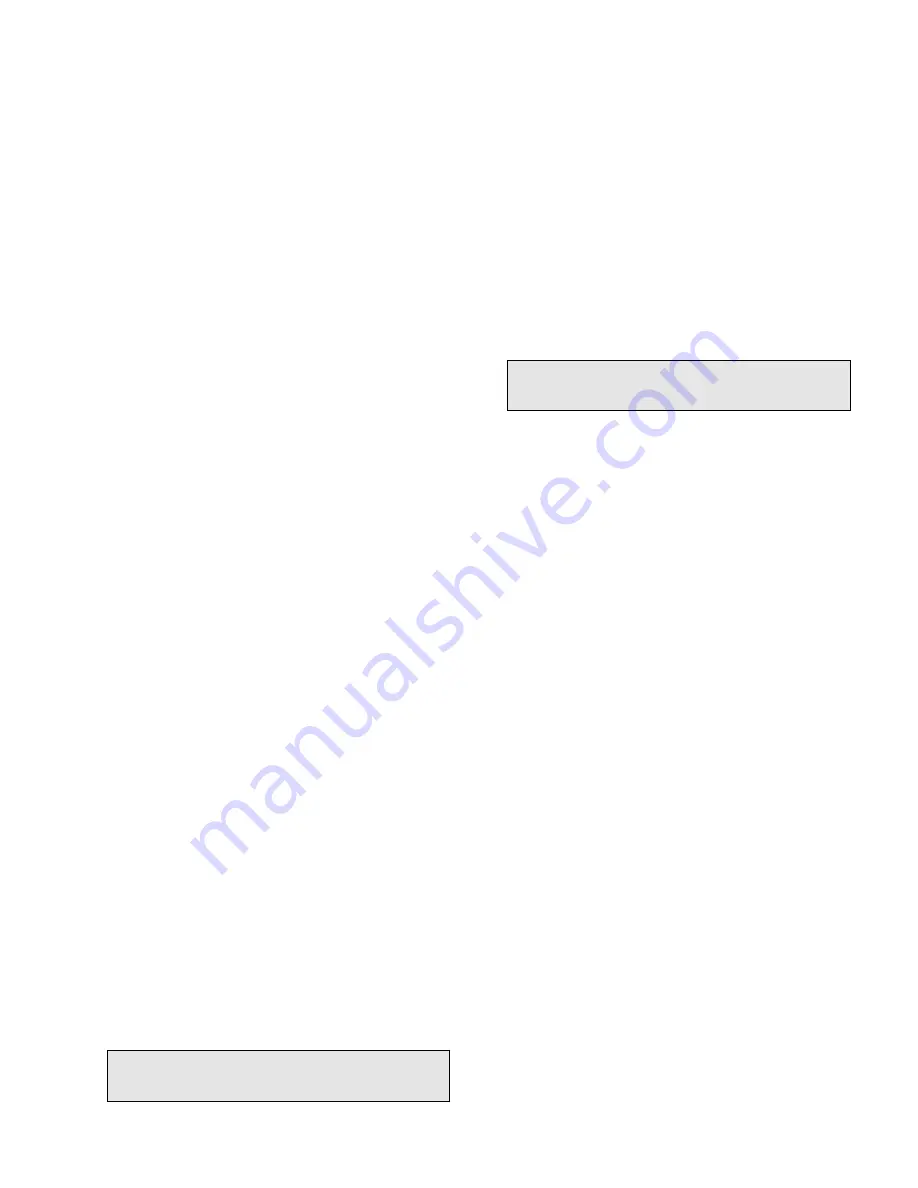
Instruction ES2007 4/98
Models 4700P and 4700E
24
5.
Remove cap screws (10) and separate body S/A from
the case S/A.
6.
Remove the diaphragm assembly (9), and reducer
plate if 6-30 psi range 4700P.
7.
Clean the body (1). Avoid the use of detergents that
might deteriorate the diaphragm S/A. Use isopropyl
alcohol. Do not use chloride-based solvents.
8.
On 4700E, carefully remove the three O-rings from the
bottom of the module. Inspect for any nicks or deterio-
ration. Replace if necessary. Clean bottom of module
using isopropyl alcohol. Carefully reassemble O-rings
into grooves. Make sure they are seated in bottom of
groove.
Caution: Do not use any lubrication on
O-rings or base.
Reassembly (Figure 19 - 4700P, or Figure 20 - 4700E)
1.
Position the diaphragm assembly (9) on the case
subassembly. If positioner is 6-30 psi range, install
reducer plate per Figure 19. Secure the body subas-
sembly to the case subassembly with cap screws (10).
Tighten evenly to 60 inch-lbs of torque.
2.
Replace spring (5), lever S/A (3), washer (16), and
retaining ring (17).
3.
On 4700E, carefully place module in position against
body making sure that O-rings do not come out of
grooves. Secure to body using screws (21).
4.
Install the pilot assembly (11) and pressure gauges.
5.
Install the positioner on the actuator. Reconnect air
lines, electrical leads if 4700E, and coupling linkage if
mounted on reciprocating valve.
6.
Assemble cam to shaft per procedure under “Cam
Lobe Change”. Recalibrate per appropriate Valve
Action/Positioner Action calibration section.
Diaphragm
If the diaphragm has deteriorated, the diaphragm assembly
should be replaced. This requires separation of the body
and case subassemblies as outlined under Body Disas-
sembly, page 24.
I/P Module
Replacement of the I/P module requires removal of electri-
cal connections, including conduit if used. Remove posi-
tioner from valve if module mounting screws are not
accessible. Remove and replace module as outlined under
Body Disassembly, page 24.
Note that there are no adjustments in the I/P module.
Pilot (Figure 18)
To clean or replace deteriorated parts, the valve must be
isolated from process. Shut off air supply. To minimize
maintenance time, it is recommended that the entire pilot
subassembly (11) be replaced by a new subassembly, so
that the old unit can be worked on when time permits.
Disassembly
1.
Unscrew the pilot subassembly (11) and disengage it
from the body (1).
Note: Turn the pilot subassembly
while removing it to prevent damage to the
O-rings.
2.
Remove end plug and withdraw the spring, plug and
extension pin. If necessary, use a penetrating oil to
free parts. Do not disassemble or adjust extension
pin.
3.
Wipe the parts with a clean soft cloth and blow
compressed air through the orifices. Use isopropyl
alcohol to clean. Do not use chloride based solvents.
Reassembly
1.
Install three new O-rings on the pilot spool. Put a light
coating of silicone grease on each O-ring.
2.
Replace the extension pin and the plug, countersunk
end first into the pilot spool. The plug should slide into
the pilot spool by its own weight.
3.
Install the spring in the pilot spool. The end having the
smallest diameter must be in contact with the plug.
Screw the pilot end plug into the pilot spool.
4.
Install the pilot subassembly (11) into the body (1).
Body
Shut off the air supply. Disconnect air lines, linkage if
reciprocating, and electrical connections if 4700E. If
positioner is reverse acting, refer to applicable section
under “Cam Lobe Change” to safely remove cam. Remove
screw (28), washer (27), cam (26). Separate positioner from
actuator by removing screws (29) and washers (30).
Disassembly (Figure 19- 4700P, or Figure 20- 4700E)
1.
Remove pressure gauges (12) (13), and on 4700P
only (14).
2.
Remove the pilot subassembly (11).
3.
Remove retaining ring (17), washer (16), lever S/A
(3), and spring (5).
4.
On 4700E only, remove 4 screws (21) to separate I/P
module from body.
Caution: Do not damage or lose the three
O-rings on bottom of module.
Summary of Contents for Masoneilan 4700E
Page 15: ...15 Instruction ES2007 4 98 Models 4700P and 4700E Figure 14 FM Installation ...
Page 16: ...Instruction ES2007 4 98 Models 4700P and 4700E 16 Figure 15 CSA Installation ...
Page 17: ...17 Instruction ES2007 4 98 Models 4700P and 4700E Figure 16 CENELEC Installation ...
Page 32: ...Instruction ES2007 4 98 Models 4700P and 4700E 32 Figure 20 4700E Rotary Reciprocating ...