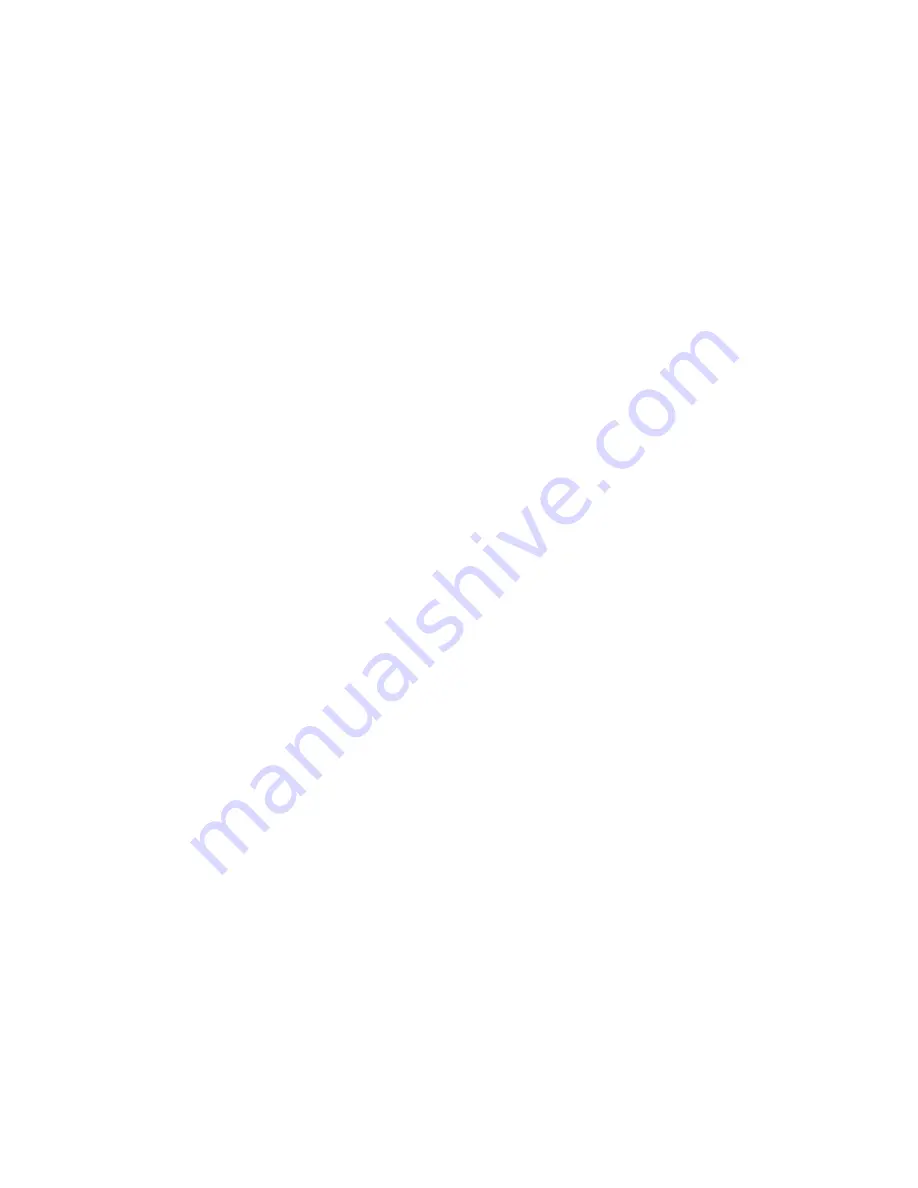
Page
22
DYCONN PRODUCT WARRANTY
To obtain warranty service, contact Dyconn customer service at (855) 239-2666 or visit
www.dyconn.com. Dyconn disclaims any liability for modification, improper installations, or
installations over specified weight range. Dyconn will not be liable for any damages arising
out of the use of, or inability to use of Dyconn products. Warranty specification is subject
to change without prior notice.