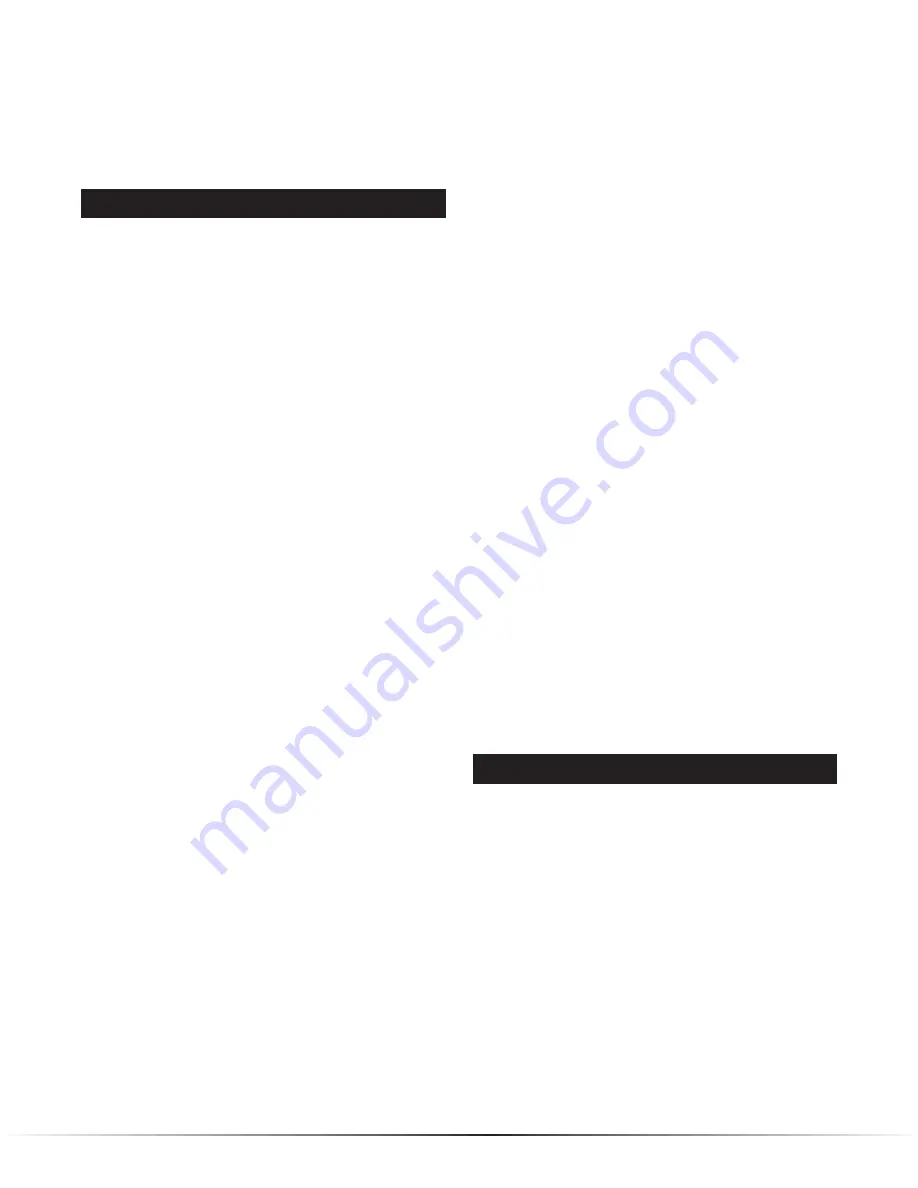
Flowgrid Slam Shut | 5
Hydrostatic Testing
All slam shut valves and slam shut valves integrated into Flowgrid
valves are hydrostatically tested at the factory prior to shipment
according to ISA-S75.19-1989 and MSS-SP-61 standards.
Installation
Personal injury, equipment damage, or leakage due to
explosion of accumulated gas or bursting of pressure
containing parts may result if this slam shut is over
pressured or is installed where service conditions
could exceed the limits given in the specification of
this manual or on the nameplate, or where conditions
exceed any ratings of the adjacent piping or piping
connections. Verify the limitations of the Flowgrid
regulator, Slam Shut valve and pilot to ensure none of
the devices are over pressured. To avoid such injury
or damage, provide pressure relieving or pressure
limiting devices as required by applicable codes to
prevent service conditions from exceeding those limits.
Additionally, physical damage to the regulator could
result in damage such as breaking the pilot (if supplied)
off the main valve, causing personal injury and/or
property damage due to explosion of accumulated gas.
To avoid such injury and damage, install the slam shut
and regulator in a safe location.
NOTE: The slam shut may be supplied as a stand alone
unit or integrated into a Flowgrid
®
regulator with filters,
restrictors and pilots. This procedure covers the instal-
lation of the slam shut and may refer to components not
ordered with the slam shut. Consult the proper IOM for
the installation of Flowgrid
®
regulator, filters, restrictors
and pilots.
1. PERSONNEL:
Installation of the slam shut valve and/or
Flowgrid
®
regulator should be made by qualified person-
nel familiar with high pressure piping and pilot operated
regulators.
2. PRIOR
INSPECTION:
Inspect the slam shut valve,
regulator, pilot, and tubing for any damage that might
have occurred in shipping. Make sure the body, pilot lines,
and inlet piping are clear and free from foreign material.
3. ORIENTATION:
Stand alone slam shuts must be
installed up stream of the pressure regulator to provide
secondary protection. The slam shut valve or slam shut
integrated into a Flowgrid
®
regulator may be installed in
any position, the best position being one that provides
easiest access for the slam shut, pilot adjustment and
maintenance.
4. SCREWED END VALVES:
Apply pipe compound to the
male threads starting one or two threads back from the
end prior to assembling the joint.
5. FLANGED END VALVES:
Use suitable line gaskets and
good bolting practices with flanged bodies. A crisscross
pattern of incrementally tightening the line bolts is
recommended.
6. WELD END BODIES:
Before welding a butt weld and/
or a socket weld valve body, disassemble the valve. On
stand alone slam shuts remove the bonnet, slam shut
body assembly and all O-rings. On slam shuts integrated
into Flowgrid valves; remove the slam shut body assem-
bly, Spring Case and all trim parts including diaphragm
and O-rings. Reassemble the valve (refer to the
MAINTENANCE section of this manual for Disassembly
and Assembly procedures) and pressurize to check for
leaks prior to putting the valve in service.
7. SLAM SHUT SENSE LINE:
Install a 3/8 inch OD tube
from the sense port to a port on the pipe line located 8 to
10 pipe diameters minimum of straight pipe downstream
of the final regulator in the run. The sense port is located
on the downstream side of the controller and latch
module just above the slam shut label, see Figure 8.
NOTE: The sense line connection should be away from
areas of turbulence (such as valves, reducers, and
elbows) and should have a full opening into the pipe free
from burrs, drill peels, and weld slag. Shutoff valves are
not required in the control line(s), but if installed, they
should be of the full opening type.
8. INLET PRESSURE LINES:
All pilots or other devices
requiring a supply of inlet pressure that can result in a flow
of gas downstream of the slam shut must be connected
to the center port (port inlet) on the slam shut body
assembly shown in Figure 8. A shut off valve may be
installed in the vent line to prevent the SSV from closing
during setup of regulators and other equipment and to aid
in setting up the slam shut valve.
Connection of any device such as a pilot to the inlet
port on the valve body can result in the flow of gas
downstream of the slam shut canceling the secondary
downstream pressure protection of the slam shut. This
may result in personal injury, death, equipment damage,
and/or bursting of pressure containing parts and/or
leakage of gas resulting in explosion of accumulated gas.
WARNING
WARNING