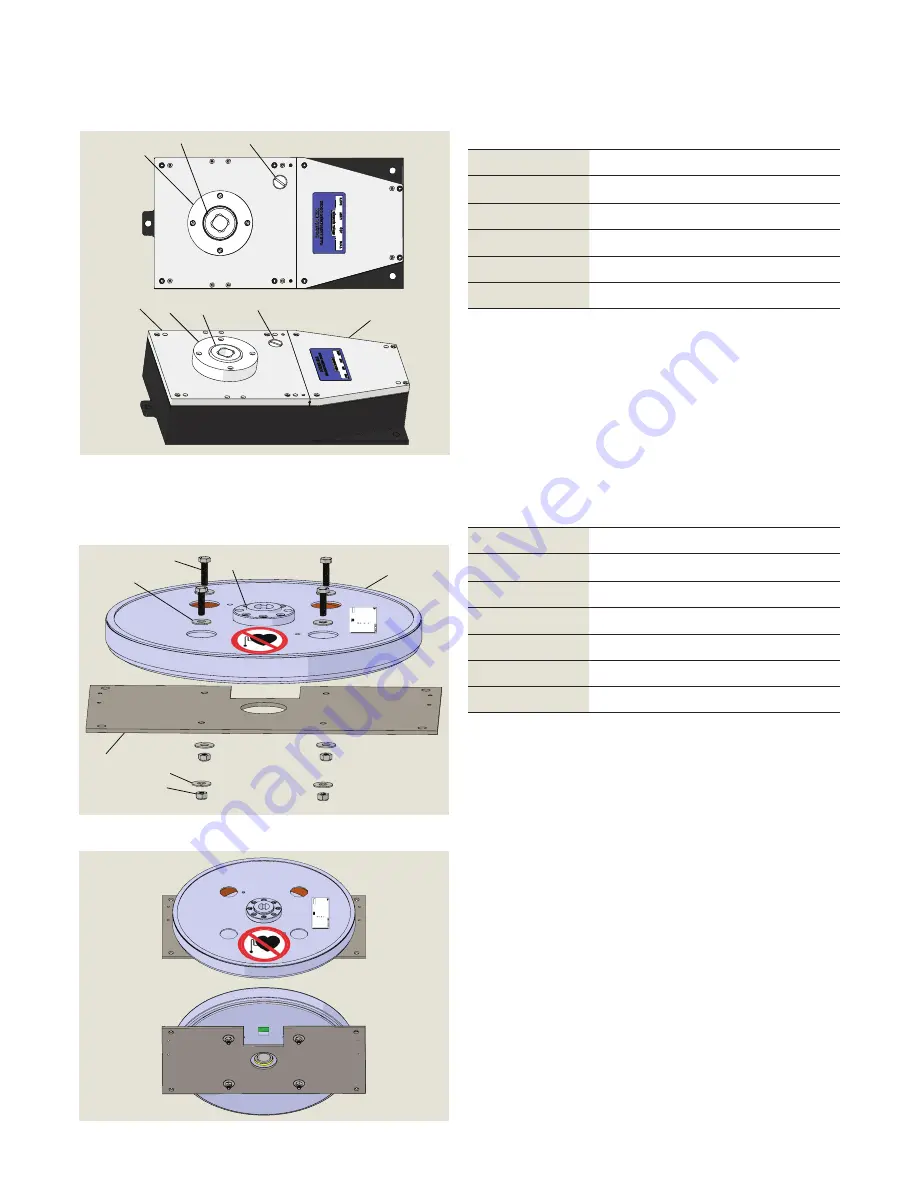
22
Crane 4000LE
07-2022
RL6002-001
Crane 4000LE Installation Manual
In-ground Motion Assist 360 drive and speed control
Remote control enclosure
Chapter 5
5.16 Motion Assist 360 drive bracket assembly
Fig. 5.16.1 Drive bracket assembly exploded view
Fig. 5.16.2 Drive bracket assembly
5.16.1 Drive bracket assembly RS6037.
1
Control unit DX60
Germany
p/n
34052292150
2
5/16" x 1/2" SS SH
DF6018-01G
3
5/16"
SS
flat
was
DF6019-01G
4
Power supply/cont
unit mounting bra
DC6023
5
5/15" SS external
tooth lock washer
DF6016-01G
6
Ground lug assem
DX6009
4
6
7
6
4
7
8
8.1
Fig. 5.15.1 In-ground speed control assembly RS6074-010
5.15 In-ground speed control assembly
2
3
5
7
8
6
7
Art.Nr
.: 34050001
150
100 - 240V ~ 50/60 Hz
-40 - +60°C
53
5
4
0
DIN 18650
Made in Germany
DORMA
Deutschland GmbH
Dorma Platz 1
58256 Ennepetal
Germany
IP20
month year
System:
Speed Limiter:
Positionin
gA
utomatic:
Static force:
Servomatic: Static force
:
Automatic: Static force:
58 W
8 W
150 N
67 N
58 W
67 N
1/2/3
0
102 W
KT
FLEX
Dir
ect driv
e sy
stem
Art.Nr
.: 34050001
150
100 - 240V ~ 50/60 Hz
-40 - +60°C
5
3
5
4
0
DIN 18650
Made in Germany
DORMA
D
eutschland GmbH
Dorma Platz 1
58256 Ennepetal
Germany
IP20
month year
System:
Speed Limiter:
Positioning
A
utomatic:
Static force:
Servomatic: Static force:
Automatic: Static force:
58 W
8 W
150 N
67 N
58 W
67 N
1/2/3
0
102 W
KT
FLEX
Dir
ec
t driv
e sy
st
em
Table 5.16.1
Motion Assist 360 drive bracket assembly
Part / Assembly
Description
2
RC6060
Motion Assist 360 drive mounting bracket
3
RC6025
Drive flange
5
RF6004-01Z
M10 x 40 mm SHCS, class 12.9
6
RF6005-01G
M10-1.5 18-8 SS nylon locknut
7
RF6010-01G
1/2" flat washer
8
RX6010
Motion Assist 360 drive
Table 5.15.1
In-ground speed control assembly
RS6074-010
Part / Assembly
Description
4
Drive shaft
6
Collar
7
1/2 x 3/4" long SFHMS
8
1/2" Thick subplate
8.1
1/2" thick subplate