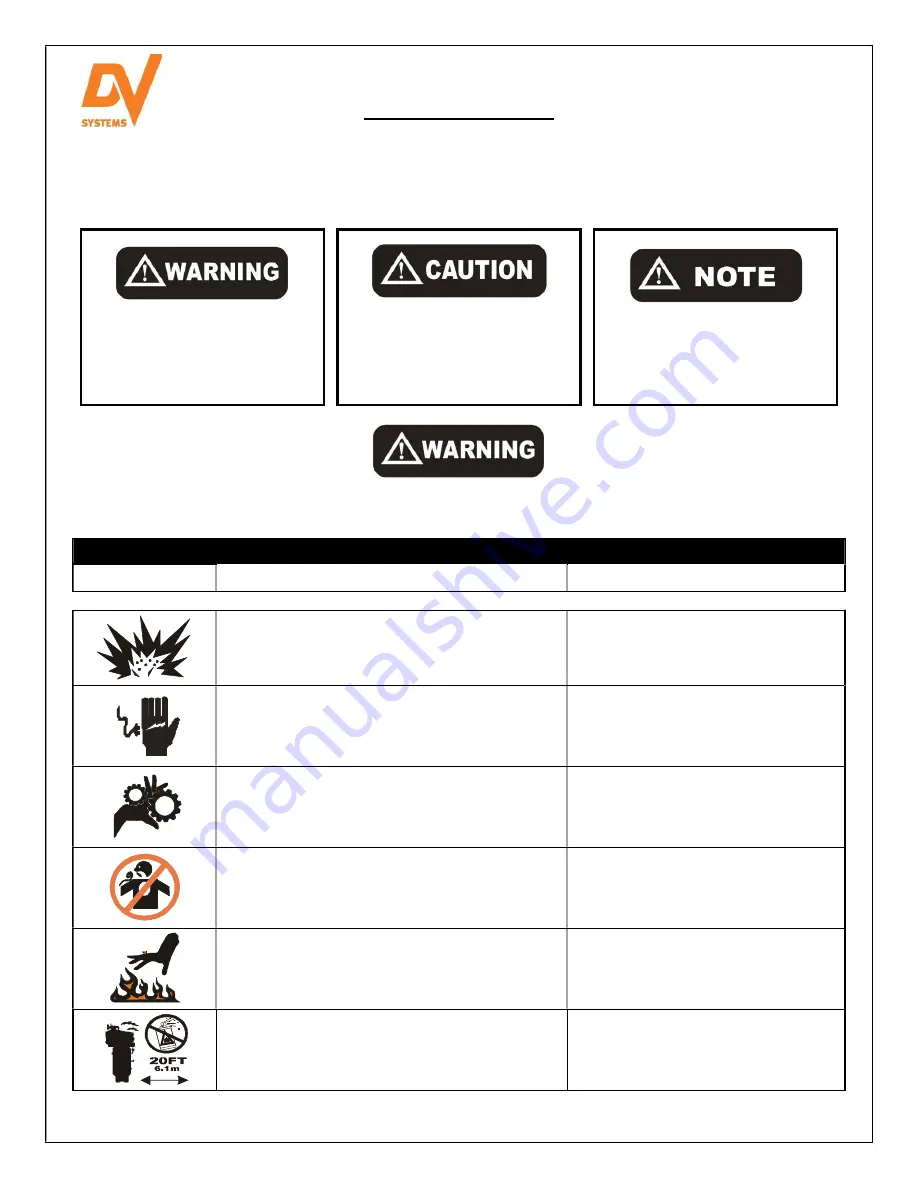
SDI-W
Feb ‘19
- 2 -
Safety Precautions
To operate the Compressor Unit safely and correctly, we have opted to use the following symbols to make you
aware of important points. These points relate to user safety and preventing equipment problems. Please pay
close attention to these sections.
The following hazards may occur during the normal use
of the equipment. Please read the following chart.
Area:
Hazard:
Safeguards:
What to look for:
What may occur if precautions are not observed.
How to avoid the hazard.
Tampering with the Unit while under full or partial
pressure may cause an explosion.
Relieve all pressure from the Unit
before attempting any repair or
maintenance work.
As the Unit starts and stops automatically, serious
injury may result from working on the Unit with the
power still in the on position.
Shut off all power to the Unit before
attempting any repair or maintenance
work.
As the Unit starts and stops automatically, do not
come into contact with moving parts.
Shut off all power to the Unit before
attempting any repair or maintenance
work.
Air compressed by the Unit is not suitable for
inhaling. It may contain vapours harmful to your
health.
Compressor capable of pressures > 50 psi.
Never directly inhale compressed air
produced by the Compressor.
Risk of injury, do not direct air stream
at body.
The Compressor Pump, Motor, and Tubing
become hot when running. Touching these areas
may cause severe burns.
Never touch the Pump, Motor, or
Tubing during or immediately after
operation.
As the electrical components on the Unit are
General Purpose, there is a potential for explosion
should vapours be present in the area.
The Compressor must be a minimum
of 20 feet (6.1 meters) from any source
of potentially explosive vapours.
Important safety Information.
A hazard that may cause
serious injury or loss of life.
Important information that
indicates how to prevent
damage to equipment, or how
to avoid a situation that may
cause minor injury.
Information that you should
pay special attention to.