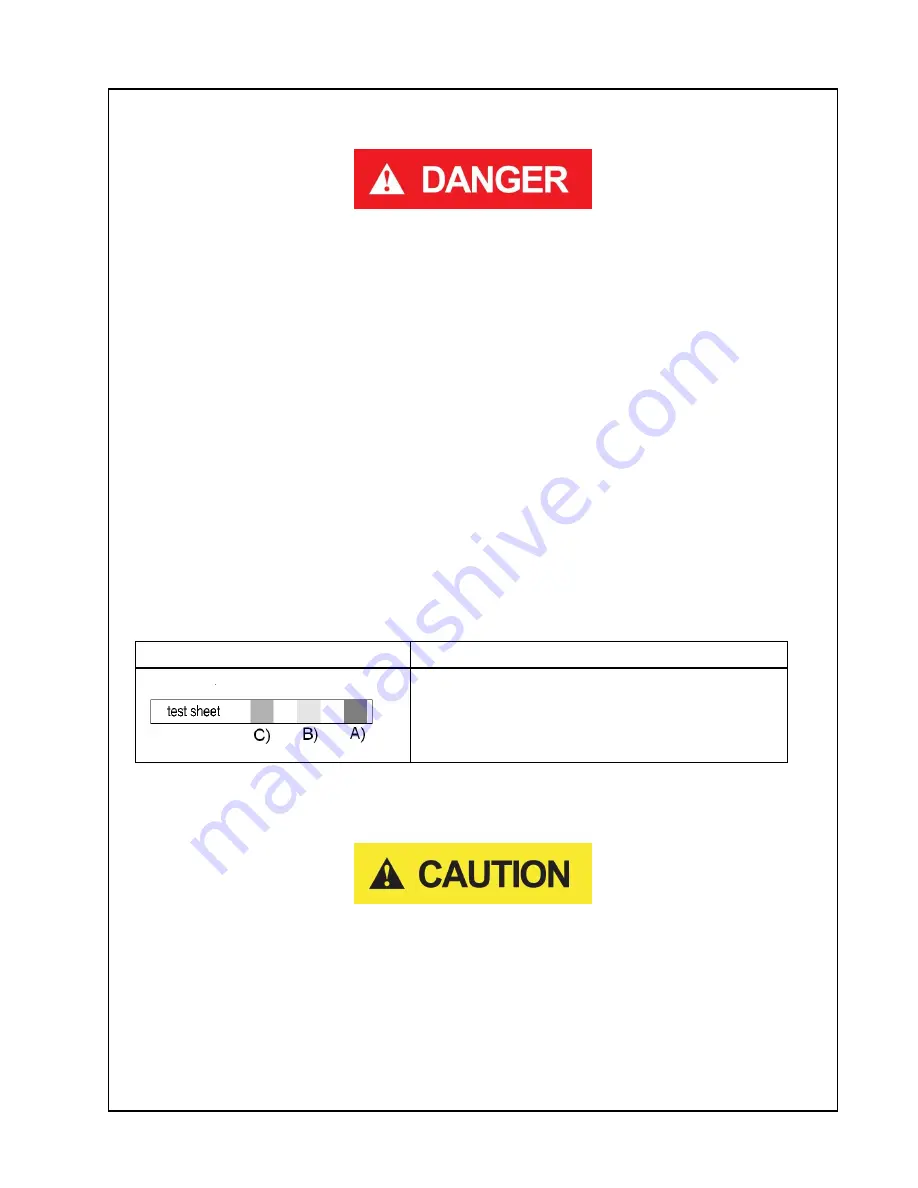
Operation & Maintenance Manual
Checking the Coolant
If the reservoir cap is opened to exchange or replenish coolant while the
engine is overheated, hot water will spurt out and may cause serious
burns. If it is absolutely necessary to open the reservoir cap while the
engine is overheated, wrap the reservoir cap with a cloth and slowly
open the reservoir cap in two steps until the steam pressure has been
released from the inside. After the steam pressure has been completely
released, remove the reservoir cap.
1. Make sure that the engine and radiator are cooled.
2. Check the level in the supplementary tank.
3. If the coolant level indicates between the upper limit and the lower limit on the
supplementary tank, it means that the coolant volume is normal.
4. If there is insufficient coolant, replenish it.
5. Open the reservoir cap and check the condition of the coolant. If the coolant cap
is contaminated or insufficient, measure the coolant concentration. If the coolant
concentration is outside the specified range, exchange the coolant.
Measurement of Coolant Concentration
Special Tools
Figure
Product Number/Name
60.99901-0038 CC2602M (Fleet guard number)
Coolant test sheet
The Coolant concentration can be measured as follows:
1. If the Engine coolant temperature is within a range of 10 ~ 55° C, drain the Coolant.
When taking out a sample of coolant from the supplementary tank, it is
difficult to measure the precise concentration. Always take out sample
by opening the drain plug of coolant.
2. Soak the test sheet in the coolant and remove after 3 ~ 5 seconds. Shake the sheet
to remove the remaining coolant.
3. Wait for about 45 seconds until the test sheet changes its color.
77
Summary of Contents for Infracore HP210WDO-T4F
Page 2: ......
Page 3: ...iii...
Page 4: ......
Page 8: ...8...
Page 9: ...Foreword 9...
Page 12: ...12...
Page 13: ...Drawbar Instructions 13...
Page 16: ...16...
Page 17: ...Safety 17...
Page 25: ...Safety Operation Maintenance Manual 25...
Page 26: ...26...
Page 27: ...Noise Emission 27...
Page 32: ...32...
Page 33: ...General Data 33...
Page 36: ...36...
Page 37: ...Operating Instructions 37...
Page 55: ...Engine Operation 55...
Page 86: ...86...
Page 87: ...Lubrication 87...
Page 90: ...90...
Page 91: ...Maintenance 91...
Page 99: ...99...
Page 101: ...Maintenance Operation Maintenance Manual Preventive Maintenance Schedule Back 101...
Page 102: ...102...
Page 103: ...Troubleshooting 103...
Page 114: ...114...
Page 115: ...Appendix A 115...
Page 116: ...Operation Maintenance Manual Appendix A Warranty 116...
Page 117: ...Appendix A Operation Maintenance Manual 117...
Page 118: ...Operation Maintenance Manual Appendix A 118...
Page 120: ......
Page 121: ......