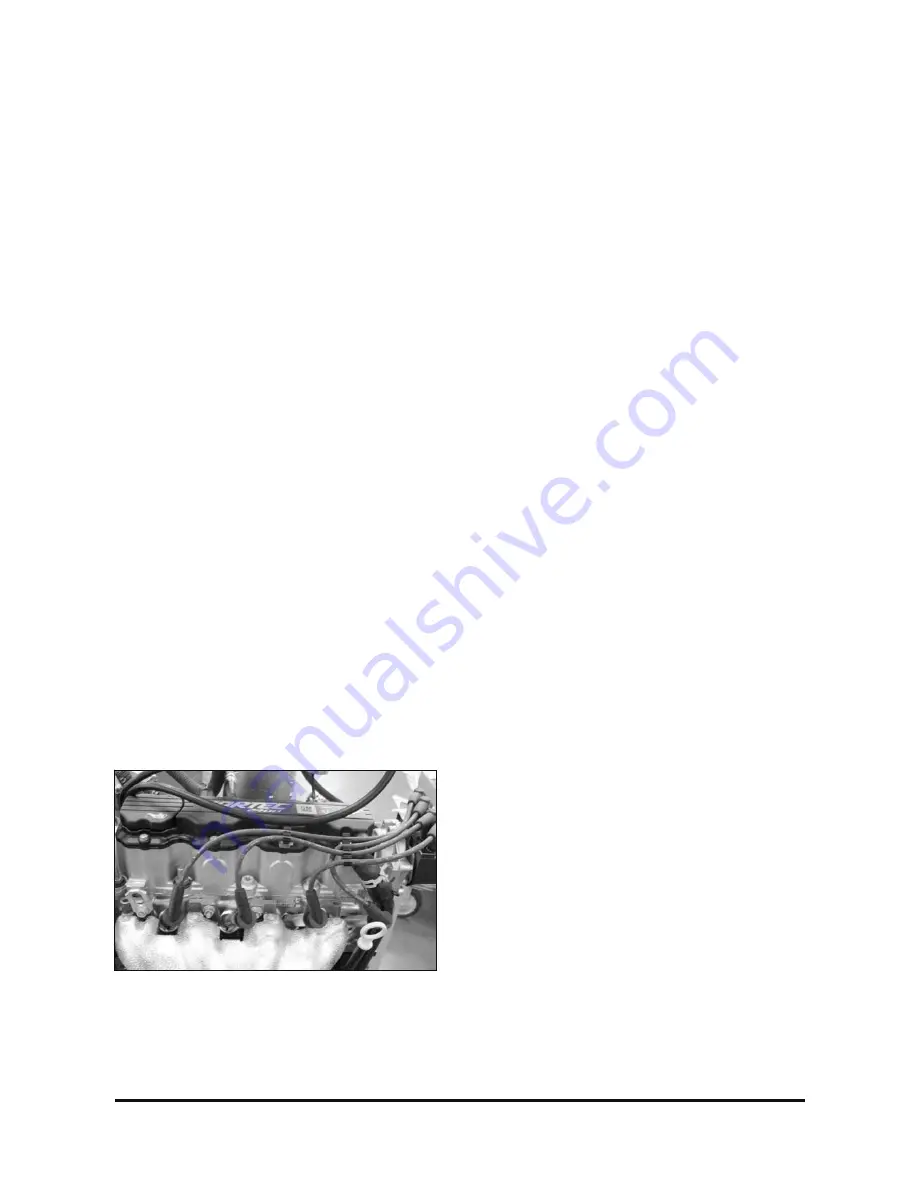
G424F(FE) Service Manual
Chapter 4. Engine Electrical System
104
Spark Plug Wire Inspection
Sparking plug wire integrity is vital for proper engine
operation. A Thorough inspection will be necessary
to accurately identify conditions that may affect
engine operation. Inspect for the following condition:
1.
Correct routing of the spark plug wires. Incorrect
routing may cause cross-firing
2.
Any signs of cracks or splits in the wires
3.
Inspect each boot for the following conditions:
•
Tearing
•
Piercing
•
Arcing
•
Carbon tracking
•
Corroded terminal
If corrosion, carbon tracking, or arcing is indicated
on a spark plug boot or on a terminal, replace the
wire and the component connected to the wire.
Spark Plug Wire Replacement
Removal
Remove or disconnect
1.
Disconnect the spark plug wire at each spark plug.
See Figure 81
a.
Twist the boots 1/2 turn before removing the
boots
b.
Pull only on the boot or use a tool designed for
this purpose in order to remove the wire from
each spark plug.
2.
Disconnect the spark plug wire from the coil pack.
a.
Twist each spark plug boot 1/2 turn.
b.
Pull only on the boot or use a tool designed for
this purpose in order to remove the wires from
the coil pack.
Installation
Install or connect
Note: If the boot-to-wire movement has occurred,
the boot will give a false visual impression of being
fully seated. Ensure that the boots have been
properly assembled by pushing sideway on the
installed boots. Failure to properly seat the terminal
onto the spark plug will lead to wire core erosion an
result in an engine misfire or crossfire condition and
possible internal damage to the engine.
1.
Install the spark plug wires at the coil pack. You
should feel the terminal snap onto the coil.
2.
Install the spark plug wire to each spark plug. You
should feel the terminal snap onto the spark plug.
See Figure 81.
3.
Inspect the wires for proper installation:
a.
Push sideways on each boot in order to inspect
the seating.
b.
Reinstall any loose boot. You should feel the
terminal snap onto the spark plug or coil when
installing the spark plug wire. Inspect and
replace component that is damaged
c.
Wire routing must be kept intact during service
and followed exactly when wires have been
disconnected or when replacement of the wires
is necessary. Failure to route the wires
properly can lead to radio ignition noise and
cross firing of the plugs or shorting of the leads
to the ground.
d.
Any time the spark plug wires or boots are
installed on the spark plug, new dielectric
grease needs to be applied inside the boot.
Summary of Contents for D20G
Page 2: ......
Page 5: ...Specifications TORQUE SPECIFICATIONS SB2004E00 D e c 1 9 9 8 ...
Page 14: ......
Page 16: ......
Page 138: ...Diesel Engine Engine System 124 NOTE The crankshaft must rotate freely by hand 02900058 ...
Page 254: ......
Page 256: ......
Page 260: ......
Page 341: ...4TNV98 4TNE98 Diesel Engine Section 3 Engine 87 4TNE98 Engine Figure 6 1 ...
Page 423: ...4TNV98 4TNE98 Diesel Engine Section 4 Fuel System 169 Fuel System Components Figure 7 1 ...
Page 477: ...4TNV98 4TNE98 Diesel Engine Section 7 Starter Motor 223 Starter Motor Troubleshooting ...
Page 494: ...4TNV98 4TNE98 Diesel Engine Section 8 Troubleshooting 240 Troubleshooting Charts ...
Page 495: ...4TNV98 4TNE98 Diesel Engine Section 8 Troubleshooting 241 ...
Page 496: ...4TNV98 4TNE98 Diesel Engine Section 8 Troubleshooting 242 ...
Page 498: ...4TNV98 4TNE98 Diesel Engine Section 8 Troubleshooting 244 4TNE98 Engine ...
Page 499: ...Service Manual G424FE LP Engine G424F LP Gasoline Engine G20G G25G G30G SB4320E00 Jan 2008 ...
Page 500: ......
Page 502: ......
Page 529: ...G424F FE Service Manual Chapter 2 Recommended Maintenance 29 ...
Page 534: ...G424F FE Service Manual Chapter 3 Engine Mechanical System 34 MAIN BEARINGS 0 50 UNDERSIZE ...
Page 584: ...G424F FE Service Manual Chapter 3 Engine Mechanical System 84 ...
Page 729: ...G424F FE Service Manual 229 Chapter 8 Basic Troubleshooting ...
Page 731: ...G424F FE Service Manual 231 Chapter 8 Basic Troubleshooting ...
Page 806: ......
Page 808: ......
Page 810: ......
Page 820: ...Power Train System Operation 14 Hydraulic System ...
Page 822: ...Power Train System Operation 16 Hydraulic System ...
Page 824: ...Power Train System Operation 18 Hydraulic System ...
Page 826: ...Power Train System Operation 20 Hydraulic System ...
Page 856: ......
Page 858: ......
Page 860: ......
Page 930: ......
Page 932: ......
Page 934: ......
Page 936: ......
Page 1018: ......
Page 1023: ...A374081 01 ELECTRIC SCHEMATIC MODEL D20 25 30G EM0K2 EM0K3 Cummins B3 3 ...
Page 1024: ...A654030 00 ELECTRIC SCHEMATIC MODEL D20 25 30G EM0QM EM0QN Yanmar 4TNE98 Tier 3 ...
Page 1025: ...A604500 00 ELECTRIC SCHEMATIC MODEL G20 25 30G EM0QF EM0QG GM G424F Non Certi LP ...
Page 1026: ...A604510 00 ELECTRIC SCHEMATIC MODEL G20 25 30G EM0QH EM0QJ GM G424F Non Certi GAS ...
Page 1027: ...A604516 00 ELECTRIC SCHEMATIC MODEL G20 25 30G EM0QY EM0QZ GM G424FE Tier 3 LP ...
Page 1028: ......
Page 1030: ......
Page 1059: ...Safety Section 29 Lean away from the direction of fall Lean forward ...
Page 1071: ...General Section 41 Typical Example Side Shifter Serial Number If Equipped ...