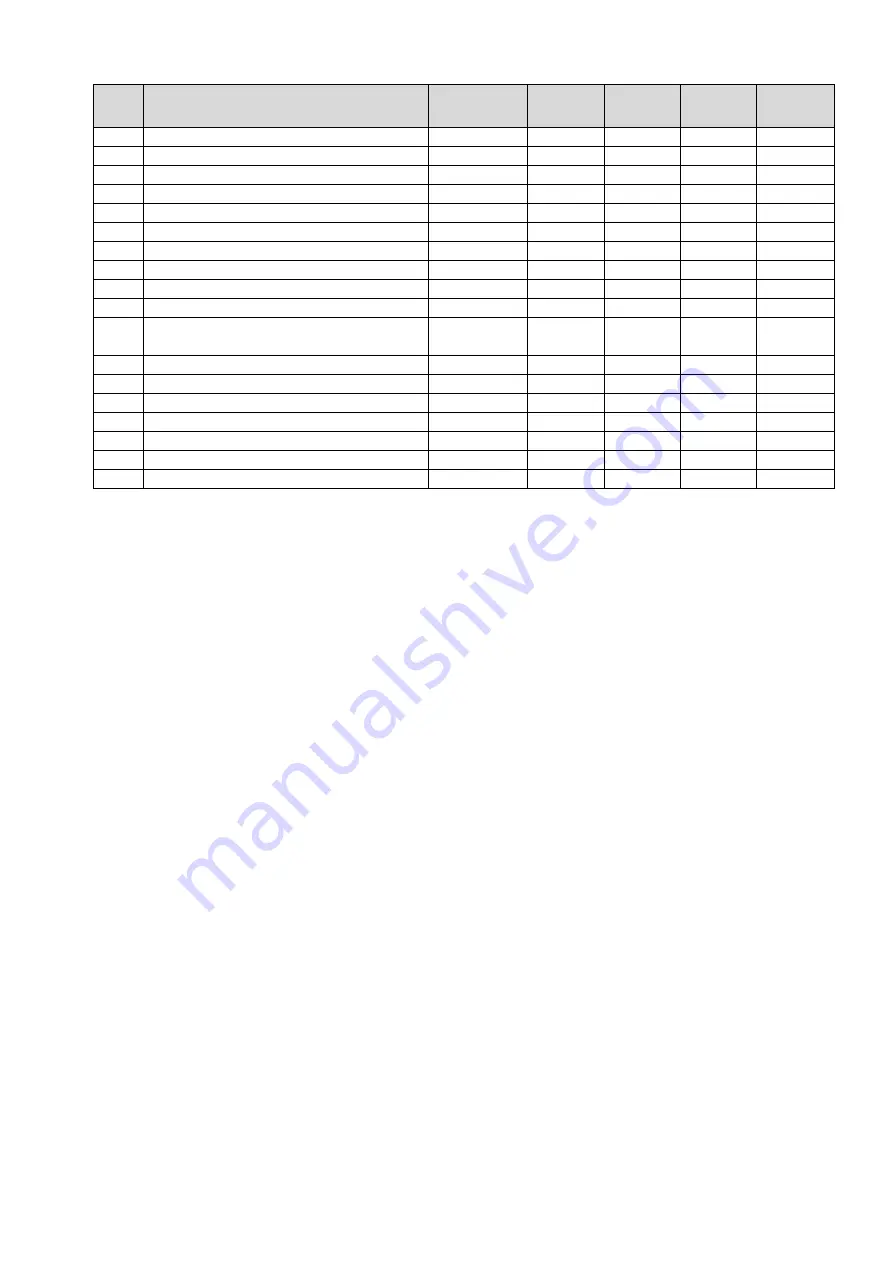
SuperSigma2 AM PMS
–
V1.5.6 17-1-2020
Page 43 (97)
©2019 DMC GmbH Herten Germany
3.2
Menu 1 “Pump Adjustments”
Cal.
Ref.
Parameter
Calibrator
Text
Min.
adjust
Max.
adjust
Step size
Default
1
Acceleration delay
"Accel "
0,1 s
10 s
0,1 s
2,5 s
2
Deceleration delay
"Decel "
0,1 s
10 s
0,1 s
0,3 s
3
Creep speed
"Creep "
0,1 Hz
600 Hz
0 Hz
0 Hz
4
Creep speed Ramp
“CreepRmp”
0,1 s
10,0 s
0,1 s
2,5 s
5
Maximum pot speed 1
"Potmax1 "
0,1 Hz
600 Hz
0 Hz
0 Hz
6
Speed 2 demand
"Pspeed2 "
0,1 Hz
600 Hz
0 Hz
0 Hz
7
Speed 3 demand
"Pspeed3 "
0,1 Hz
600 Hz
0 Hz
0 Hz
8
Speed 4 demand
"Pspeed4 "
0,1 Hz
600 Hz
0 Hz
0 Hz
9
Speed 5 demand
"Pspeed5 "
0,1 Hz
600 Hz
0 Hz
0 Hz
10
Speed 6 demand
"Pspeed6 "
0,1 Hz
600 Hz
0 Hz
0 Hz
11
Minimum motor speed in cutback
conditions
"MinSpeed"
0,1 Hz
600 Hz
0 Hz
40 Hz
12
Acceleration for speed 6 demand (pwrStr)
"Paccel6 "
0,1 s
10 s
0,1 s
5 s
13
Power steer delay
"PStrDly "
0 s
50 s
0 s
5 s
14
Accelerator pot minimum
“AccMin”
0 V
10 V
0 V
0,2 V
15
Accelerator pot maximum
“AccMax”
0 V
10 V
0 V
4,6 V
16
Speed threshold to enter end of braking
“SpdThEbM”
0 %
50 %
0,1 %
5 %
17
Ramp time from SpdThEbMto zero
“SpdRmpTm”
0,1 s
10 s
0 s
1,5 s
18
Zero Speed threshold to end braking
“ZSpdTh”
0 %
10,0%
0,1 %
1,0 %
M1-1P
Acceleration delay “Accel”
This sets the time taken to accelerate from zero speed to maximum speed. The maximum speed demand is set by
. Increasing the value results in a slower pump response, while decreasing the value
results in a faster pump response.
M1-2P
Deceleration delay ”Decel”
This sets the time taken to decelerate from maximum speed to zero speed. Increasing the value results in a slower pump
deceleration, while decreasing the value results in a faster pump deceleration.
M1-3P
Creep speed ”Creep”
This effectively sets the initial speed that the pump will adopt on entering drive.
Increasing the value will help minimize any delay from selecting drive to creeping the pump. The value relates to the
motor speed, i.e. the motor’s rotor frequency.
M1-4P
Creep
speed Ramp “CreepRmp”
This parameter sets the ramp time for applying creep speed.
M1-5P
Maximum pot speed 1 ”Potmax1”
This sets the pump speed when the switch wired to pin 1 of 35-way Connector is active.
When the pump potentiometer is active, this speed demand has the highest priority and overrides all other speed
requests, except for the power steer trigger input (pin 6 of 35-wy connector). When the power steer trigger input is active,
the current speed demand will be the higher between Speed 1 and Speed 6. The pump motor will accelerate or decelerate
to the new speed demand using the programmed Acceleration and Deceleration rates.
M1-6P
Speed 2 demand ”Pspeed2”
This sets the pump speed when the switch wired to pin 2 of 35-way Connector is active.
When pump speed 2 is active and the pump potentiometer is not active, it will override all other speed requests, except
for the power steer trigger input (pin 6 of 35-wy connector). When the power steer trigger input is active, the current
speed demand will be the higher between Speed 2 and Speed 6. The pump motor will accelerate or decelerate to the new
speed demand using the programmed Acceleration and Deceleration rates.
M1-7P
Speed 3 demand ”Pspeed3”
This sets the pump speed when the switch wired to pin 3 of 35-way Connector is active.
When pump speed 3 is active and the pump potentiometer and Speed 2 are not active, it will override all other speed
requests, except for the power steer trigger input (pin 6 of 35-wy connector). When the power steer trigger input is active,
the current speed demand will be the higher between Speed 3 and Speed 6. The pump motor will accelerate or decelerate
to the new speed demand using the programmed Acceleration and Deceleration rates.