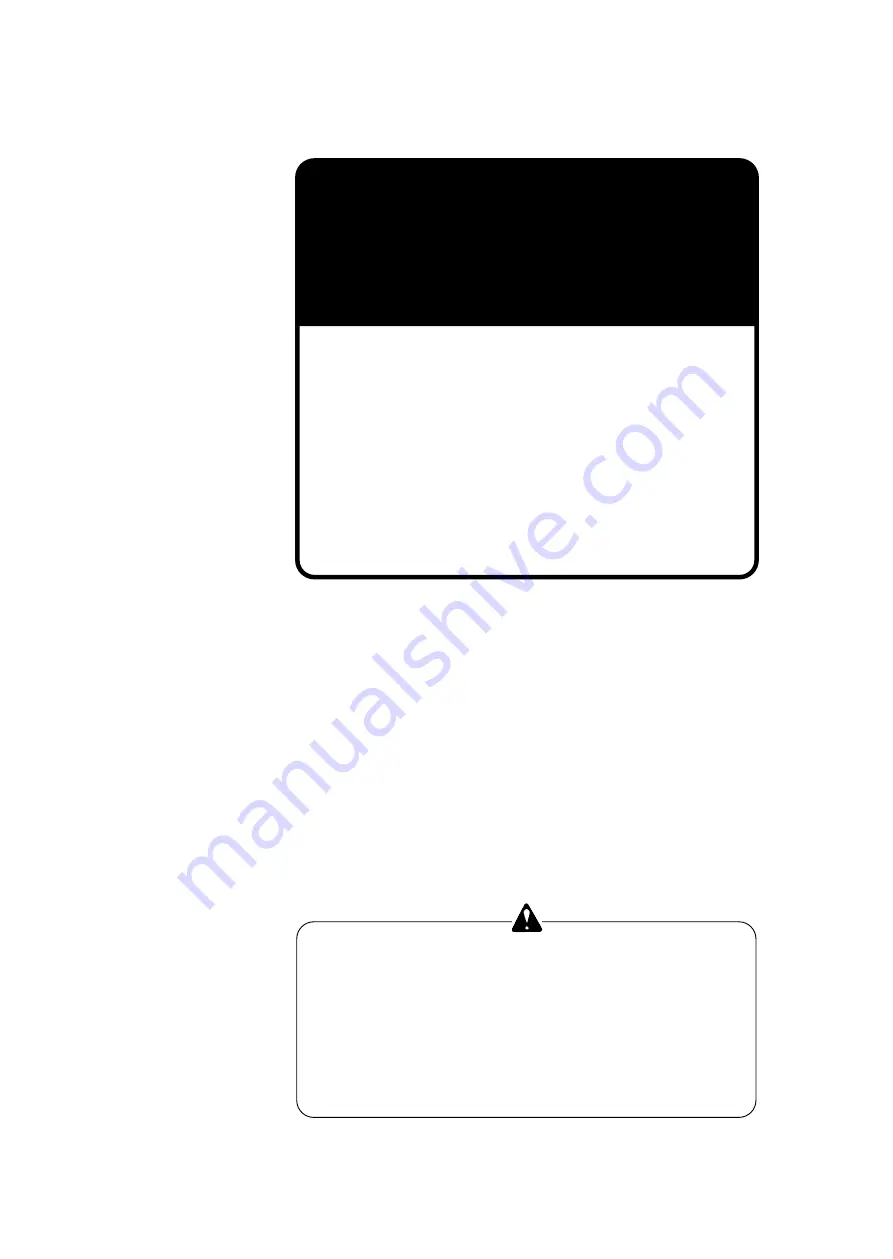
N5-Y1071 2002.12
DUPRINTER
Ver.2
DP-460/DP-440
DP-430/DP-340
DP-330/DP-330L
SERVICE MANUAL
Be sure to read this manual carefully, so that you
repair and service this machine safely and
correctly. Do not begin work until you have
thoroughly understood the contents of this manual.
Repairing or servicing the machine with insufficient
knowledge about it could lead to unforeseen
accidents or falls in the machine's performance or
quality.
DUPLO SEIKO CORP.
Summary of Contents for Duprinter DP-330
Page 9: ......
Page 11: ......
Page 18: ...c Dimensions chap 1 17 MEMO...
Page 24: ...4 8 2A 2B 2C 44000A1e b Part Names and Their Functions chap 1 23...
Page 152: ...151 MEMO...
Page 193: ...192 MEMO...
Page 329: ...328 x Overall Wiring Layout chap 8 15 Overall Wiring Layout 2 Drive PCB 2 2...