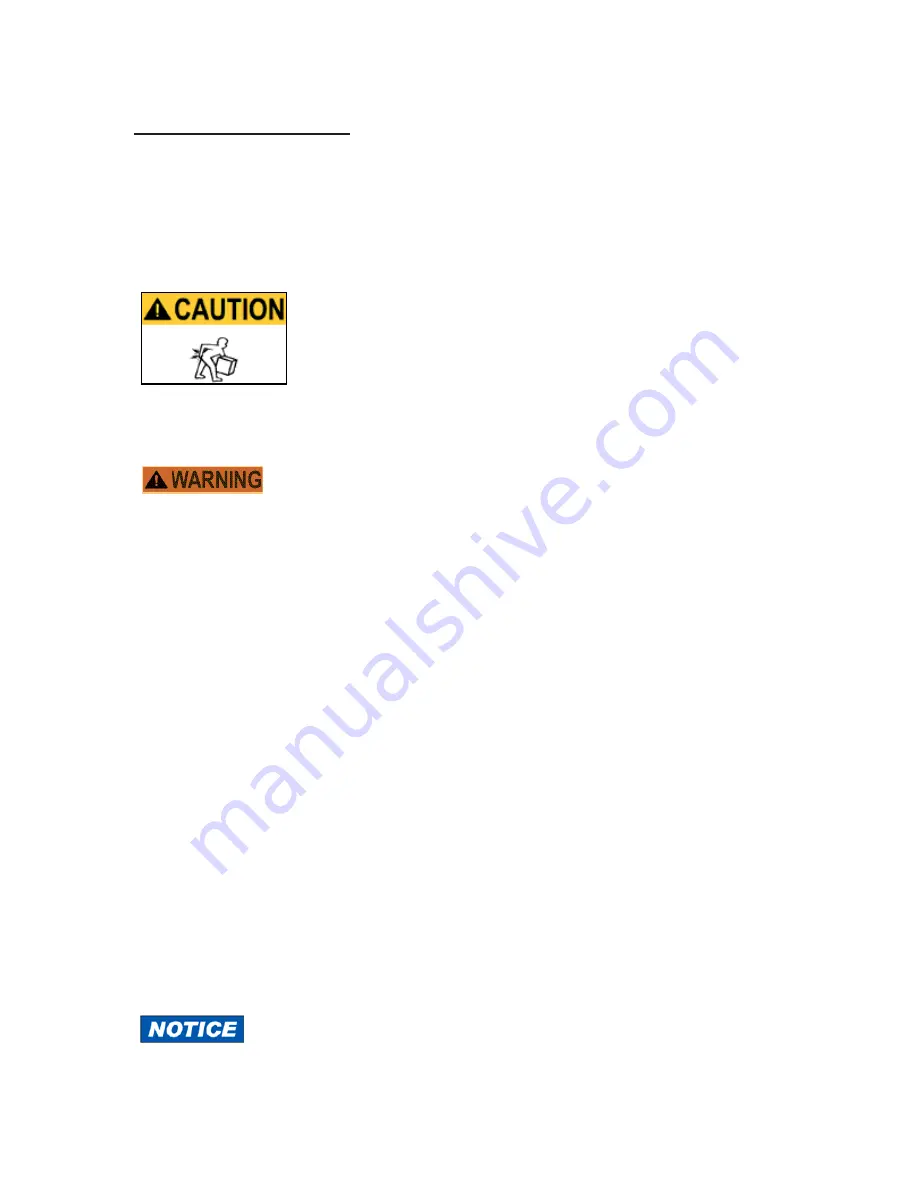
11
Unpacking and Installation
Upon receipt of your new
Jet
Mounter
™
, inspect the carton(s) carefully for signs of physical
damage or mishandling. Report any damage to the shipping company immediately and
contact Drytac Corporation if replacement parts are needed. If no damage is apparent,
proceed with the unpacking.
It is recommended that two people unpack the JM18,
JM 26 and
JM34 to avoid damage to the equipment or personal injury. To
unpack the JM44 and 54 you must follow the instructions affixed to
the top of the crate
in the sequence described
. If the instructions
are missing be sure to contact Drytac Technical Services before attempting to unpack or
install the machine.
Due to the weight of the JM44 and JM54 laminators a hoist or suitable lift must
be used to position the machine on an appropriate table or stand.
Select a clean, well-lighted working area that allows access to both the front and back of the
machine. Position the machine on a level, sturdy surface that can support the weight of the
machine and is at an optimum working height for the operator. (See Technical Specifications
Chart on page 30 for individual weight and size dimensions). The JM
44‟s and JM54‟s are
available with optional stands that have casters for ease of movement as well as a storage
rack for preloaded supply shafts.
Jet
Mounter
™
laminators,
depending on the country in which the machine was purchased, a
re
supplied in either a 115 VAC or 230 VAC versions. The power requirements for your
particular machine are marked on the rear panel adjacent to the power connector. Please
confirm that you have the correct power source available at the chosen location. If there are
any questions about electrical requirements for the equipment, please contact a qualified
electrician
prior to attempting to power up the machine!
Be absolutely certain that the
voltage supplied at the outlet corresponds with the voltage marked on the plate attached to
your machine. Do not rely on the cord or outlet configuration to determine the correct power
supply voltage!
ALLOW ENOUGH WORKSPACE AROUND THE MACHINE TO BE ABLE
TO FEED AND REMOVE YOUR WORKPIECE SAFELY!