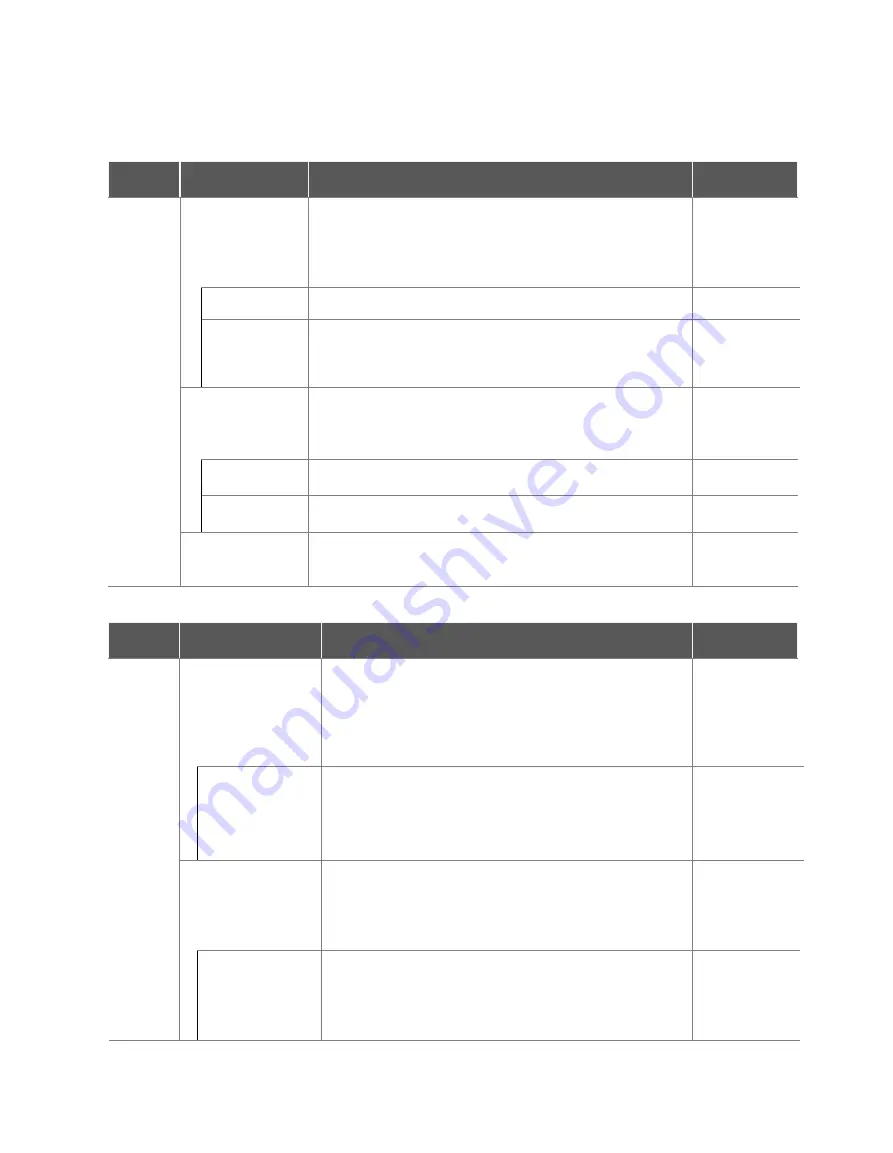
89
5.4
State and Flange LED Color for Each Mode
Mode
State
Description
Flange and/or
Base LED
Manual
Manual Standby
This is the default status of teaching.
Workcell Manager
,
Task Builder
and
Task Writer
can be
used to configure the work condition or perform task
programming.
It monitors the stop status with Safe Operating Stop (SOS).
Blue
Manual
Jogging
The jog function is used to operate the robot.
Blue Blinking
Manual
Handguiding
The robot can be operated directly by hand during teaching.
Cyan Blinking
Recovery Standby
Recovery in progress.
All safety monitoring functions except for axis and TCP speed
monitoring are disabled during recovery.
It monitors the stop status with Safe Operating Stop (SOS).
Yellow
Blinking
Recovery
Jogging
The jogs of each axis can be used to correct the exceeded
safety threshold.
Yellow
Blinking
Recovery
Handguiding
The robot can be moved directly by hand to correct the
exceeded safety threshold.
Yellow
Blinking
Safety Stop
The system stopped due to protective stop or exceeding the
safety threshold.
It monitors the stop status with Safe Operating Stop (SOS).
Yellow
Mode
State
Description
Flange and/or
Base LED
Auto
Auto Standby
The Teach Pendant UI is in the actual mode execution
screen in a single workspace.
Pressing the "Execute" button will execute the task
program.
White is displayed for a
Standalone Zone,
green is
displayed for a
Collaborative Zone.
.
White/Green
Auto
Running
The task program is being executed.
White is displayed for a
Standalone Zone
, green is
displayed for a
Collaborative Zone
., and white and yellow
are displayed by turns for a
High Priority Zone
White
Blinking
/
Green Blinking
/
White and
Yellow Flashing
alternately
HGC
(HandGuide
Control)
Standby
The Handguiding command is executed during task
program execution.
The system waits until the user presses the "Handguiding"
button.
It monitors the stop status with Safe Operating Stop (SOS).
Cyan
HGC Running
The robot pose can be changed by pressing the
"Handguiding" button.
After the robot stops, enter
HGC End & Resume
signal
through the Safety IO to set Auto Running and then
continue executing the task program.
Cyan
Blinking
Summary of Contents for H2017
Page 1: ...1 Manual Version 2 1 Software Version 2 7 1 ...
Page 29: ...29 2 5 3 Robot operating space M0609 ...
Page 30: ...Doosan Robotics Installation Manual v2 1 30 ...
Page 31: ...31 M0617 ...
Page 32: ...Doosan Robotics Installation Manual v2 1 32 ...
Page 33: ...33 M1013 ...
Page 34: ...Doosan Robotics Installation Manual v2 1 34 ...
Page 35: ...35 M1509 ...
Page 36: ...Doosan Robotics Installation Manual v2 1 36 ...
Page 37: ...37 H2017 ...
Page 38: ...Doosan Robotics Installation Manual v2 1 38 ...
Page 39: ...39 H2515 ...
Page 40: ...Doosan Robotics Installation Manual v2 1 40 ...
Page 42: ...Doosan Robotics Installation Manual v2 1 42 M1013 M1509 ...
Page 119: ...119 B 2 Europe Machinery Directive Attestation of Conformity ...
Page 120: ...Doosan Robotics Installation Manual v2 1 120 ...
Page 121: ...121 B 3 Europe EMC Directive Attestation of Conformity ...
Page 122: ...Doosan Robotics Installation Manual v2 1 122 B 4 U S NRTL Certification U S CANADA ...
Page 123: ...123 ...
Page 124: ...Doosan Robotics Installation Manual v2 1 124 B 5 Functional Safety Certification ...
Page 125: ...125 B 6 Voluntary Safety Confirmation Declaration KCs ...
Page 126: ...Doosan Robotics Installation Manual v2 1 126 ...
Page 127: ...127 ...
Page 128: ...Doosan Robotics Installation Manual v2 1 128 ...
Page 129: ...129 ...
Page 130: ...Doosan Robotics Installation Manual v2 1 130 ...
Page 161: ...161 D 1 3 Nameplate and Label ...
Page 176: ...Doosan Robotics Installation Manual v2 1 176 E 1 3 Nameplate and Label ...
Page 190: ...Doosan Robotics Installation Manual v2 1 190 ...