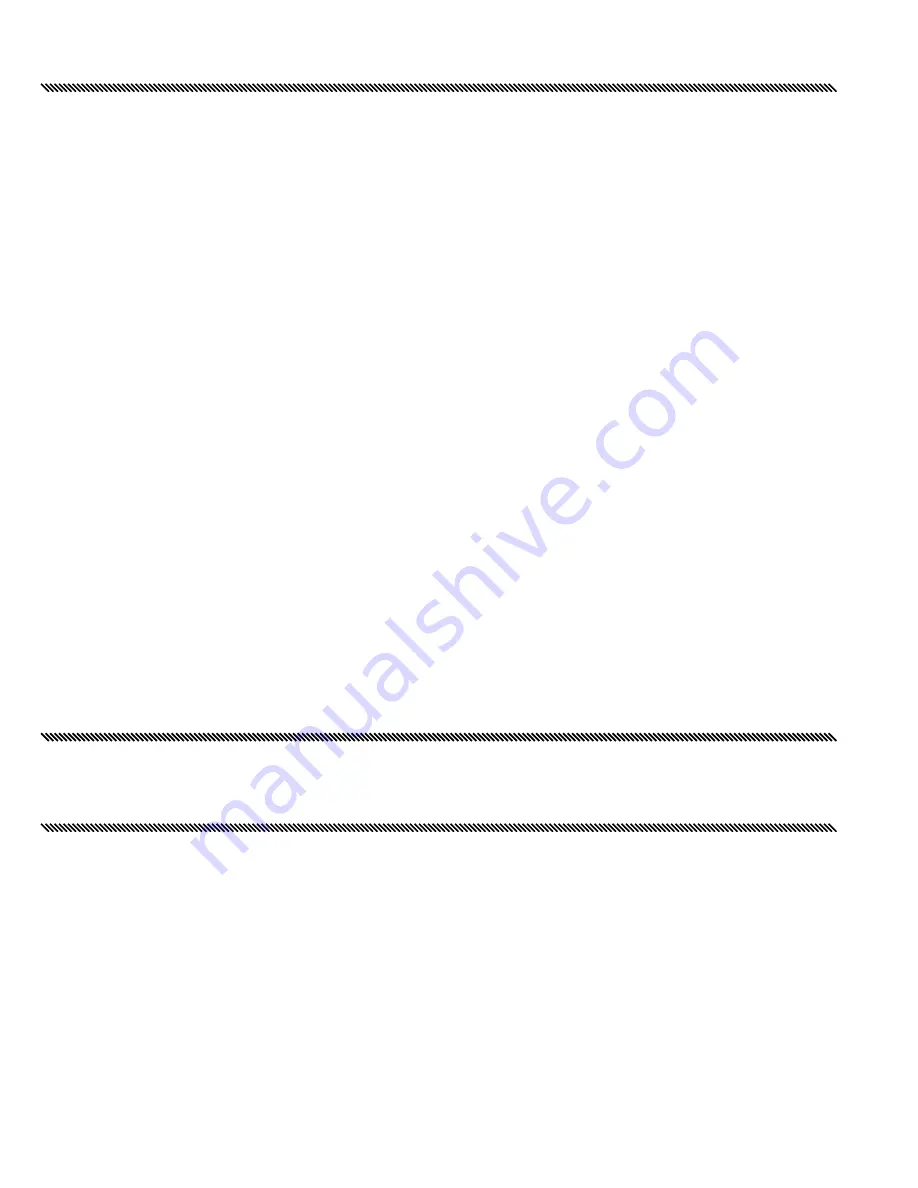
-12-
SERVICING
SERVICING
A SIMPLIFIED STEP-BY-STEP PROCEDURE
Duro Dyne has called upon its many years of pinspotting experience in designing the Mach 70 Rolling Head.
Your unit has been rigorously factory tested and inspected to provide many years of dependable service.
WHAT TO DO BEFORE YOU BEGIN TROUBLESHOOTING:
CONSULT THE MANUAL.
Most of the functional problems that occur are due to an oversight in the set-up, operational or normal
maintenance procedures. Therefore, you should re-check all “Set Up”, “Initial Adjustment”, “Operation” and
“Maintenance” procedures.
INSPECT THE UNIT
If the problem still persists, the next step is careful visual inspection. Turn off the electricity - that is,
disconnect your Pinspotter from its power supply and carefully check the control box for loose, broken or
disconnected wires. Also check the air circuit for leaky air connections or cut hoses.
HOW TO IDENTIFY WELD QUALITY PROBLEMS
By weld we mean that the Weld Transformer is energized, sending a pulse of electricity through the weld
pin, causing it to begin to fuse to the sheet metal.
To properly troubleshoot the weld quality problems, you must first pinpoint the symptom by test welding the
pins to bare sheet metal. The symptom will then show up in one of four categories:
1) The pins weld to bare metal but not on lined work.
2) The pins weld to bare metal but can easily be removed.
3) Pins weld to bare metal but remain on the weld tip as it retracts.
4) The pins do not weld at all.
Before troubleshooting, always check:
1) Air pressure for a minimum of 80 PSI during usage of unit.
2) The input Voltage for a minimum of 208V.
3) The Weld Timer is set properly.
4) The Upper and the Lower Weld tips for extreme wear.
It may become necessary to use a voltmeter and/or ohmmeter to perform some servicing procedures.
An analog type is best. Our Technical Services Dept will help you if necessary.
TROUBLESHOOTING
TROUBLESHOOTING
For assistance please call Duro Dyne Technical Services Dept at 1-800-899-3876 between the hours of
7am - 6pm EST.
N O T E S :
N O T E S :
1. The Feed Reed Switch is a safety that will not allow the machine to operate if the feed cylinder is not fully
retracted. The Feed Reed Switch is located on the Feed Cylinder. To check that the Feed Reed Switch is
positioned properly, loosen the set screws and put an Ohm meter on terminals 7 and 9 in the trolley. Slide
the Feed Reed Switch back and forth until continuity is indicated, then tighten the set screws.
2. Check that the Air Regulator is set for 80 psi. Mounted on the top of the Trolley are two Adjustable Ex-
haust Mufflers. The front one adjust the speed of the Dwell Cylinder moving down and the rear one adjust
the speed up. These mufflers can become restricted or loose. If machine is sluggish or starts slamming
down, adjust these mufflers accordingly.
3. The First Pulse Reed Switch is located in the middle of the Dwell cylinder.
4. To check that the Dwell Reed Switch is positioned properly, loosen the set screws and put an Ohm meter
on terminals 6 and 11. Slide the Dwell Reed Switch up and down until continuity is indicated, then tighten
the set screws.
5. Mounted on the Feed Cylinder is a Feed Speed Control. The Feed Speed Control adjusts how fast the Pusher
with Pawl moves in and out. If adjusted too fast the pins may be tossed past the tip, if adjusted too slow
the pins will not be placed on the tip.