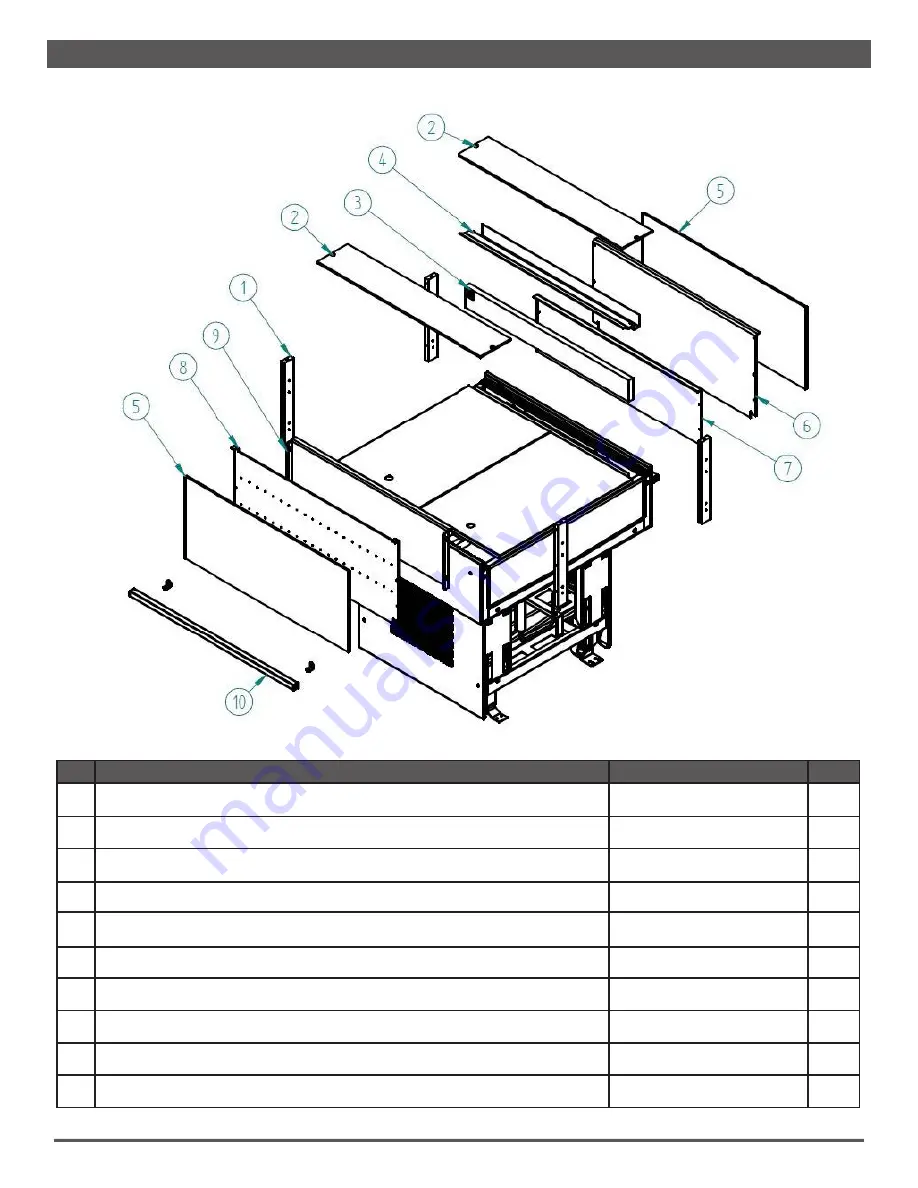
(BLANK)
37
PARTS LIST
END WALLS / SIDE BUMPER
#
DESCRIPTION
Part Number
PCS
1
Air Inlet End Wall DX/SX
P114146E
4
2
Plexi Worktop
P114147C
2
3
Honeycomb
P114148A
1
4
Honeycomb Holder
P114149K
1
5
Front/ Rear Glass
P114150F
2
6
Rear Closed Air Inlet
P114151D
1
7
Product Holder
P114152B
1
8
Front Holed Air Inlet
P114153M
1
9
Front Air Inlet
P114154H
1
10
Front and Back Bumper Rail Kit
P114155F
2
Summary of Contents for Hillphoenix MIDA
Page 5: ...3 TECHNICAL DATA MIDA Mobile Single Deck Self Contained Mercchandiser 3 X3 4 X4 4 X8 ...
Page 18: ...CASE CLEANING 16 SCHEDULED MAINTENANCE TABLE Fig 17 Recommended Cleaning Schedule ...
Page 26: ...24 PARTS ORDERING THIS PAGE LEFT BLANK ...
Page 36: ... BLANK 34 PARTS LIST MIDA 4x4 MIDA 4x8 PARTS ORDERING NOTES ...
Page 43: ... BLANK 41 PARTS LIST MIDA 3X3 PARTS ORDERING NOTES ...
Page 44: ...42 APPENDIX MIDA 3X3 MIDA 4X4 ...
Page 45: ......
Page 46: ...44 APPENDIX MIDA 4X8 ...
Page 47: ......
Page 48: ...46 MIDA 3X3 WIRING DIAGRAM ...
Page 49: ...47 MIDA 4X4 WIRING DIAGRAM C SERIAL NUMBER ...
Page 51: ... BLANK 49 MIDA 4X8 WIRING DIAGRAM C SERIAL NUMBER ...
Page 52: ... BLANK 50 MIDA 4X8 WIRING DIAGRAM C SERIAL NUMBER ...
Page 54: ...52 MIDA 4X8 WIRING DIAGRAM D SERIAL NUMBER ...
Page 56: ...54 ...