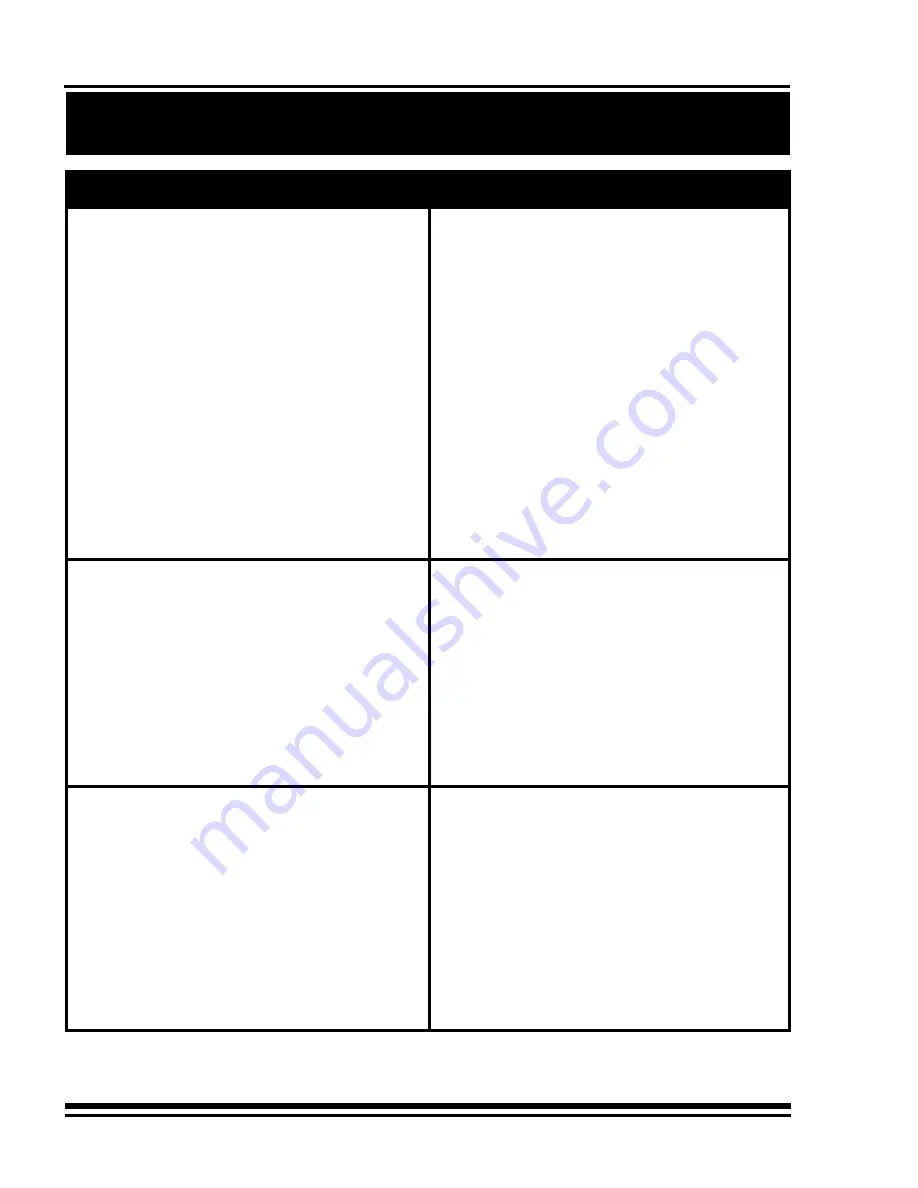
PAGE 12
FAILURE
PROBABLE CAUSE
a)
Brake plates or divider plates have been damaged by
contamination in the hydraulic fluid or lack of circulation
flow in the brake housing.
b)
Brake piston is seized in the brake housing because of
contamination in the hydraulic fluid.
c)
Excessive back pressure in the return line causes the
brake to be released.
d)
Control valve has incorrect spool which traps hydraulic
pressure in the brake piston when the control valve
handle is returned to neutral position. For proper function
of the automatic brake, both pressure ports of the winch
must be open to the reservoir in neutral position of the
control valve.
e)
Wire rope is fastened to the incorrect cable anchor slot.
f)
Sprag clutch is damaged or surfaces where sprag
clutch engages on motor drive shaft, or connecting
shaft, are worn or indented.
g)
Winch supplied with external brake release option is
not plumbed per HYDRAULIC CIRCUIT. Failure to
vent external brake release port to reservoir may trap
pressure and cause winch brake to slip.
a)
Pump is too slow. Pump rpm must be maintained at
normal operating speed when a load is lowered.
b)
Brake is running too hot. This is caused by a complete
lack of, or insufficient, circulation flow. To check the
circulation, observe the flow of oil from the circulation
return line of the winch (approx. 3.5 (US) gpm - 13 l/min)
when the winch is reversed.
c)
Control valve for the winch operation has poor metering
characteristics.
d)
Damaged brake plates or divider plates.
e)
The over-running clutch, which connects the motor
shaft with the brake assembly, is damaged.
f)
Air has mixed with hydraulic oil resulting in foamy oil.
a)
Oil leaks from the motor flange are caused by a
damaged O-ring seal on the motor flange.
b)
Oil leaks occurring between the cable drum flanges
and housing are caused by excessive pressure in the
brake housing. Excessive pressure in the brake housing
will damage the oil seal between the brake housing and
the cable drum interior.
c)
If the breather relief on the end cover leaks, the seal
between the drum interior and the brake housing is
damaged and must be replaced. This condition is
caused by excessive pressure in the brake housing of
the winch or operation with the incorrect hydraulic fluid
during cold weather or a restriction in the circulation
return line leading back to tank.
Brake will not hold.
Oil leaks.
Brake vibrates when lowering a load.
Refer to the SERVICE INSTRUCTIONS if it becomes necessary to disassemble the Model H8 winch.
248 REV.950715
TROUBLE SHOOTING