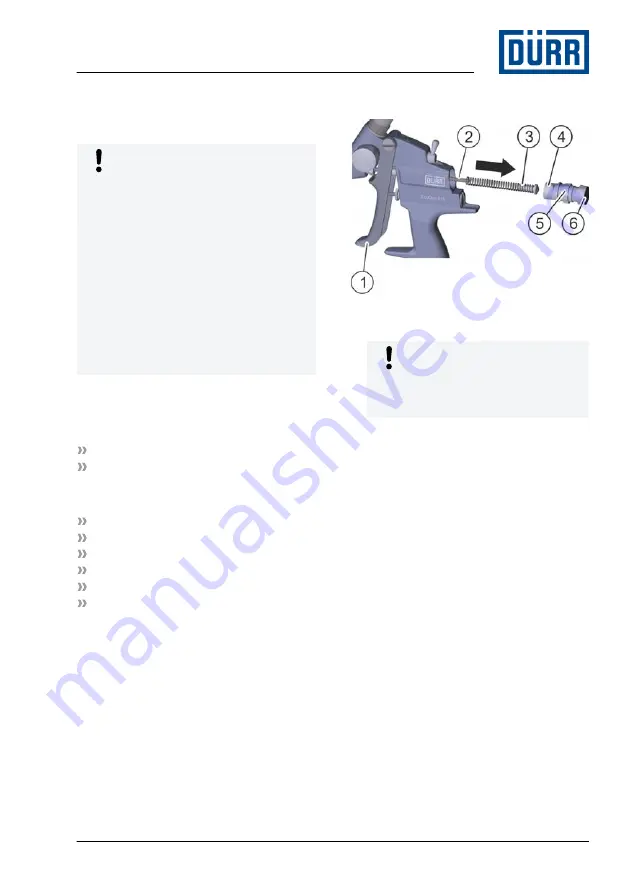
8.2
Troubleshooting
8.2.1 Replace needle and nozzle.
NOTICE!
Property damage due to improper
replacement of needle and nozzle
Replacing only the needle or only the
nozzle could damage spray gun compo-
nents. This can compromise the tightness
of the spray gun. The spray pattern deteri-
orates.
– Observe order of replacement steps
(needle – nozzle).
– Observe order of assembly steps
(nozzle – needle).
– Always replace nozzle and needle at
the same time.
The integrated Quick Clip technology allows
for removal and installation of the needle
without changing the preset needle stop.
Personnel:
Operator
+ additional qualification explosion pro-
tection
Protective equipment:
Protective gloves
Safety boots
Protective workwear
Eye protection
Respiratory protection device
Use ear protection
Removing the needle
Fig. 13: Replacing the needle
1.
NOTICE!
The stop screw is spring pretensioned.
When you loosen the stop screw it
might fall off.
Hold onto stop screw (6) while removing
it.
2. Counter the locknut (5) on the clip (4).
3. Press the stop screw (6) on the face by
about 1 mm into the spray gun.
4. Turn stop screw (6) ¼ turn counter clock-
wise.
ð
The spring on the needle (2) pushes
the stop screw (6) out.
5. Pull out the stop screw (6).
6. Remove the compression spring (3).
7. Pull back the trigger (1).
Faults
05/2018
EcoGun 910 - MSG00003EN
17/32