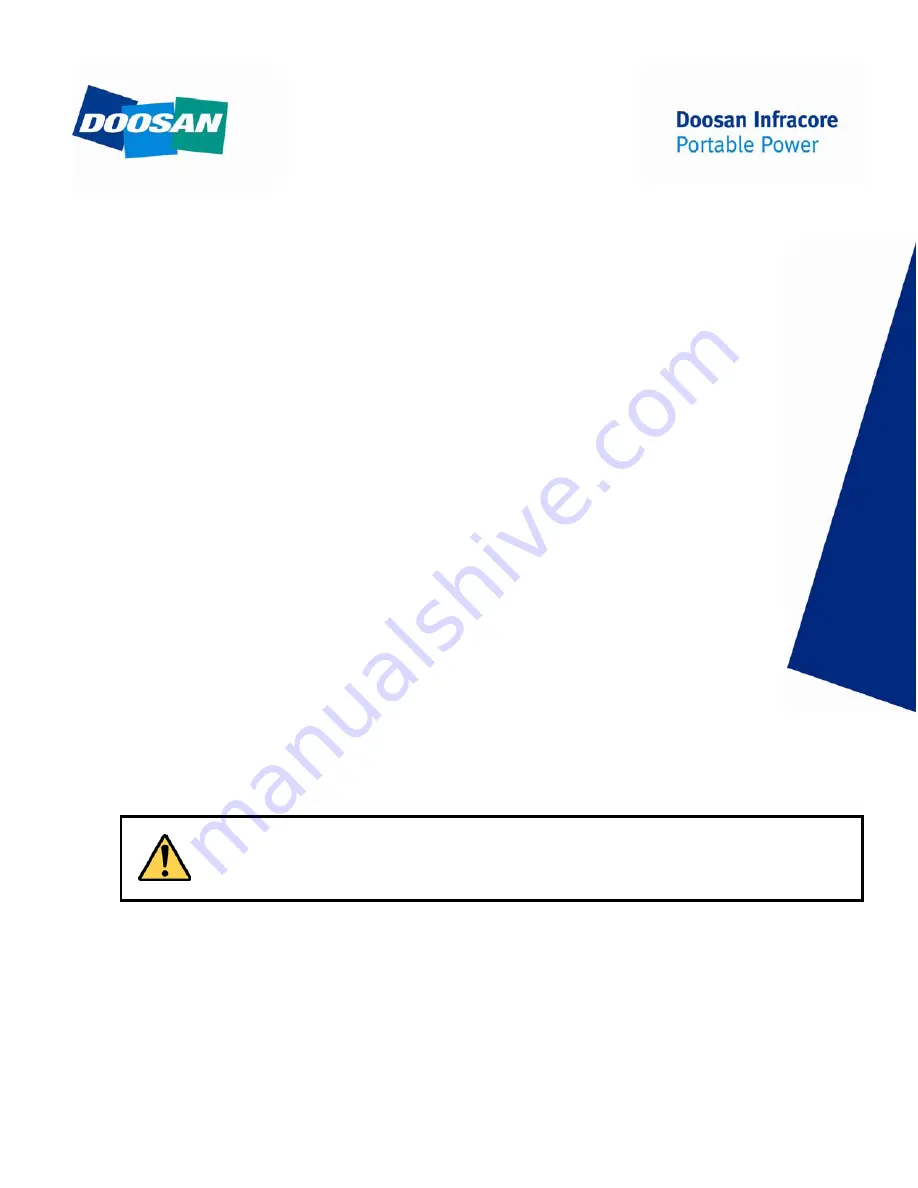
COMPRESSOR MODEL
P260/HP220WYM-T3 (D82)
P260/HP220WYM-FX-T3 (E55)
P260/HP220WYM-EX-T3 (E56)
Doosan Infracore Portable Power
1293 Glenway Drive
Statesville, N.C. 28625
DoosanPortablePower.com
P/N: 46553446 (9-2013) Rev C
This manual contains important safety information.
Do not destroy this manual.
This manual must be available to the personnel who operate and maintain this compressor.
OPERATION and MAINTENANCE
MANUAL
Summary of Contents for D82
Page 2: ...2...
Page 5: ...3 FOREWORD...
Page 8: ...Operation Maintenance Manual FOREWORD 6...
Page 9: ...7 DRAWBAR NOTICE...
Page 11: ...DRAWBAR NOTICE Operating Maintenance Manual 9...
Page 12: ...Operating Maintenance Manual DRAWBAR NOTICE 10...
Page 13: ...11 SAFETY...
Page 16: ...Operating Maintenance Manual SAFETY 14...
Page 18: ...Operating Maintenance Manual SAFETY 16...
Page 19: ...SAFETY Operating Maintenance Manual 17...
Page 21: ...SAFETY Operating Maintenance Manual 19...
Page 23: ...21 NOISE EMISSION...
Page 29: ...27 GENERAL DATA...
Page 32: ...Operating Maintenance Manual GENERAL DATA 30...
Page 33: ...31 OPERATION...
Page 43: ...41 LUBRICATION...
Page 45: ...43 MAINTENANCE...
Page 55: ...53 TROUBLESHOOTING...