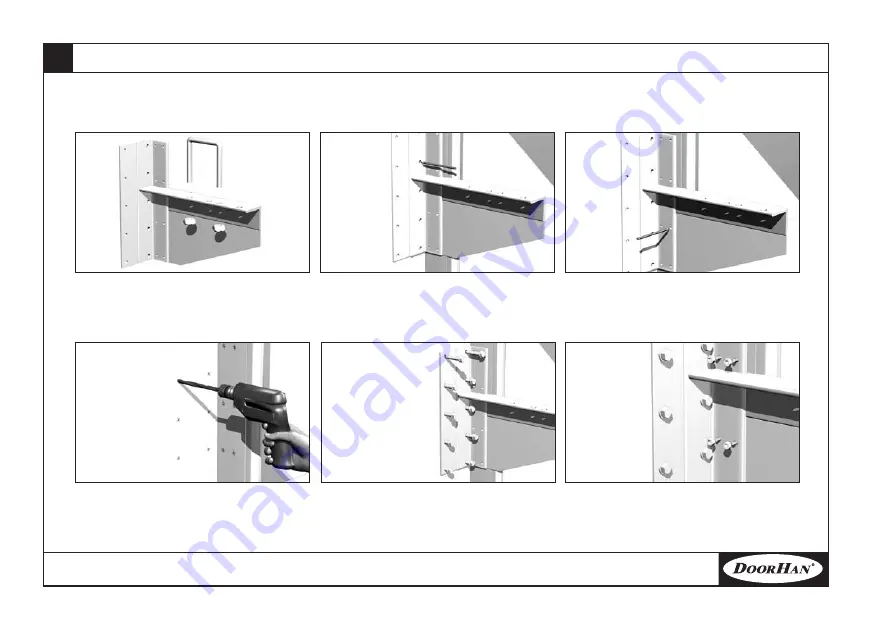
74
i n s t a l l a t i o n o f g a r a g e a n d i n d u s t r i a l s e c t i o n a l d o o r s
9
suPPLEmEnt
Mounting of the torsion gear with cylindrical shaft
disassemble the remote shaft bracket with
a cramp
lean the remote bracket for the low shaft to the embrasure wall close to the corner support
(on the outside) according to the mounting card . using perforation in the bracket make
marking for its fastening to the wall and the corner bracket .
drill according to the marking 10 holes
∅
12
mm in the embrasure wall and 8 holes
∅
7
mm in the corner support .
fasten the bracket to the wall using dowels and tapping screws and to the corner support
using bolted joints . install the second bracket on other side of the embrasure in a similar
manner .