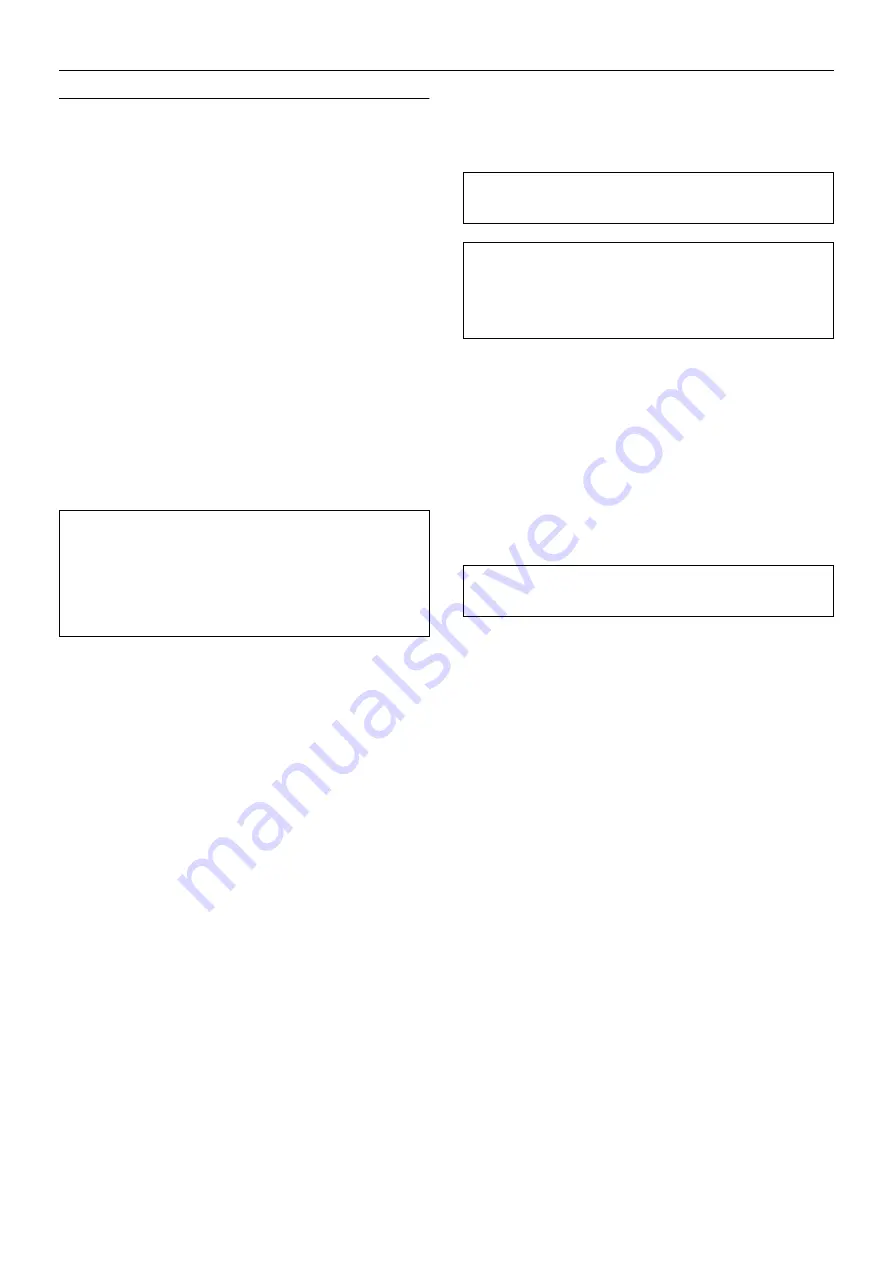
MAINTENANCE
77
7/124 - 10/104, 10/124 - 14/114, 14/84
LUBRICATION - GENERAL INFORMATION
Lubrication is an essential part of preventive maintenance, affecting to
a great extent the useful life of the compressor. Different lubricants are
needed and some components require more frequent lubrication than
others. Therefore, it is important that the instructions regarding types
of lubricants and the frequency of their application be explicitly
followed. Periodic lubrication of the moving parts reduces to a
minimum the possibility of mechanical failures.
The Maintenance Schedule shows those items requiring regular
service and the interval in which they should be performed. A regular
service program should be developed to include all items and fluids.
These intervals are based on average operating conditions. In the
event of extremely severe (hot, cold, dusty or wet) operating
conditions, more frequent lubrication than specified may be necessary.
All filters and filter elements for air and compressor oil must be
obtained through Portable Power to assure the proper size and
filtration for the compressor.
Compressor Oil Change
These compressors are normally furnished with an initial supply of oil
sufficient to allow operation until the first service interval indicated in
the Maintenance Schedule. If a compressor has been completely
drained of all oil, it must be refilled with new oil before it is placed in
operation. Refer to specifications in the Portable Compressor Fluid
Chart.
If the compressor has been operated for the time/hours indicated in the
Maintenance Schedule, it should be completely drained of oil. If the
compressor has been operated under adverse conditions, or after long
periods in storage, an earlier change may be necessary as oil
deteriorates with time as well as by operating conditions.
An oil change is good insurance against the accumulation of dirt,
sludge, or oxidised oil products.
Completely drain the separator tank, piping, and cooler. If the oil is
drained immediately after the compressor has been run for some time,
most of the sediment will be in suspension and, therefore, will drain
more readily. However, the oil will be hot and care must be taken to
avoid contact with the skin or eyes.
After the compressor has been completely drained of all old oil, close
the drain valves and/or plugs and install new oil filter elements. Add oil
in the specified quantity at the filler plug. Tighten the filler plug and run
the compressor to circulate the oil. Check the oil level. DO NOT
OVERFILL.
NOTE:
Some oil types are incompatible when mixed and result in the
formation of varnishes, shellacs, or lacquers which may be insoluble.
Such deposits can cause serious troubles including clogging of the
filters.
Where possible, do NOT mix oils of different types and avoid mixing
different brands. A type or brand change is best made at the time of
a complete oil drain and refill.
CAUTION:
In most severe applications such as sandblasting, quarry
drilling, well drilling, and oil and gas drilling, more frequent service in-
tervals will be required to ensure long component life.
WARNING: High pressure air can cause severe injury or death
from hot oil and flying parts. Always relieve pressure before
removing caps, plugs, covers or other parts from pressurised
air system. Ensure that the air pressure gauge reads zero (0)
pressure and ensure there is no air discharge when opening the
manual blowdown valve.
NOTE:
Portable Power provides compressor oil specifically
formulated for Portable Compressors and requires the use of these
fluids in order to obtain extended limited airend warranty.
Summary of Contents for 10/104
Page 2: ......
Page 4: ......
Page 11: ...ISO SYMBOLS 7 7 124 10 104 10 124 14 114 14 84 Replace any cracked protective shield ...
Page 83: ...MAINTENANCE 79 7 124 10 104 10 124 14 114 14 84 ...
Page 84: ...80 MAINTENANCE 7 124 10 104 10 124 14 114 14 84 ...
Page 92: ...88 MACHINE SYSTEMS 7 124 10 104 10 124 14 114 14 84 ...
Page 108: ......
Page 109: ......