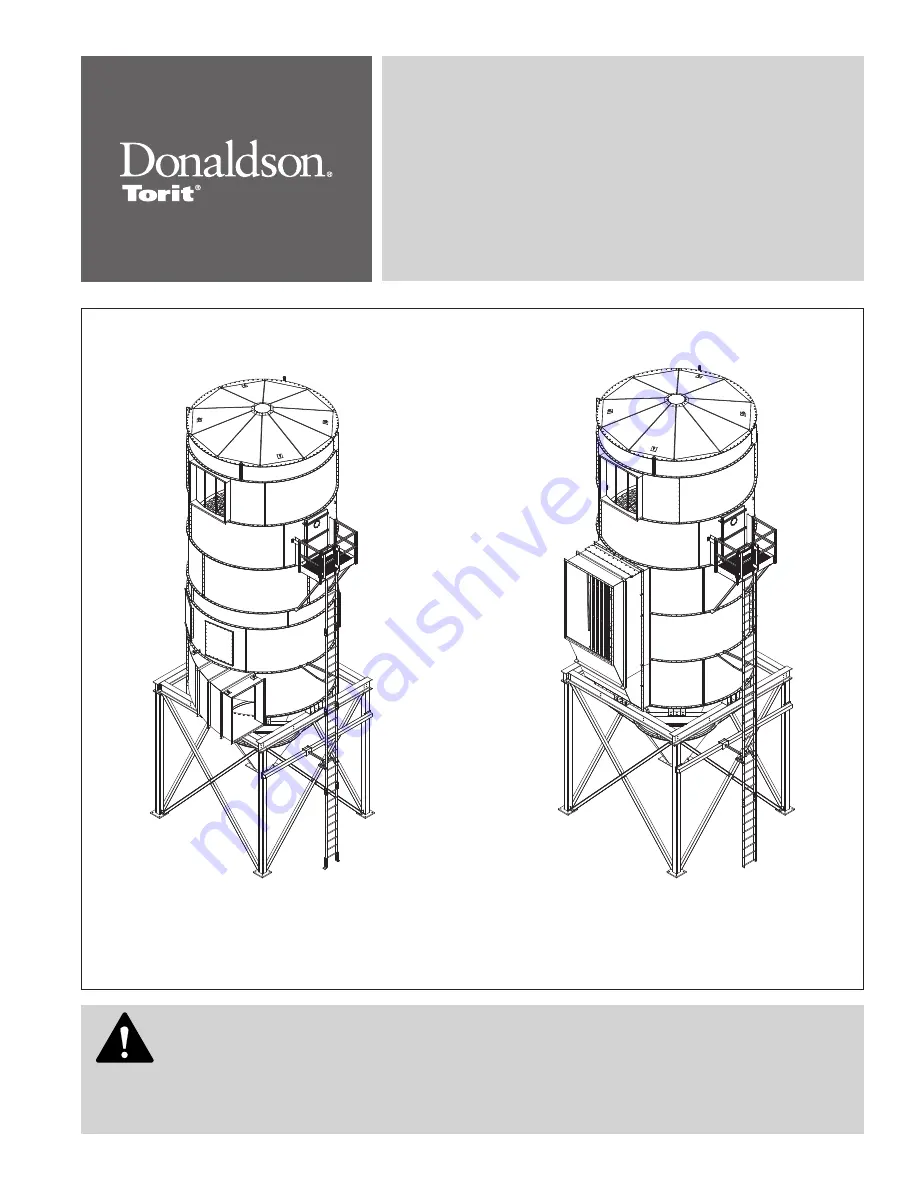
RF Baghouse Dust Collector
Models RFWP and RFWPH
Installation and Operation Manual
Installation, Operation, and Service Information
Model RFWP
Model RFWPH
This manual contains specific precautions related to worker safety. The hazard alert image denotes safety
related instructions and warnings in this manual. DO NOT install, operate, or perform maintenance on this
collector until you have read and understood the instructions, precautions and warnings contained within this
manual.
IOM AD3670201 (ENG)
Revision 4
English
Master Language