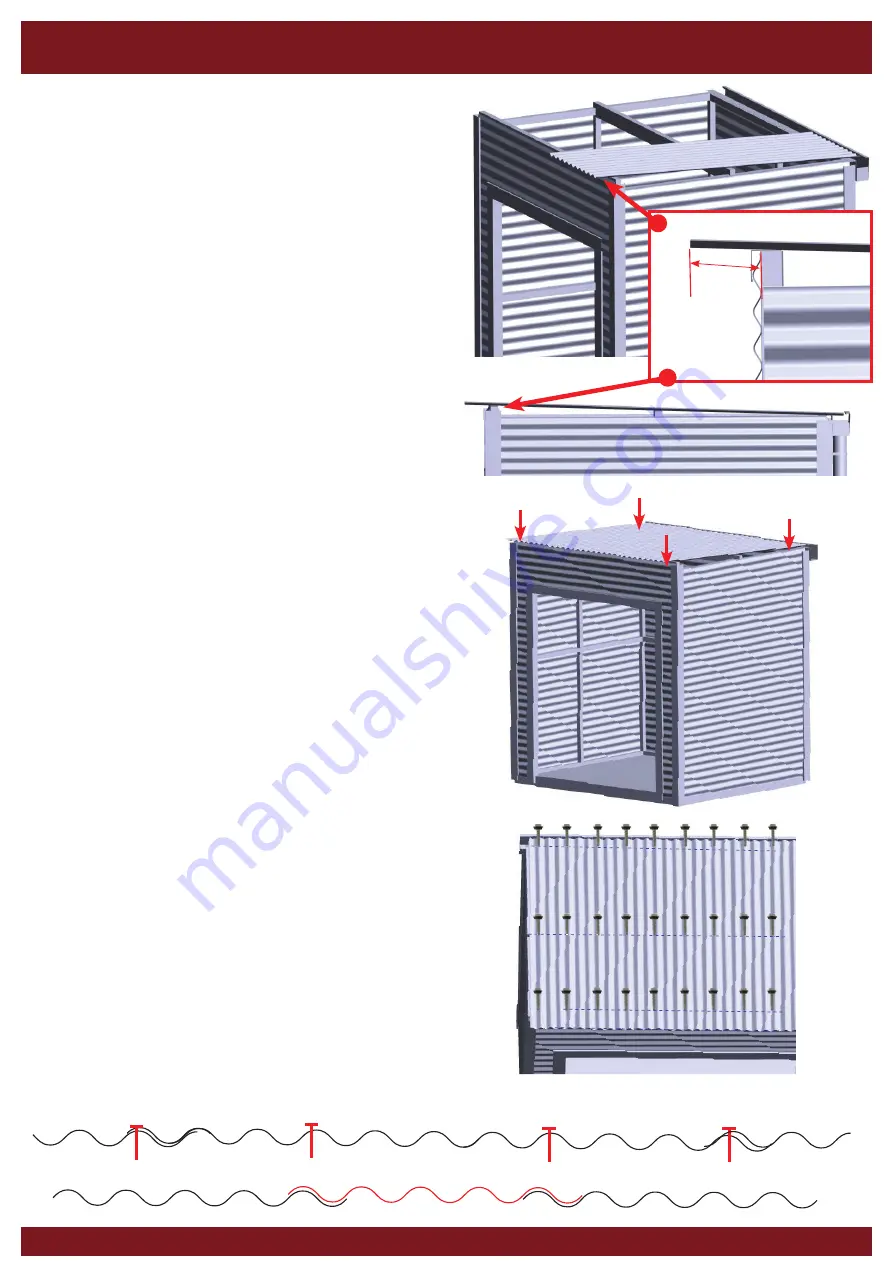
22
22
• Starting at one end, make sure the edge of the sheet is overhanging 20mm past
the end of the shed and screw 1 x 55mm tek screw through the top of the crest
on corrugate profi le into the top plate front and rear.
• Repeat at the other end.
• Check that everything is aligned and fi t the rest of the screws front and rear
using the Roof Fixing Pattern below as a guide. Start with the overlaps in the
sheets and then screw in the rest. You should use 4 screws front, middle and
rear for each sheet. Ensure to screw through the overlap as per below diagram.
ROOF FIXING PATTERN
1. Steel roof cladding - start from one end and overlap each sheet
2. Clear Panel - The Clear Panel overlaps both steel sheets on either side (shown
in red)
If an optional clear roof sheet has been supplied, this can be fi tted in any
of the middle positions. (Note - both edges of clear roof sheet overlap
the steel sheets at each side vs the steel sheets that are under on one
edge and over on the other).
• Starting from one end of the shed, place the fi rst roof sheet into position.
The edge of the sheet should overhang 20mm past the outside edge of
the timber end top plate and overhang the front of the front top plate by
250mm. (or 230mm from top plate fl ashing)
• Overlap the centre roof sheet with the fi rst one and align the ends. Repeat
with the remaining roof sheet(s).Make sure all the ends of the sheets are
aligned.
Overlap the last sheet to fi t the remaining space.
• Reach in from the back of the shed and place 1x rivet in the overlap,
600mm in from the back. Repeat with another rivet 600mm in from the front
of the sheet. Repeat with all of the overlap joins.
• Now that the sheets are joined together, adjust them so that they are square
on with the shed and that the top plates are straight. At the front of the
shed, create an overlap of 250mm past the front of the top plate.
22
ROOF
250mm
1
2