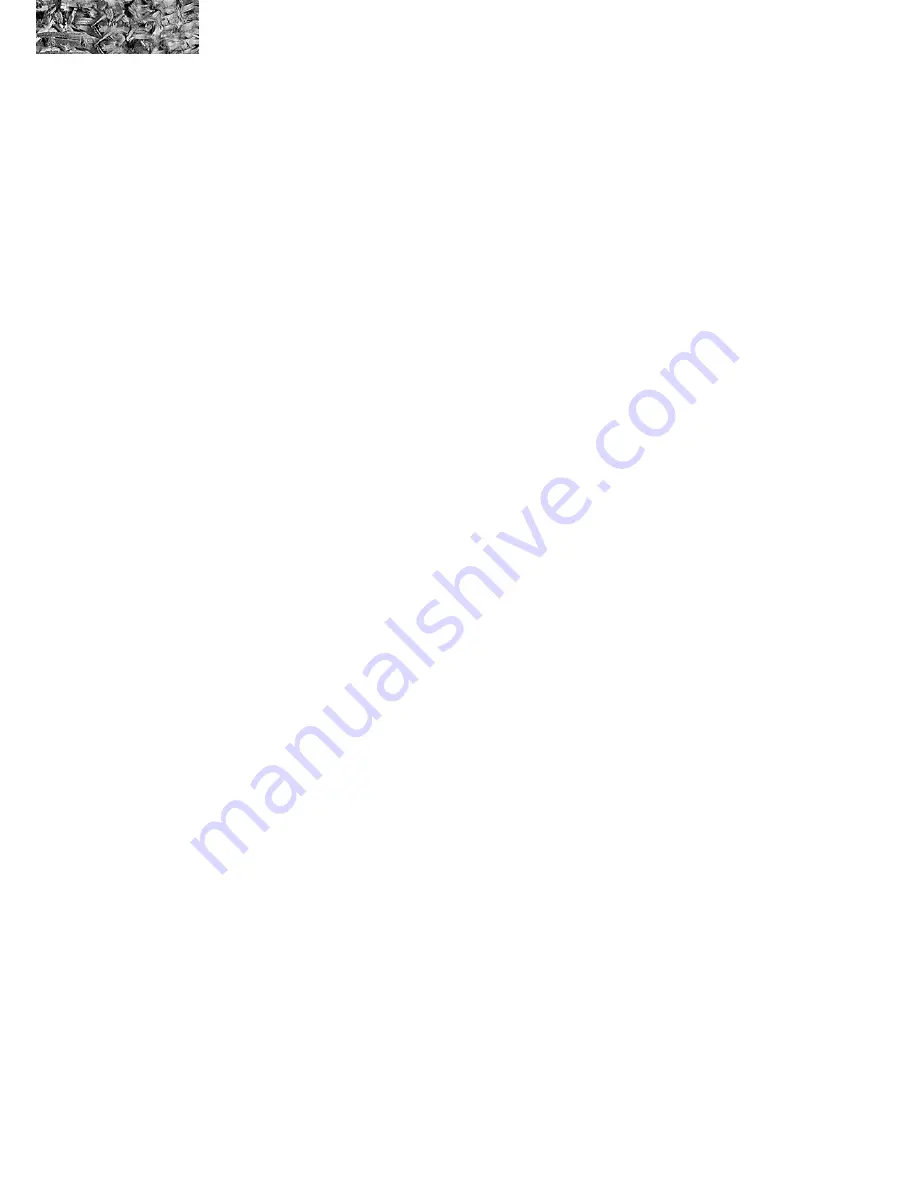
40
T C - 1 5 T R E E C H I P P E R
O P E R A T I N G I N S T R U C T I O N S
•
The feed roll output speed will be set to eeTreeMode setting.
Engine RPM
•
The control will monitor the chipper speed, and based on when the engine rpm will proportionally control
the feed roll speed until the speed drops to its programmable adjustable set point, will determine when the
feed roller reverses.
•
There will be an engine rpm set point and time of reversal setting for when the drop set point is reached.
•
When the engine rpm starts to rise and reaches a programmable adjustable set point, the feed rollers will
turn back on in the forward direction.
•
If engine rpm does not reach the forward set point, feed roll stays in neutral
•
This rpm will be taken off of the Engine flywheel (126 pulses per revolution)
•
Low rpm fault
•
When feed roll forward is on, and engine rpm is below its programmable adjustable set point for 10
seconds, the low rpm fault is true. If the rpm fault is true, the operator will have to momentarily reselect
the direction desired with the switch.
•
If engine rpm is below its programmable adjustable set point when the feed roll forward is pressed, the
low rpm fault will be true. The engine rpm will have to be raised above the programmable adjustable set
point and the feed roll forward switch will need to be pressed to start operation.
Safety Bar
•
If safety bar is pressed or disconnected, the feed roller will stop.
•
Feed roll will not go into forward position until Safety Bar Reset is pressed and the operator will have to
momentarily press the forward direction with the feed forward switch.
•
The safety bar will have no effect on the feed roller reverse switch; the feed roller will reverse at all times.
Safety Bar Reset
•
Any time the safety bar is pressed, the safety bar reset will need to be pressed to reset the safety bar.
•
If the safety bar is pressed, the operator must press the safety bar reset and then press the feed roll forward
switch to continue forward movement of the feed rollers. If the safety bars have not reset, the feed rollers
will not move forward.
Winch Override
•
Any time the winch override input is turned on the feed roll will stop and the feed speed will = 100%.
LED Fault Lights
•
The DCV710 has four Red/Green LEDs. Two are positioned on each side. The application can switch the
meaning of the LEDs using the Programming Tool DVC710 IO configuration screen. Note the Power On
period time can be changed as well. This is provided so that depending on how your controller is oriented
in your vehicle the appropriate LEDs for your application can be seen.
Summary of Contents for TC-15
Page 2: ...Clearing the Way for a Better Tomorrow...
Page 4: ...Clearing the Way for a Better Tomorrow...
Page 49: ...41 T C 1 5 T R E E C H I P P E R O P E R A T I N G I N S T R U C T I O N S...
Page 50: ...42 T C 1 5 T R E E C H I P P E R O P E R A T I N G I N S T R U C T I O N S...
Page 54: ...46 T C 1 5 T r e e C h i p p e r P A R T S R E F E R E N C E T R A I L E R A S S E M B L Y...
Page 60: ...52 T C 1 5 T r e e C h i p p e r P A R T S R E F E R E N C E D I S C A S S E M B L Y...