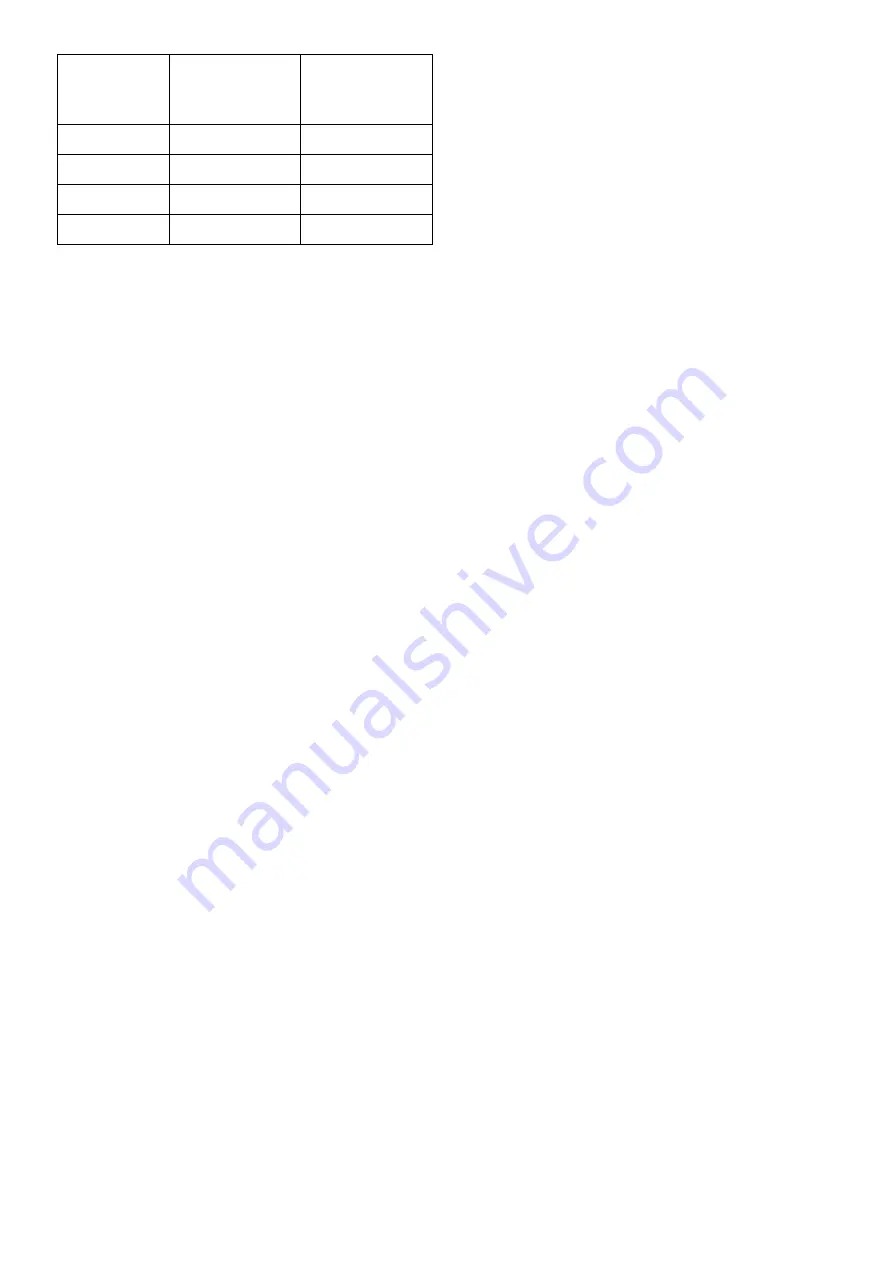
G80XW/XF, G115XW/XF, G150XW/XF, G200XW/XF - 50HZ
OPERATION & MAINTENANCE MANUAL
85
G100XW/XF, G135 XW/XF, G170XW/XF, G225XW/XF - 60Hz
REMOVAL OF NOZZLE
1. Assemble the cap nut and nozzle to the nozzle tester.
2. Remove the nozzle nut and components inside.
INSTALLATION NOZZLE
1. After removing carbon deposit, submerge the nozzle
in diesel oil and clean it.
2. Replace all the gaskets with new ones.
3. Assemble the parts and tighten them to specified
torque.
ADJUSTMENT NOZZLE
1. The cap nut and assemble a nozzle to a nozzle tester.
2. With the adjusting screw loosened, operate the
nozzle 2 ~ 3 times to bleed it.
3. Operate the nozzle tester lever at the specified rate.
4. Adjust the injection pressure to the standard pressure
using the adjusting screw.
5. After adjusting the injection pressure, tighten the cap
nut to the specified torque.
6. Re-check the injection pressure and ensure the spray
pattern is normal. the spray pattern should be uniform
and free of spattering.
NOTE FOR CLEANING NOZZLE
•
Clean nozzle body externally of soot and carbon.
When cleaning several nozzles at the same time,
make sure nozzle bodies and needles are not mixed
up. Visually inspect needle and body.
•
Do not clean the nozzle if the seat of the needle is
indented or the pintle is damaged. If this occurs the
nozzle should be replaced.
•
Clean annular groove with scraper over full
circumference. Wash out dislodged carbon deposits
and dirt.
•
Scrape needle seat with cleaning cutter. Dip cutter in
test oil before use. The cutter can also be clamped in
a lathe.
•
Polish needle seat with wooden cleaning tool by
chucking the needle in a lathe at the pintle end.
•
Clean the spray holes of nozzles by chucking a
cleaning needle of suitable diameter in the collet. If
the carbon deposits in the spray holes cannot be
removed by rotating and pressing, have the needle
project only slightly from the collet and drive out the
carbon by lightly tapping on the tool.
•
Before reassembly thoroughly wash nozzle body and
needle in clean test oil.
•
Hold the needle at the pintle end only; to avoid
corrosion do not touch the lapped surfaces of the
needle with your fingers.
•
Thoroughly clean all other parts of the nozzle holder
with clean fuel.
•
Check nozzle discharge pressure in the nozzle tester.
The edge-type filter should not be pressed into the
nozzle holder by more than approximately 5mm. If
this depth is exceeded the injector must be replaced.
ADJUSTING INJECTION TIMING
1. Bring the piston of #1 cylinder to the compression
TDC (OT) by turning the crankshaft. Again, turn 60° in
the reverse direction of engine rotation.
2. Disassemble the fuel injection pipe that connects the
fuel injection pump and #1 injection nozzle.
3. Disassemble the fuel injection pump delivery valve
holder. After removing the valve and valve spring,
assemble the valve holder. Finally, assemble the "U"
shaped pipe.
4. Operating the priming pump of supply pump, turn the
crankshaft slowly in the direction of engine rotation
until the fuel drops at the rate of one drop every 6 ~8
sec.
Engine Model
Opening
pressure
(kg/cm
2
)
Remarks
D1146
214
at 200 rpm
D1146T
214
at 200 rpm
DP086TA
214
at 200 rpm
P086TI
214
at 200 rpm