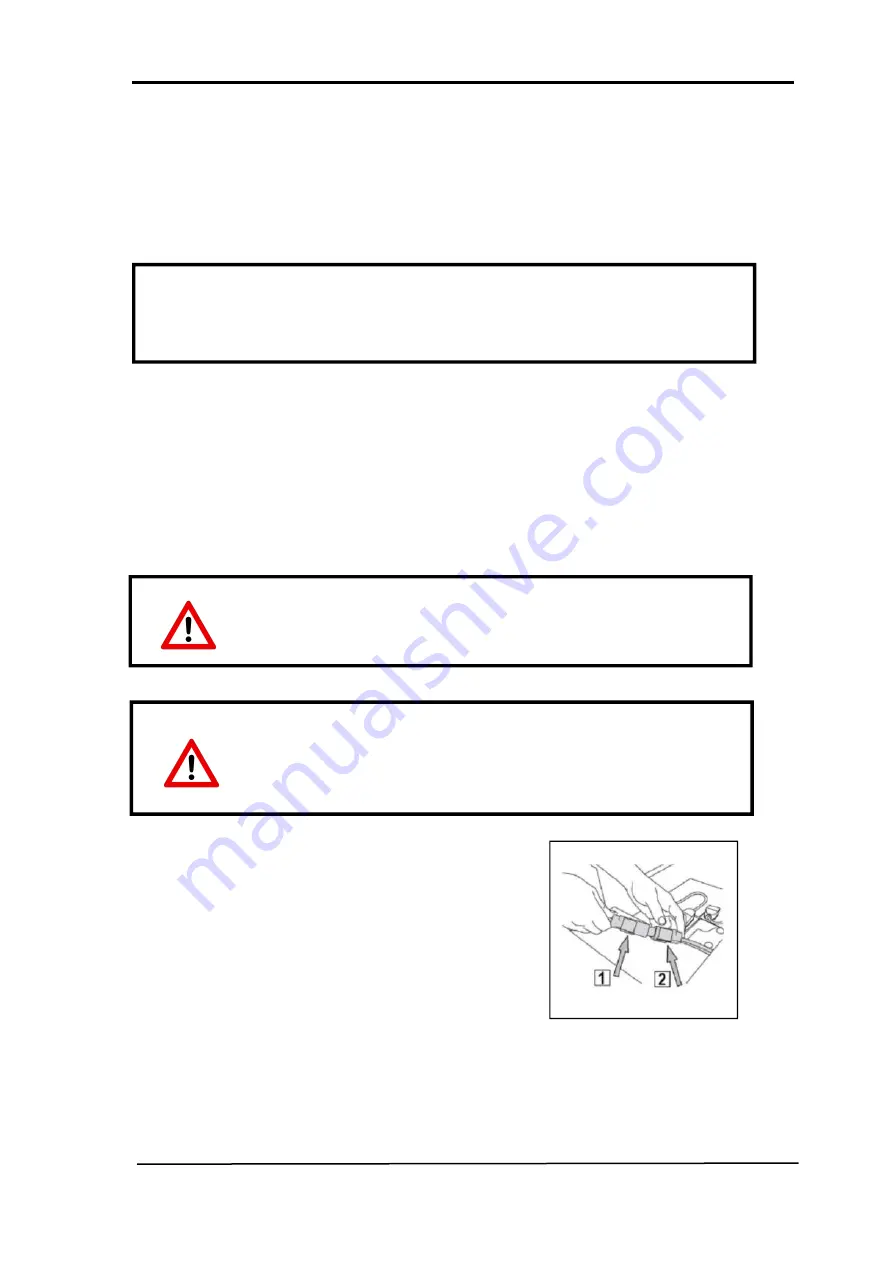
D9
7
□
Do not disassemble by hand, should be disassembly by tools.
□
It is forbidden to wash the machine directly with corrosive reagent or high pressure water.
□
in order to prevent coagulation of cleaning agent in the water tank filter , please do not leave the
agent in solution tank in a long time.
□
Do not put caustic soda products in agent it will damage rubber blade.
Preparation and configuration of the machine
Battery installation
The batteries are installed in the sewage box below specially designed
battery position, composed of high maintenance free battery 4 6v/200ah,
normally, the battery installation has been completed at the factory,
please do not arbitrarily change the battery configuration, please use the
original battery connecting wire and interface.
Battery connection
Battery plug (1) located in the battery above,
please connect with plug (2)
Do not arbitrarily change the battery connector,
if unauthorized changes will lose the battery
charger,
the quality assurance from the original factory.
battery charging connection
Battery charging port located inside of a post operation
,
As
shown in figure (1),lease connect charging port
(
2
)
with
figure (1)
please use the original configuration of the battery and charger, change one
configuration, will lose the quality of battery or charger factory guarantee!
please maintenance and charging battery follow the operation manual ,
regularly check the battery according to the maintenance requirement!
Remove the dirt on the surface of the cell, make sure the battery connection
fastening, To ensure battery ventilation.
please moving the machine and wooden pallets together by forklift,
the machine has no direct use of forklift position, do not handling
equipment directly!