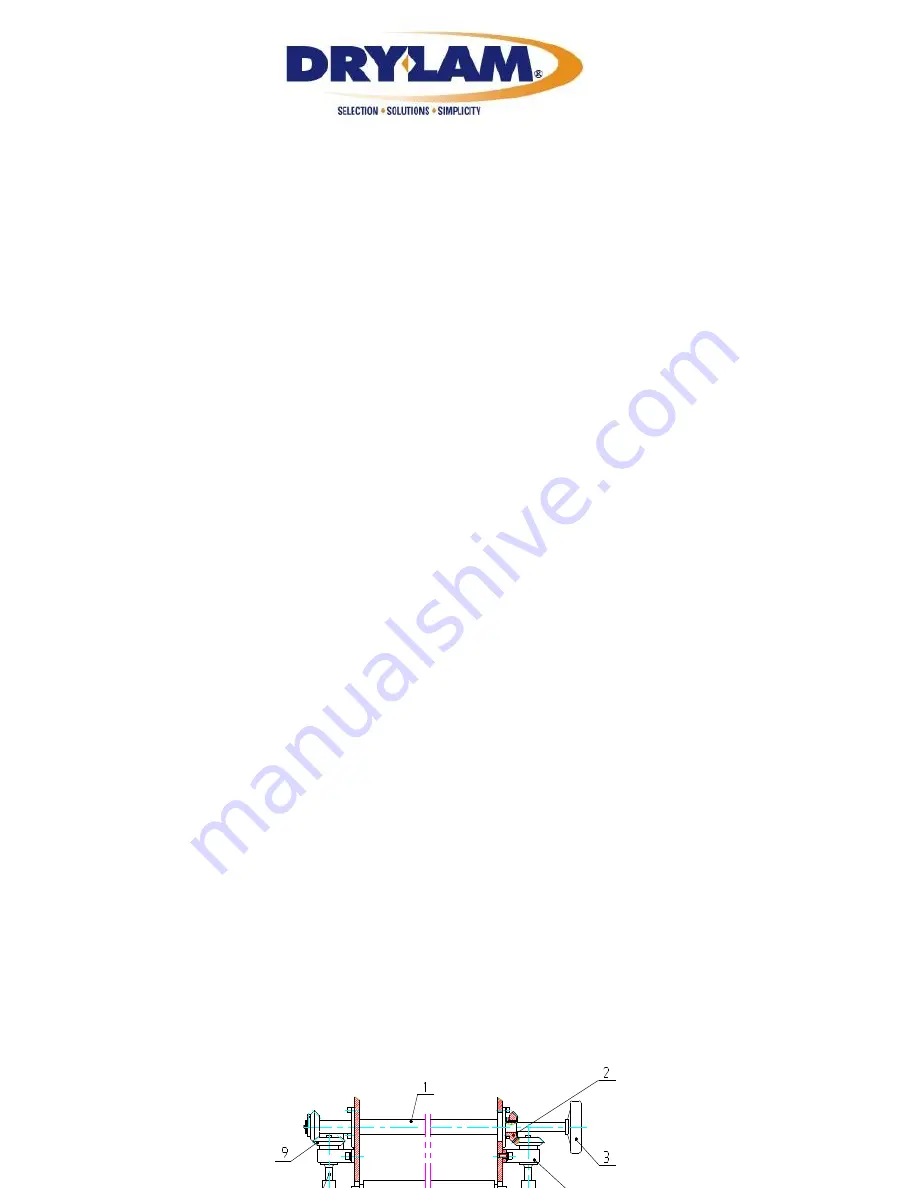
LPV1200 DUO SYSTEM
Page 34 of 40
(I)
Checking
methods and adjustment for pressure balance of rollers:
The adjustment of the space between the two rollers will be completed during operations.
While not in use, the asymmetry of the space between the two rollers is caused by the space of
screw threads of journey adjustment structures, which does not affect the normal uses. If the
quality of the laminating is influenced, please make examinations and adjustment in the
following steps.
●
Checking steps & methods of adjustment:
●
Open the left and the right cabinets;
●
Check whether the left and right pressure adjustment brackets are loose. If it is, please adjust
the pressure adjustment brackets and then fasten it;
●
Check whether the fore-and-aft taper gears on the two sides are loose. If the left gear is loose,
please dismantle it and then remove the screws of pressure adjustment brackets, after the
fore-and-aft taper gears declines, please fasten the screws on the top of gears, and then place
each component back to where they were; if the right taper gear is loose, it is no need to
dismantle it. Other procedures are the same as the left.
●
Adjustment methods for the space between the two rollers: (please refer to Figure 13)
Place the printed material with proper length (usually 5.9” wider than the film at the both
sides) between the two rollers, turn the pressure adjust hand wheel to make the upper roller
contact with printed material, and make a visual examination of the spaces of rollers and the
two sides of the printed material.
If the spaces are inconsistent with each other, please remove the left transverse taper gear;
turn the fore-and-aft taper gear until the spaces at the two sides of rollers is even.
Assembly the left transverse taper gear and blocking plates and fasten the screws on each
component.