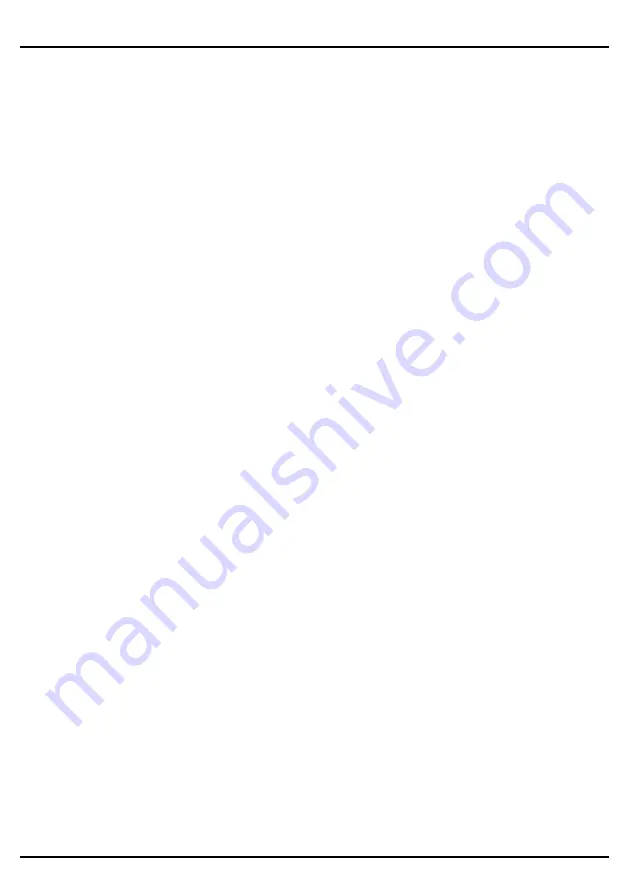
8
7. HEALTH & SAFETY INFORMATION
Always ensure that the product is fully inspected before every use, this will prevent damage
or serious injury to person.
7.1 FREQUENT INSPECTION
A visual inspection is to be carried out by a trained person before every use. This inspection
should consist of:
- Evidence of slippage on the braking mechanisms.
- Inspection of the load chain for wear, lubricant, damaged chain links or dirt.
- Hooks for damage, fracture marks, cracks, latch engagement and latch operation.
- Any missing parts or safety devices
- Housing is not distorted.
7.2 PERIODIC INSPECTION
An appointed person who over see the visual inspection and ensure that records are taken to
ensure continue evaluation.
It will be necessary to partially disassemble the unit to perform more periodic inspection.
The periodic inspection are to include the following -
- more in depth inspection to look for wear, cracks or distortion of all parts of the chain
hoist
including - hooks, chains, chain guide, hook collar, dead end stud, all nuts, bolts
and pins, shafts, gears and bearings.
- Inspection of the chain for excessive wear or stretch, (see maintenance section for
further
details on Gaging Load Chain Wear).
- Inspection for wear on the tip or the pawl, teeth or the ratchet and pockets of the lift
wheel
and hand wheel, hook block sheaves and hanger sheaves
- Loose or missing bolts, nuts, pins or rivets.
- Inspection for corroded, stretched or broken pawl spring.
- Inspection of the brake compartment for worn, glazed, or oil-contaminated friction discs
and
scoring of the hand wheel hub, ratchet and friction hub.
Any deficiencies noted are to be corrected before the hoist is returned to service.
Any parts that are deemed unserviceable are to be replaced with new parts before the unit is
returned to service.