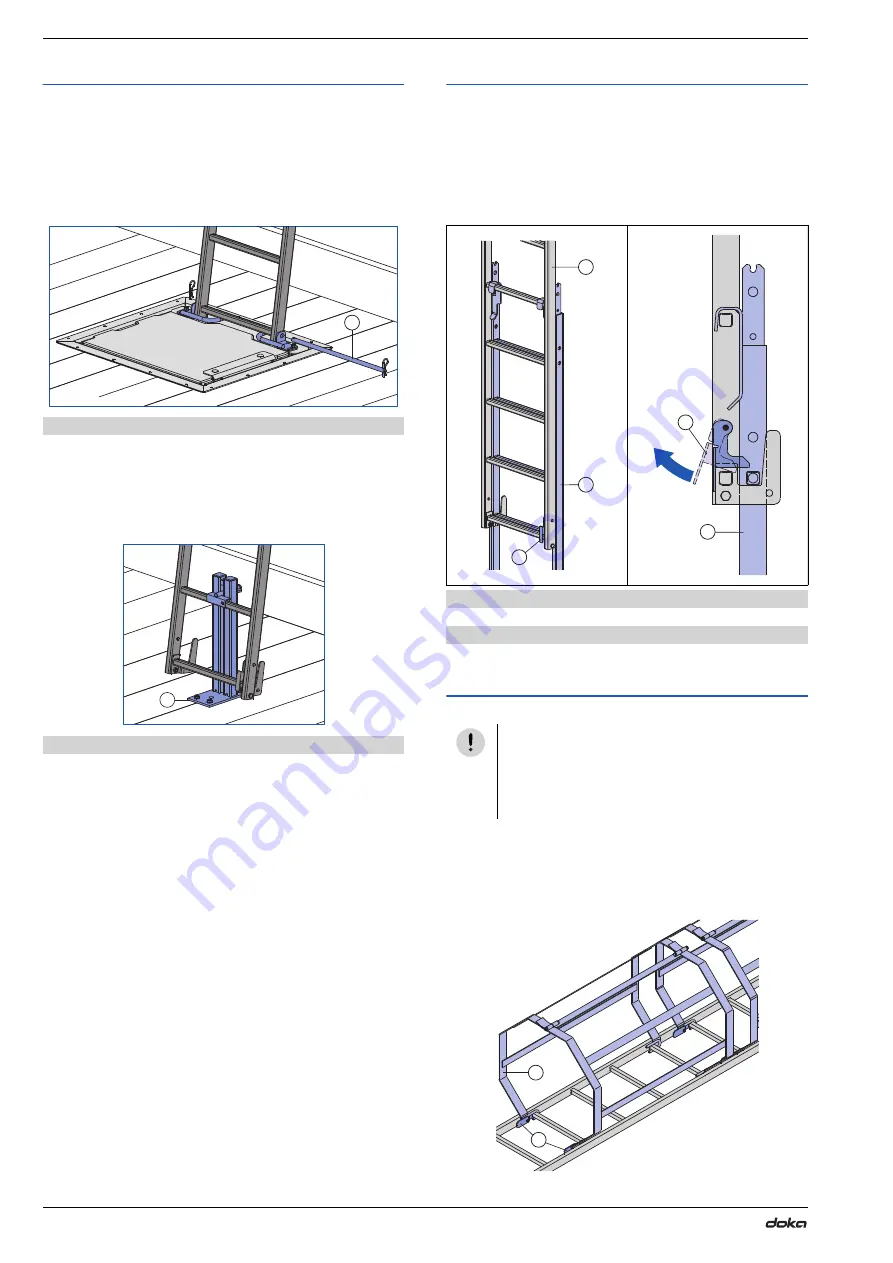
56
999775002 - 02/2020
General
User Information
Climbing formwork 150F
Attaching the ladders
Manhole B 70/60cm
➤
Fix the System ladder XS 4.40m to the manhole with
a ladder stirrup.
➤
Insert a Ladder bolt XS through the rung of the lad-
der and secure it on both sides with a d4 spring cot-
ter.
➤
Screw the Ladder adapter XS to the platform deck-
ing.
➤
Fix the bottom of the ladder to the Ladder adapter
XS.
Lengthening the ladder
Telescoping ladder extension (for adjusting to
ground level)
➤
To telescope the ladders past one another, lift the
safety latch on the ladder and fix the Ladder exten-
sion XS 2.30m onto the desired rung of the other lad-
der.
Ladder cage
➤
Fix the Ladder cage XS 1.00m
(E)
onto the next
available rung. The safety latches
(F)
prevent the
cage being accidentally lifted out. Add further Ladder
cages
XS
1.00m, in each case fixing them onto the
next available rung.
F
Ladder bolt XS
D
Ladder adapter XS
F
98010-337-01
98010-337-02
D
B
System ladder XS 4.40m
C
Ladder extension XS 2.30m
G
Safety latch
NOTICE
➤
Always observe all relevant safety regula-
tions applying to the use of the Ladder cage
XS in the country in which you are operating
(e.g. in Germany: BGV D 36).
9766-273-02
G
B
C
Tr625-201-03
G
C
Tr625-201-02
F
E
Summary of Contents for 150F
Page 2: ...2 999775002 02 2020 User Information Climbing formwork 150F ...
Page 26: ...26 999775002 02 2020 Anchoring on the structure User Information Climbing formwork 150F ...
Page 34: ...34 999775002 02 2020 Repositioning User Information Climbing formwork 150F ...
Page 52: ...52 999775002 02 2020 Assembly User Information Climbing formwork 150F ...