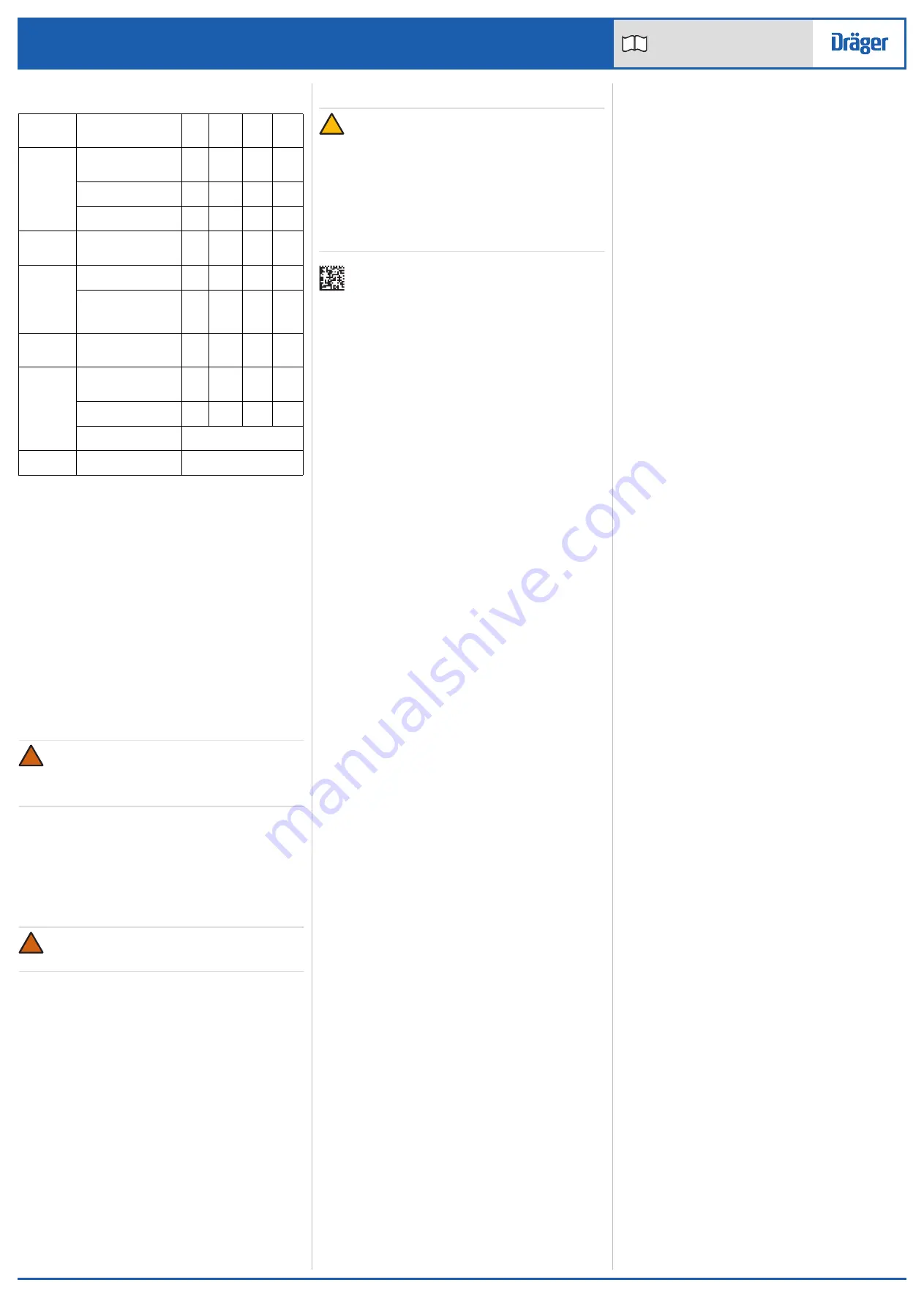
PAS
®
Micro Series
Airline/Short duration respiratory protection equipment with PAS
®
ASV
Instructions for Use
i
3359994 (A3-D-P) Page 3 of 3
Additional inspection and testing may be required in the country of
use to ensure compliance with national regulations.
Notes
O
Dräger recommendations
1. Clean the equipment if it is dirty. If it the equipment has been
exposed to contaminants, disinfect any components that come
into direct and prolonged contact with the skin.
2. These maintenance tasks may only be carried out by Dräger or
trained service personnel. Details of the tests are contained in
the technical manual which is issued to service personnel that
have attended a relevant Dräger maintenance course.
3. For type A check the O-ring on the lung demand valve; and for
type ESA check the outer surface of the male part of the push-
in connector on the lung demand valve. As a guide, lubricant
should be felt on the fingers but not seen. If relubrication is
required, lightly apply Dow Corning
®
Molykote
®
111 (other
lubricants are not tested and may damage the equipment).
5.2
Maintenance tasks
5.2.1
Removing the cylinder
WARNING
High-pressure air release may cause injury to the user or
other personnel near the breathing apparatus. Close the
cylinder valve and fully vent the system before attempting
to disconnect the air cylinder.
1. Close the cylinder valve and press the front button
(Fig 3, Item 3) to fully vent the system.
2. Loosen the cylinder strap.
3. Disconnect the cylinder valve from the pressure reducer.
4. Remove the cylinder. To prevent damage, ensure that the
hand wheel of the pressure reducer remains clear of the
cylinder.
5.2.2
Air cylinder charging
WARNING
Air quality for compressed-air cylinders must conform to
requirements of EN 12021.
●
Refer also to the instructions supplied with the cylinder and the
charging unit for recharging the cylinder.
●
Only charge compressed-air cylinders which:
○
Conform to national standards.
○
Feature the original manufacturer’s test date and test mark.
○
Have not exceeded the test date indicated on the cylinder
by the last testing station.
○
Are not damaged.
●
To prevent ingress of moisture into the cylinder, ensure that the
cylinder valve remains closed until connected to the charging
unit.
●
Recharge to the rated working pressure of the cylinder. Dräger
recommend a charge rate of 27 bar/minute (rapid charging will
increase the temperature resulting in an incomplete charge).
●
To prevent overcharging of the cylinder, Dräger recommend
using a pressure-limiting device on the charging compressor.
Component/
System
Task
After
use
Every
month
Every
year
Every
six
years
Complete
equipment
Visual inspection
(see Note 1 and
Section 3.1.1)
O
O
Functional test
(see Section 3.1.3)
O
O
Flow and static tests (see
Note 2)
O
Lung
demand
valve O-ring
Check and lubricate if
necessary (see Note 1)
O
Pressure
reducer
Medium-pressure check
(see Note 2)
O
Renew the high-pressure
connector O-ring and
sintered filter (see
Note 2)
O
Pressure
reducer and
PAS
®
ASV
Overhaul – Contact
Dräger for the Repair &
Exchange (REX) service
O
Cylinder
Charge to correct
pressure
(see Section 5.2.2)
O
Check the initial test date
stamped on the cylinder
O
Cylinder pressure test
and recertification
Carry out in line with national
regulations
Cylinder
valve
Basic overhaul
During cylinder pressure test
or on condition
!
!
5.3
Cleaning and disinfecting
CAUTION
Do not exceed 60 °C for drying, and remove components
from the drying facility immediately when dry. Drying time
in a heated dryer must not exceed 30 minutes.
Do not immerse pneumatic or electronic components in
cleaning solutions or water.
If water is trapped and then freezes inside the pneumatic
system of the breathing apparatus (such as the lung
demand valve), operation will be impaired. Prevent any
liquid from entering, and thoroughly dry the breathing
apparatus after cleaning to prevent this from occurring.
For information about suitable cleaning and disinfecting
agents and their specifications refer to document 9100081
on www.draeger.com/IFU.
Refer also to the Instructions for Use for the lung demand valve,
face mask and other associated equipment.
●
Use only clean lint-free cloths
1. Clean the breathing apparatus manually using a cloth
moistened with cleaning solution to remove excess dirt.
2. Apply disinfecting solution to all internal and external surfaces.
3. Rinse all components thoroughly with clean water to remove all
cleaning and disinfecting agents.
4. Dry all components using a dry cloth, in a heated dryer or in air.
5. Contact service personnel or Dräger if disassembly of
pneumatic or electronic components is required.
6
Storage
Store the equipment between -15 °C and +25 °C. Ensure that the
environment is dry, free from dust and dirt, and does not subject
the equipment to wear or damage due to abrasion. Do not store
the equipment in direct sunlight. Note also the following:
●
Extend the shoulder straps, the waist belt and the head
harness straps of the face mask.
●
For hygienic storage, place the face mask in a protective bag
(contact Dräger for supply of a suitable bag).
●
Route rubber hoses in such a way that the bend radius is not
too acute and the hose is not stretched, compressed or
twisted.
●
Fix the apparatus securely to any raised mounting point to
prevent it from falling.
7
Disposal
When required, dispose of the PAS
®
Micro in accordance with
national or local regulations for waste disposal.
8
Technical data
●
High-pressure connector: 200 bar or 300 bar, standard G5/8”
as per EN 144-2.
●
Independent air supply (single user):
○
Airline pressure and flow requirements: pressure 6 to
10 bar, air flow rate at least 550 litres/minute.
Important
note
: do not exceed 10 bar.
○
Airline hose requirements: maximum of 100 m of Dräger
approved hose.
Important note
: no more than four
individual hoses (a maximum of five hose connections) are
permitted in the airline.
●
PAS
®
ASV: whistle activates and switch-over occurs in the
range: 3.5 to 5.5 bar (airline pressure).
●
Pressure reducer: whistle commences in the range:
110 to 100 bar (cylinder pressure).
●
Whistles cease in the range: 1.75 to 0 bar (cylinder pressure).
●
Whistle volume: >90 dBA.
!