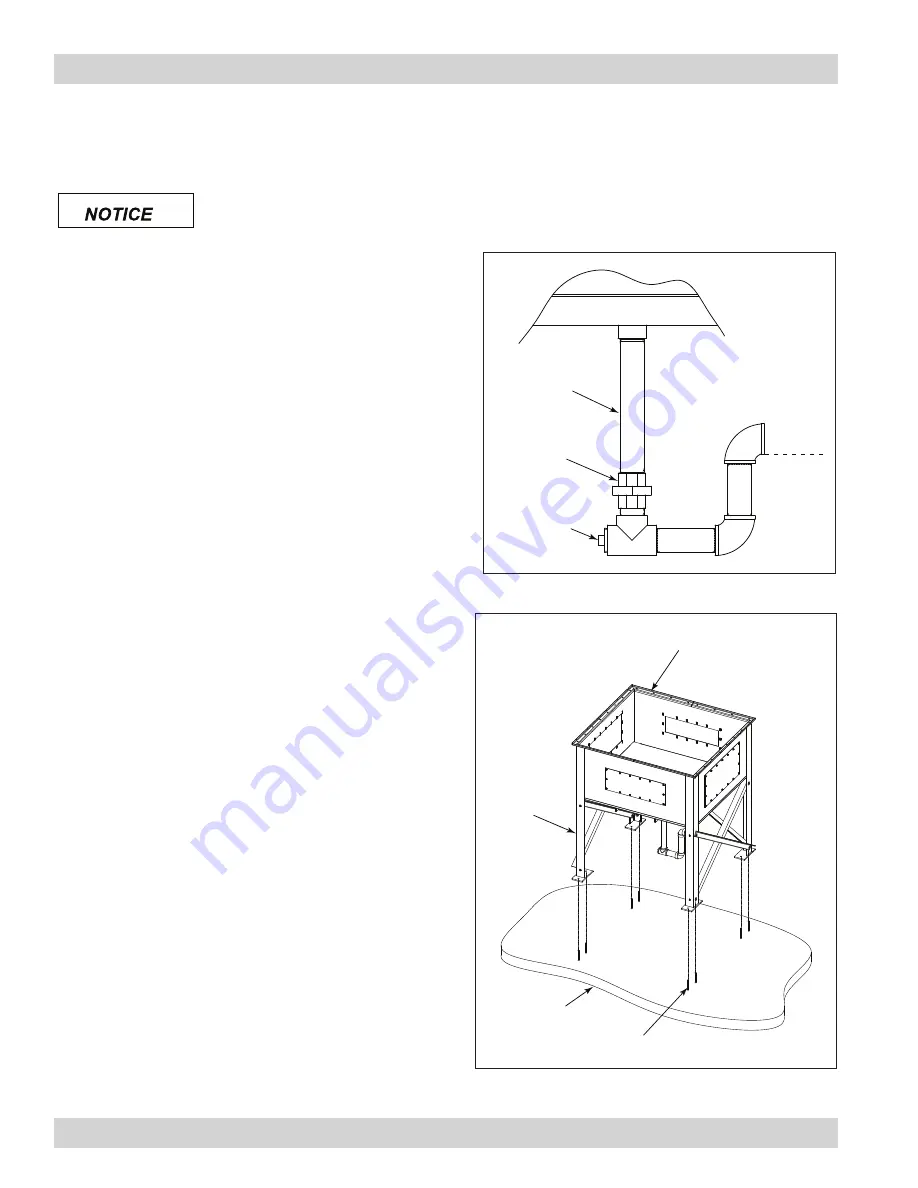
Donaldson Company, Inc.
17
Inlet Plenum Installation
Reference Typical Foundation Anchor and leg assembly drawing
shipped with the collector prior to starting assembly.
1. Prepare the foundation or support framing in the selected
location. Locate and install anchors.
2. Using a crane or forklift, raise the inlet plenum to the required
height.
Note: When using a crane, use clevis pins and a sling
attached to four lifting lugs.
3. Lower the inlet plenum with legs to the anchor bolts.
4. Level inlet plenum and secure all hardware.
5.
Apply supplied sealant to the top flange of the inlet plenum.
6.
Remove the first stage and primary filters from the filter cabinet
and set aside.
7.
Using a crane or forklift, raise the filter cabinet section to
the required height. See below illustration for correct lifting
orientation.
8.
Set cabinet on top of the inlet plenum flange and attach with the
supplied fasteners.
9. Remove crane or forklift.
10.
Re-install the first stage and primary filters.
Inlet Plenum Installation, WSO 25-4 shown
leg
foundation
anchor bolt
inlet plenum
P-Trap Installation
Ensure collected material properly flows through the P-Trap. The P-Trap dimensions should
accommodate a column of coolant greater than the static capacity of the fan to avoid coolant pooling in
the collector and potentially causing property damage.
1. Install the P-Trap as shown in P-Trap Installation.
2. Position the P-Trap outlet to the proper location and tighten the
union.
3. Plumb the P-Trap to a receptacle or install a return line back to
the machine center.
4. Fill P-Trap before starting collector.
Note: The characteristics of some machining fluids change
with time, use, and exposure to air. Check the condition
of the collected fluid before re-using.
P-Trap Installation
maximum
fill level
hopper
NPT pipe
union
pipe plug