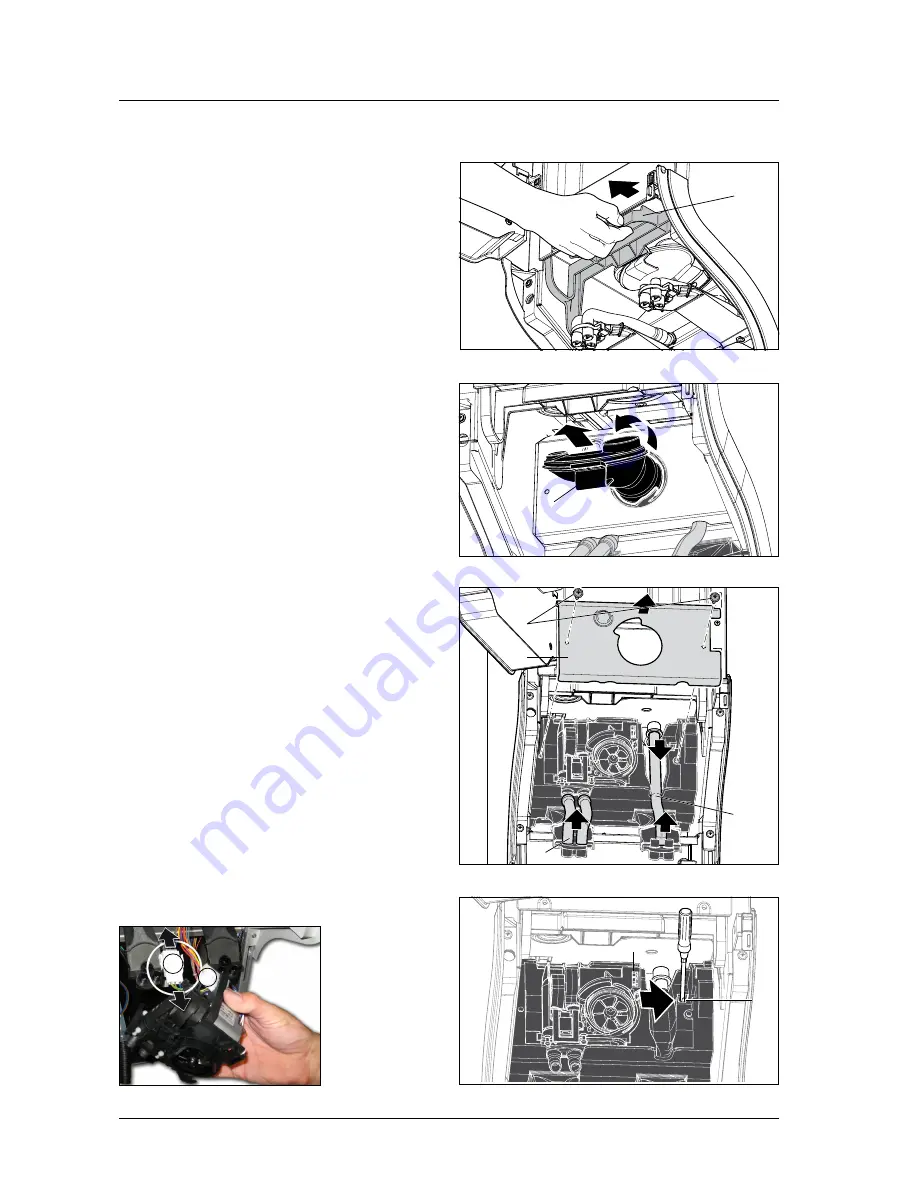
Cafitesse 100 Next Generation
Functions - dosing system
5C-6
August 2009
Disconnect the dispenser from the power supply
system and close the water tap.
Remove the cuptray and the driptray and open
pen
the dispenser door.
Remove the product pack from the cooling com-
partment and store it in the refrigerator.
Pull down the cover fluid treatment (see chapter
A.2.2).
Note:
The cafitesse NG 120 is not
equipped with a cover coolbox.
Undo 2 releasable rivets at the splash panel and
remove the overflow hose on the inside of the
splash panel (see chapter A.2.2)..
Remove the splash panel together with the cover
fluid treatment (see chapter �.2.2).
(see chapter A.2.2).
see chapter A.2.2).)..
Pull the locking device (1) to release the comple-
te mixing console (fig. 1).
Rotate the mixing bowl (2) counterclockwise to
release it and remove it with the sealing ring
(fig. 2).
Undo the 2 screws (3) at the mixing cover con-
sole (4) and remove the cover console. (fig. 3).
Remove the outlet hose (5) on the right side and
the 2 outlet hoses (6) on the left side (fig. 3)
Press the switch (7) on the right side to unhook
the mixing unit and take it out (fig. 4).
Use a screwdriver to unhook the mixing console
at the snap-fits (8) on both sides and pull the
mixing console out of the guide rails (fig. 4).
Undo the cable harness from the from the con-
nector (9) and the cable harness from the micro
switch (10) (fig. 5).
•
•
•
•
•
•
•
•
•
•
•
•
•
3
4
C.2.3 Disassembly of the mixing unit
(only for Cafitesse 120 NG)
Fig. 1
Fig. 2
Fig. 3
1
2
6
5
Fig. 4
7
Fig. 5
9
8
9
10
Summary of Contents for Cafitesse 110
Page 2: ... 2009 Douwe Egberts Coffee Systems International DRAFT Version August 2009 D R A F T ...
Page 22: ...D R A F T Cafitesse 100 Next Generation Installation Putting into operation 2 20 August 2009 ...
Page 54: ...Cafitesse 100 Next Generation Programming 4 20 August 2009 ...
Page 58: ...D R A F T Cafitesse 100 Next Generation Functions Overview of assemblies 5 August 2009 ...
Page 71: ...Cafitesse 100 Next Generation Functions water system August 2009 5A 13 ...
Page 82: ...Cafitesse 100 Next Generation Functions dosing system 5C 10 August 2009 ...
Page 93: ......