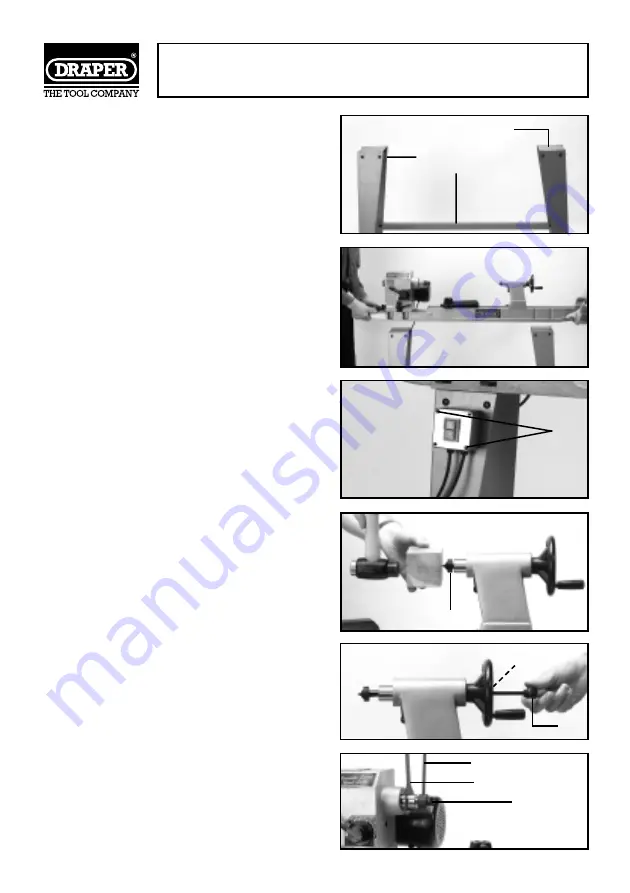
- 6 -
ASSEMBLY
Wood Lathe Stand
Using the nuts and bolts supplied, fix
together both the top plates
✪✌
with the four
legs
✫✌
. Bolt on the shelf (WTL95) or four
supports (WTL90)
✬✌
and tighten all the
fixings.
Fig.2.
Note: The Wood Lathe stand should always
be fastened down securely to the floor
using four suitable fixings (not supplied).
Mounting the Wood Lathe to the Stand
Lift the lathe onto the stands top plates (seek
assistance as this is very heavy). Align the
holes in the bed with the stand and bolt in
place using the 8 fixings supplied.
Fig.3.
No-Volt On/Off Switch
The no-volt switch is recommended to be
fixed into place on the leg of the stand using
the two bolts
✭✌
which are longer, coming
through the rear of the switch box.
Fig.4
.
Note: Make sure the cable from the switch
to the motor will allow the rotation of the
headstock. Ensure the lead never passes
between bed and workpiece.
Drive Spur and Live Centre
Locate the drive spur (with prongs) and the
live centre (with bearing) from the
packaging. Insert the live centre
✮✌
into the
barrel of the tail stock and with a piece of
scrap timber and a hammer, tap the spur in
until secure. Carry out the same procedure
for the drive spur into the headstock spindle.
Fig.5
.
Removal
When the need arises to remove the spurs,
use the ejection pin
✯✌
to push out the live
centre from the tailstock by inserting it down
the centre of the tailstock handwheel hole
✰✌
.
Fig.6
.
The drive spur is removed using the ejection
pin
✱✌
and the spindle holding wrench
✲✌
.
Using the wrench to hold the spindle on the
flats, insert the ejection pin into the hole in
the side of the thread protection cap
✳✌
.
Undo the cap which will force the spur out of
the spindle.
Fig.7
.
Fig.2.
Fig.3.
Fig.4.
Fig.5.
Fig.6.
Fig.7.
✬✌
✫✌
✭✌
✮✌
✰✌
✯✌
✱✌
✲✌
✳✌
✪✌