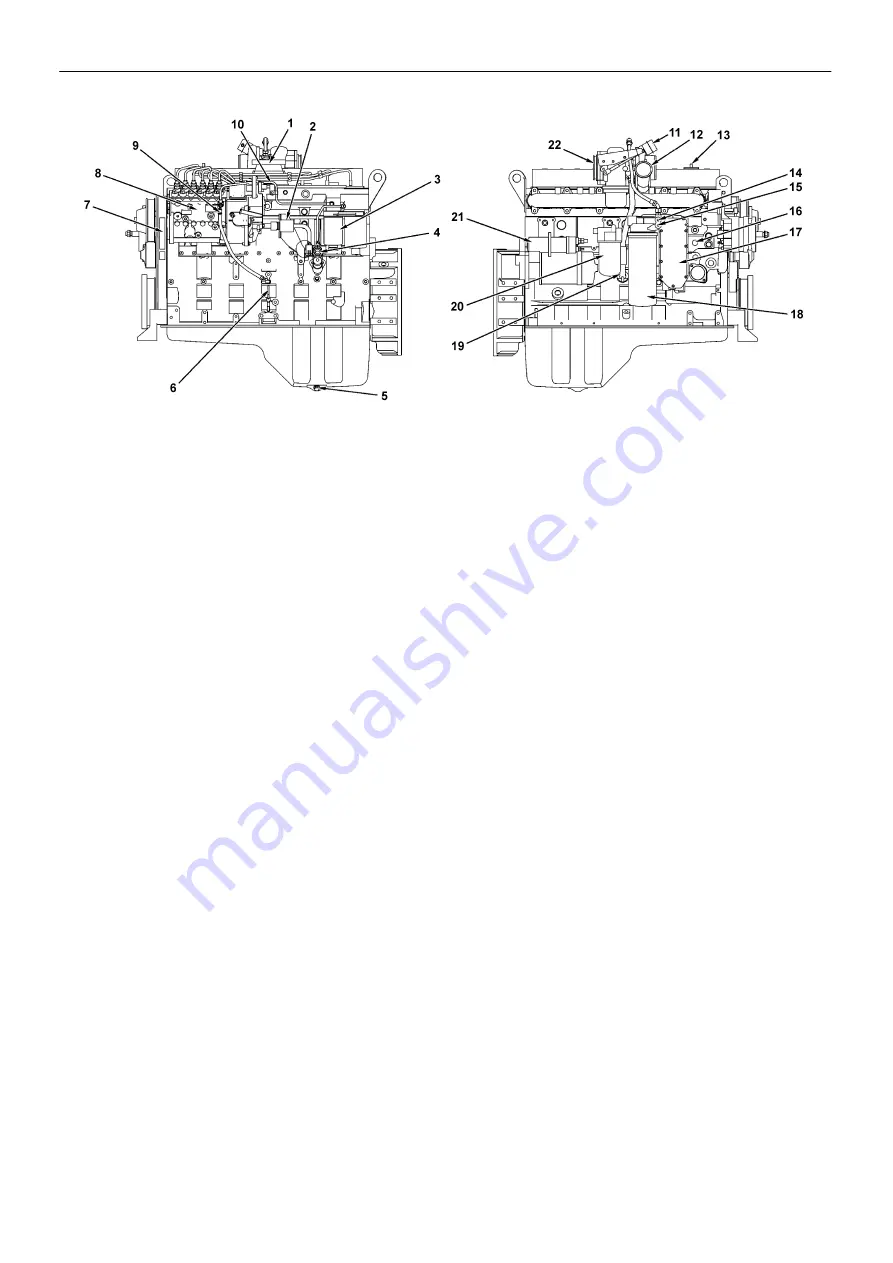
22
EXTERNAL VIEWS
9/235
Fig. 1 (Left
−
hand Side)
Fig. 2 (Right
−
hand Side)
(1) Engine air inlet.
(2) Shutoff solenoid.
(3) Fuel filter
(4) Fuel transfer pump.
(5) Oil drain plug.
(6) Dipstick (engine oil)
(7) Engine dataplate.
(8) Fuel injection pump
(9) Fuel drain line.
(10) Intake manifold.
(11) Turbocharger wastegate actuator.
(12) Turbocharger air outlet.
(13) Oil filler cap.
(14) Lubricating oil pressure (after filter).
(15) Lubricating oil pressure (before filter).
(16) Coolant heater port.
(17) Lubricating oil cooler.
(18) Lubricating oil filter.
(19) Turbocharger oil drain.
(20) Coolant filter.
(21) Starter motor
(22) Turbocharger exhaust outlet.