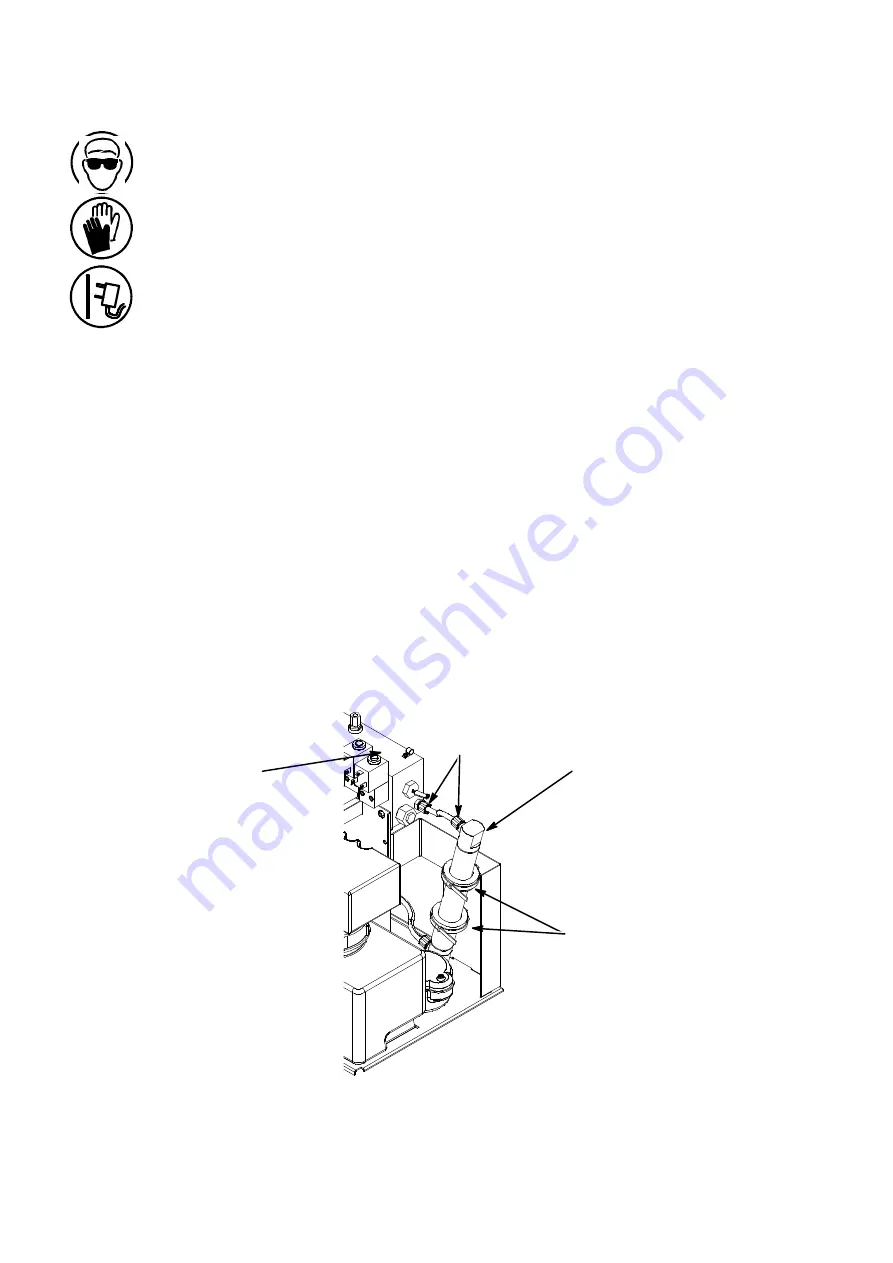
REPAIR
8--34
27080 Issue 1 Sept 98
Note:
Tools required:
Lint--free tissue to catch any escaping ink.
Adjustable spanner (see step (4)).
Protective clothing (especially safety glasses).
The printer must be shut down and the cartridges removed.
(1) Remove the securing screw and pull out the ink system.
(2) Disconnect the viscometer wiring from the ink interface PCB.
(3) Pull the viscometer out of its clips by squeezing each tab and
releasing the clip.
(4) Disconnect the ink tubes from the viscometer and trim the used end
part (approx. 5--6mm) of the tubes, then transfer to the new
viscometer. The tubes must be connected so that when the new
viscometer is fitted into the clips, the tube connectors face the block
(see diagram), the wires must come out of the bottom of the
viscometer.
(5) Fit the new viscometer into the clips and connect the wiring to the
ink interface PCB.
(6) Refit the ink system and the cartridges.
The replacement is now complete. Check for leaks when the printer is
next started up. If a viscometer fault is shown, ensure that the
viscometer is fitted correctly.
Summary of Contents for A-SERIES
Page 1: ...DOMINO A SERIES INK JET PRINTER OPERATION AND MAINTENANCE MANUAL ...
Page 6: ... 6 27080 Issue 1 Sept 98 ...
Page 8: ... 8 27080 Issue 1 Sept 98 ...
Page 10: ... 10 27080 Issue 1 Sept 98 ...
Page 12: ...HEALTH AND SAFETY 1 2 27080 Issue 1 August 98 ...
Page 18: ...HEALTH AND SAFETY 1 8 27080 Issue 1 August 98 ...
Page 20: ......
Page 21: ......
Page 22: ......
Page 36: ...OPERATION 3 2 27080 Issue 1 August 98 ...
Page 55: ...DISPLAY MESSAGES AND FAULT FINDING 4 2 27080 Issue 1 August 98 ...
Page 76: ...REFERENCE 5 4 27080 Issue 1 August 98 ...
Page 136: ...PRINTER DESCRIPTION 6 20 27080 Issue 1 September 98 ...
Page 137: ...DESCRIPTION 27080 Issue 1 August 98 6 21 Wiring Diagram 37700W Iss 1 PELTI ER ...
Page 138: ...DESCRIPTION 6 22 27080 Issue 1 August 98 ...
Page 140: ...MAINTENANCE 7 2 27080 Issue 1 Sept 98 ...
Page 142: ...MAINTENANCE 7 4 27080 Issue 1 Sept 98 ...
Page 156: ...MAINTENANCE 7 18 27080 Issue 1 Sept 98 ...
Page 158: ...REPAIR 8 2 27080 Issue 1 Sept 98 ...
Page 192: ...REPAIR 8 36 27080 Issue 1 Sept 98 ...
Page 208: ...SPARES AND ACCESSORIES 9 16 27080 Issue 1 Sept 98 Electronics Inner Door 1 2 3 4 5 6 7 ...
Page 212: ...SPARES AND ACCESSORIES 9 20 27080 Issue 1 Sept 98 ...
Page 214: ...OPTIONS 10 2 27080 Issue 1 Sept 98 ...
Page 240: ...OPTIONS 10 28 27080 Issue 1 Sept 98 ...
Page 242: ...APPENDIX A INSTALLATION A 2 27080 Issue 1 Sept 98 ...
Page 261: ...APPENDIX B COMPRESSOR DRIVEN AIRDRYER B 2 20950 Issue 1 April 98 ...
Page 311: ...APPENDIX B A SERIES AIR DRIVEN AIRDRYER B 2 20951 Issue 1 Apr 98 ...
Page 313: ...APPENDIX B A SERIES AIR DRIVEN AIRDRYER B 4 20951 Issue 1 Apr 98 ...