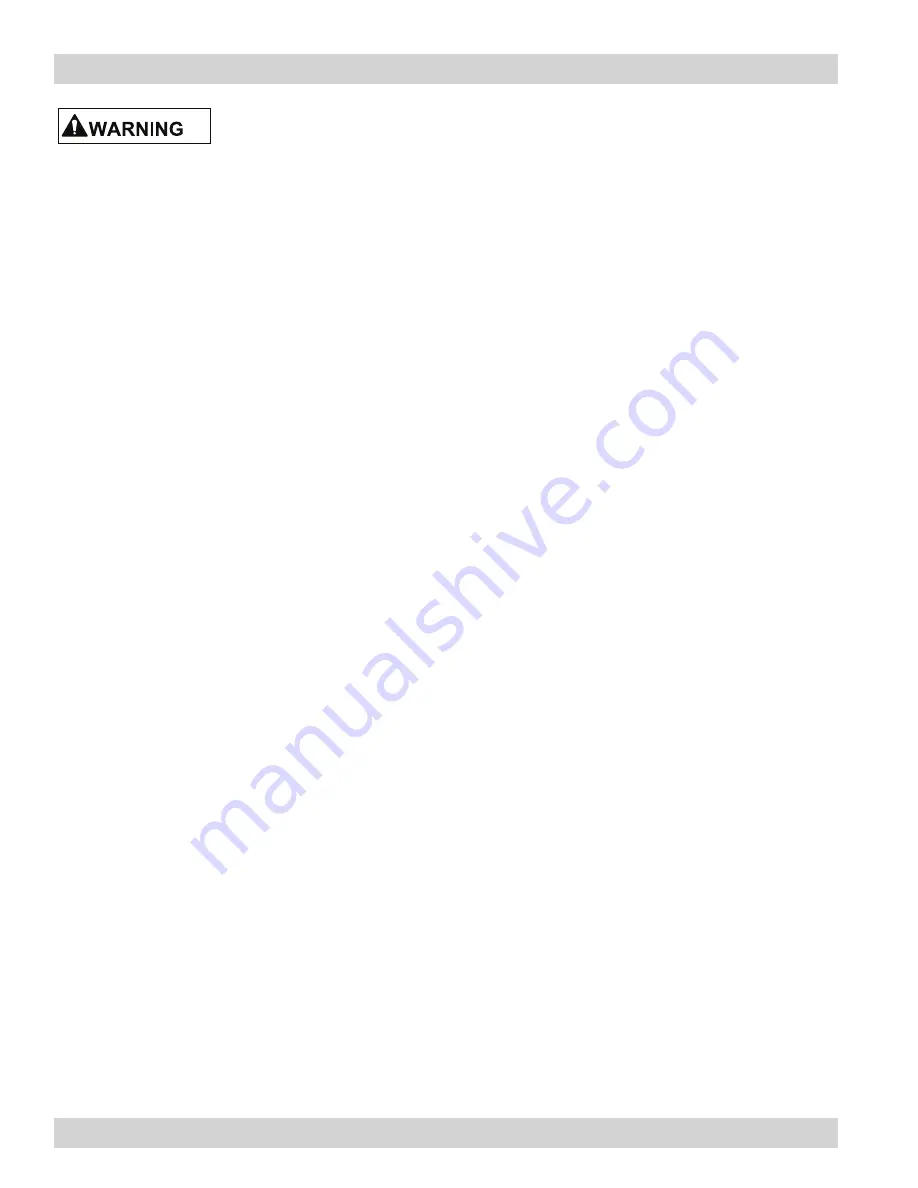
Donaldson Company, Inc.
Process owners/operators have important responsibilities relating to combustible hazards.
Process owners/operators must determine whether their process creates combustible
dust, fume, or mist. If combustible dust, fume, or mist is generated, process owners/operators should at a
minimum:
• Comply with all applicable codes and standards. Among other considerations, current NFPA standards
require owners/operators whose processes involve potentially combustible materials to have a current
Hazard Analysis, which can serve as the foundation for their process hazard mitigation strategies.
• Prevent all ignition sources from entering any dust collection equipment.
• Design, select, and implement fire and explosion mitigation, suppression, and isolation strategies that
are appropriate for the risks associated with their application.
• Develop and implement maintenance work practices to maintain a safe operating environment, ensuring
that combustible dust, fume, or mist does not accumulate within the plant.
Donaldson recommends process owners/operators consult with experts to insure each of these
responsibilities are met.
As a manufacturer and supplier of Industrial Filtration Products, Donaldson can assist process owners/
operators in the selection of filtration technologies. However, process owners/operators retain all
responsibility for the suitability of fire and explosion hazard mitigation, suppression, and isolation strategies.
Donaldson assumes no responsibility or liability for the suitability of any fire and/or explosion mitigation
strategy, or any items incorporated into a collector as part of an owner/operators hazard mitigation strategy.
Improper operation of a dust control system may contribute to conditions in the work area or facility that
could result in severe personal injury and product or property damage. Check that all collection equipment is
properly selected and sized for the intended use.
DO NOT operate this equipment until you have read and understand the instruction warnings in the
Installation and Operations Manual. For a replacement manual, contact Donaldson Torit.
This manual contains specific precautionary statements relative to worker safety. Read thoroughly and comply
as directed. Discuss the use and application of this equipment with a Donaldson Torit representative. Instruct all
personnel on safe use and maintenance procedures.