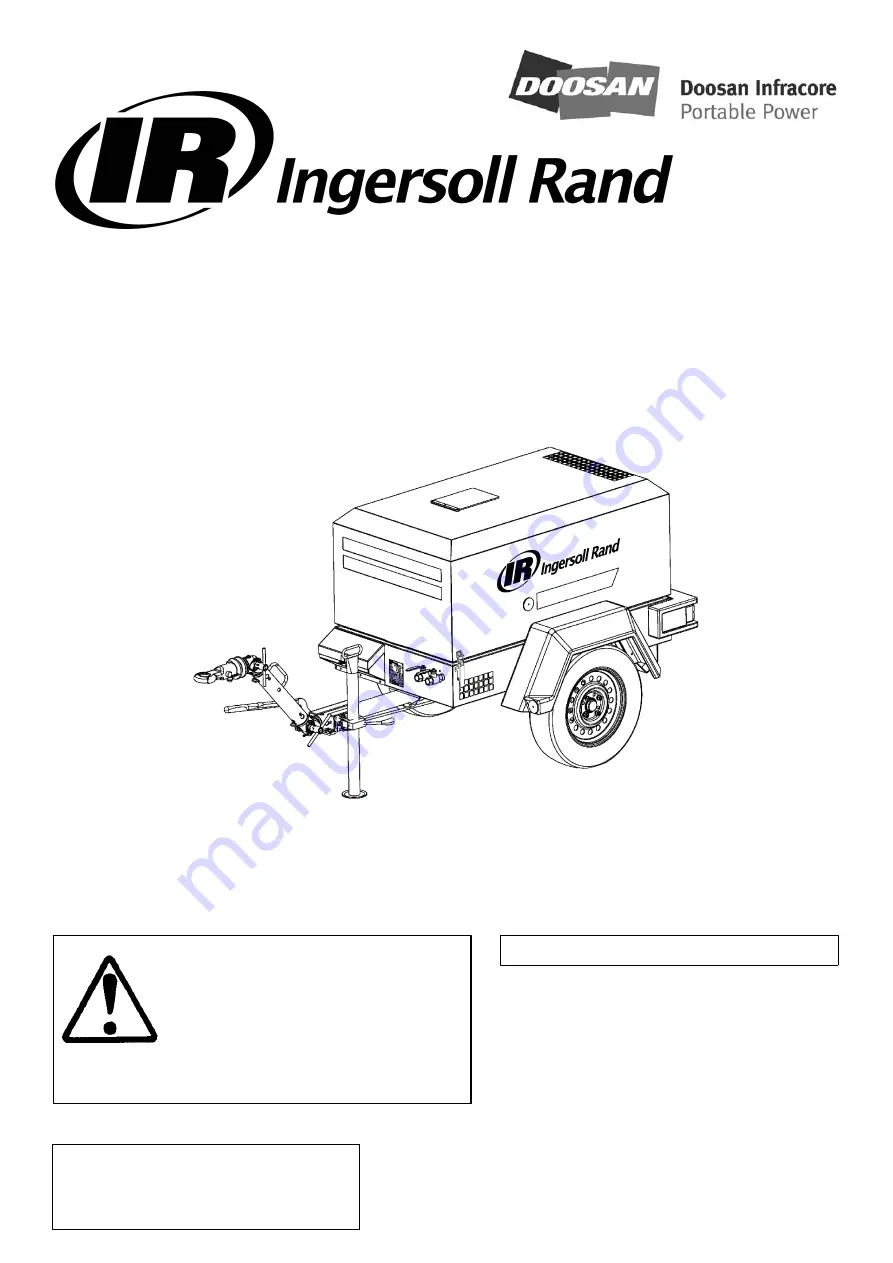
7/20
P65
OPERATION AND MAINTENANCE MANUAL
Original Instruction
C.C.N. : 22311203
en
REV
: H
DATE
: JANUARY 2010
This manual contains
important safety information
and must be made available to
personnel who operate and
maintain this machine.
121001
−
>
SERIAL No :
Revised (
10
-12)
Doosan purchased Bobcat Company from Ingersoll-Rand Company in
2007. Any reference to Ingersoll-Rand Company or use of trademarks,
service marks, logos, or other proprietary identifying marks belonging
to Ingersoll-Rand Company in this manual is historical or nominative
in nature, and is not meant to suggest a current affiliation between
Ingersoll-Rand Company and
Doosan
Company
or the
products
of
either.