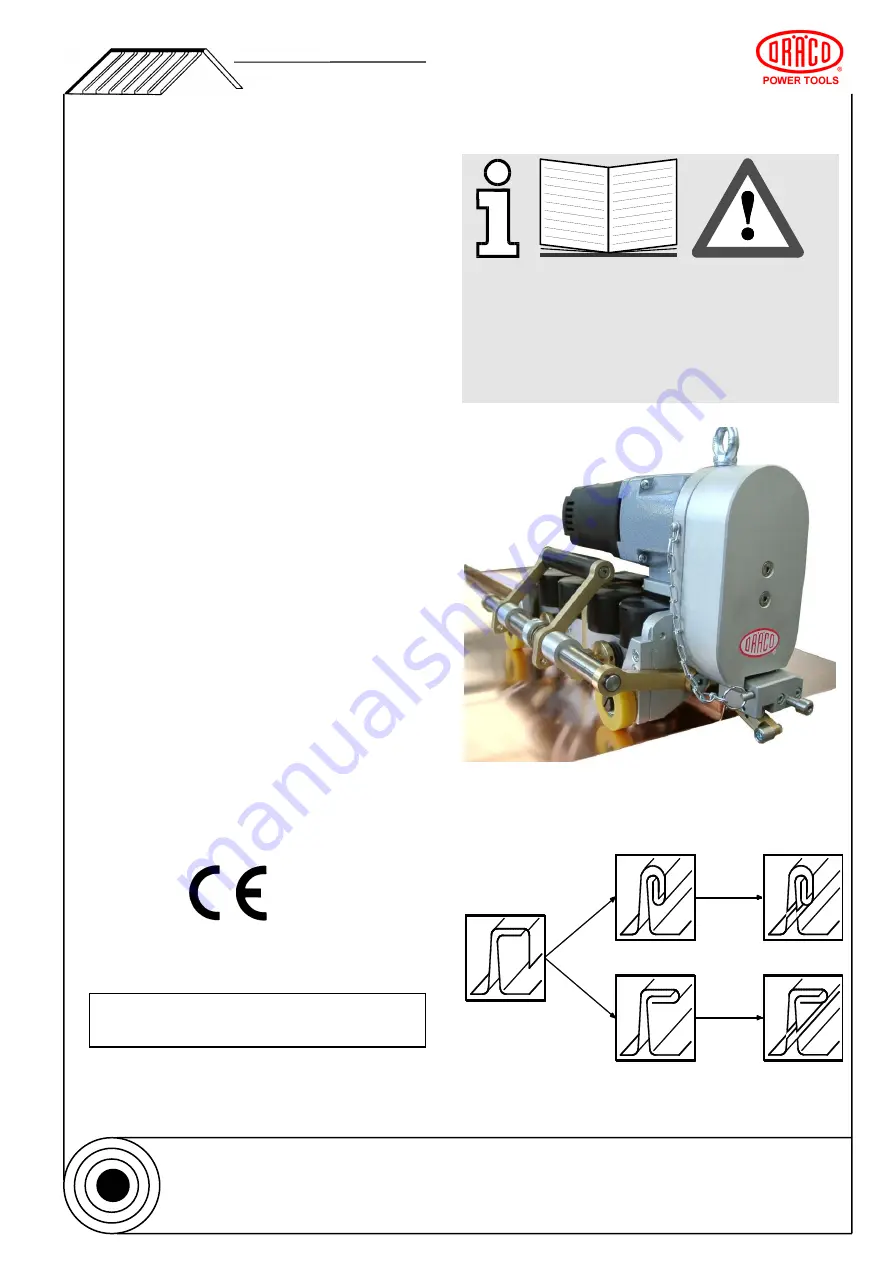
Instruction Manual
Automatic
Power Seamer
K9-1
(for Double Lock Standing Seam)
K9-1-WAD
(Complete version, for Single- and
Double Lock Standing Seam, Dual-
Safety Switch & Seam Cutting)
Please read this manual, before attempting to
operate this machine and observe all safety
regulations and signs.
Pic. K9-1-WAD
Mach.-No.: 04536
... the Roof- and Wall Program of
Max Draenert Apparatebau GmbH & Co.KG
– Electric – Cordless – Pneumatic Tools – Machines
Factory
1
D-73777 Deizisau
P.O. Box 1120
Phone +49-(0)7153-8217-0
Gutenbergstr. 15-17
D-73779 Deizisau
Fax
+49-(0)7153-8217-66
INTERNET http://www.dracotools.com
E-Mail: draenert@dracotools.com