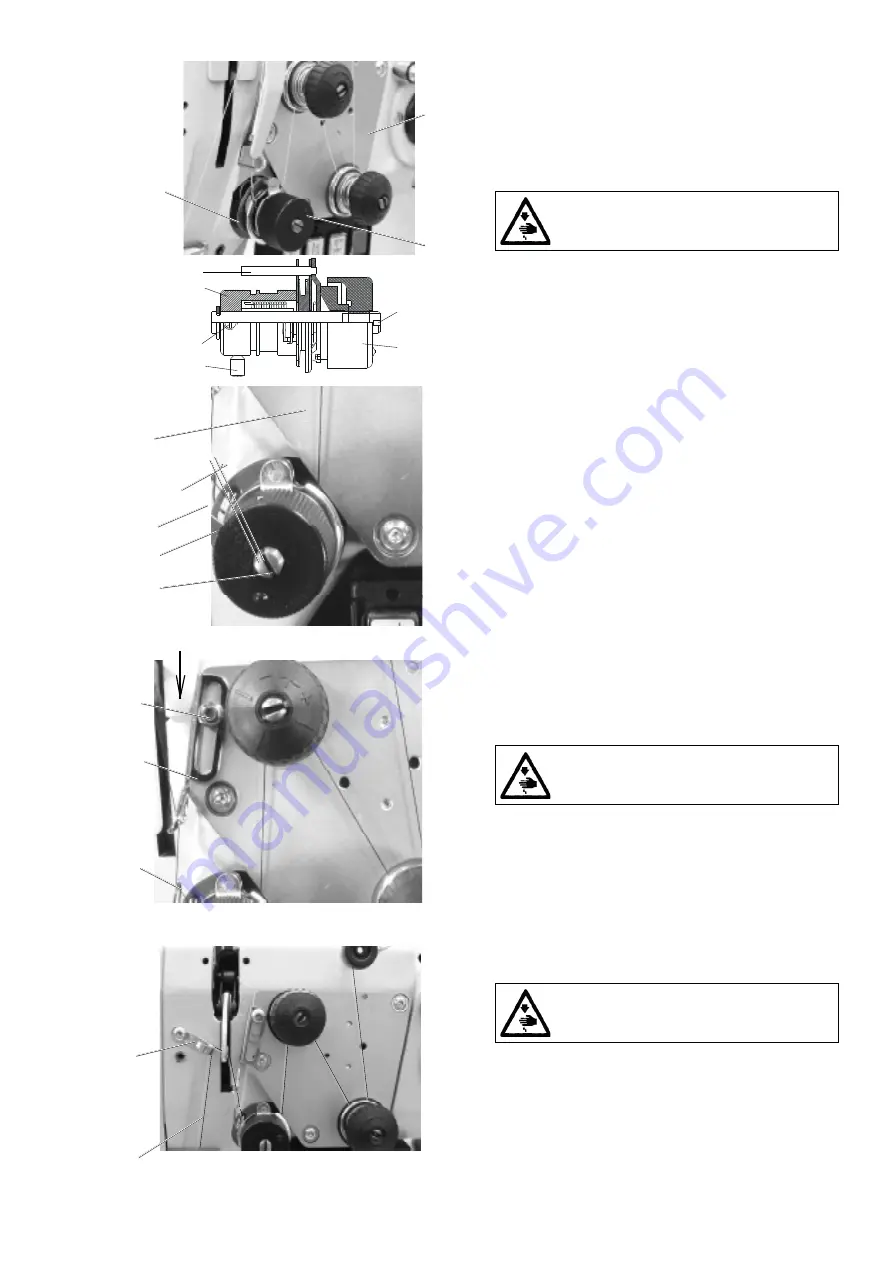
9
3.4.4 Setting the adapting spring
The mechanism of the adapting spring is in the machine arm set by the
pin (1) and fixed by the screw (2). The axial adjustment shall ensure
that the surfaces of the parts (3) and (4) are aligned (the threaded
thread must in no place break on edges). The initial position of the
adapting spring (5) shall ensure that B = 1 to 1.5 mm (see the
Figure).
Caution! Danger of injury!
Switch off the main switch! Before starting the setting
operation, wait until the motor stops!
-
Loosen the screw (2) and take the mechanism out of the machine
arm.
- Turning the body (6) relative to the pin (1), set the required initial
position of the adapting spring /the screw (7) has been set at the
producer´s so as to permit the turning movement of the body (6) the
screw must not be fully tightened/.
- During the installation of the mechanism into the machine arm take
care of the axial adjustment of the mechanism.
- Retighten the screw (2) and check the adjustment.
- Loosen the nut (8) of the mechanism, insert a screwdriver into the
notch of the screw (9) and set the required value of the adapting
spring. By turning the screw clockwise you increase the spring
force, and vice versa.
- Retighten the nut (8) and check the function of the adapting spring.
3.4.5 Setting the thread limiter
The thread limiter is to be set in such a way that, when sewing and
passing the thread through the most distant point of the hook, the
spring (2) shifts by about 1/4 to 1/2 length of its total length. This
means that the thicker will be the sewn material and the longer will be
the stitch length, the more will be the limiter shifted in the sense of the
arrow and inversely. Under standard sewing conditions, the thread
limiter is set in its tested positions depending on the sewing category
in accordance with the chapter 11.
Caution! Danger of injury!
Switch off the main switch! Before starting the setting
operation, wait until the motor stops!
- Tighten the screw (3).
-
Set the thread limiter (1) so as to ensure a minimum motion of the
adapting spring (2) when the thread passes around the bottom of
the hook.
- Tighten the screw (3).
3.4.6 Setting the additional thread limiter
For improving the uniformity of stitch interlocking with some (e.g. too
thin) materials, the machine is provided with an additional thread limiter
which is to be set as follows:
Caution! Danger of injury!
Switch off the main switch! Before starting the setting
operation, wait until the motor stops!
- Set the stitch length to the required value.
- Sew an approximately 5 cm long seam along the edge of sewn work,
switch off the machine, and tilt away the hook cover.
- Rotate the handwheel until the thread taken up by the hook will be
stretched across its bottom, i.e., across the full diameter of the hook.
- Adjust the position of the additional limiter (1) so as to obtain an
almost complete stretching of the thread (2) at that moment, as shown
in the drawing.
- Sew next stitch and check the adjustment.
2
3
1
5
A
4
9
3
6
7
1
2
8
9
2
1
8
3
4
All manuals and user guides at all-guides.com