for FRED SR
Page 22: ...22 NOTES...
Page 23: ...NOTES 23...