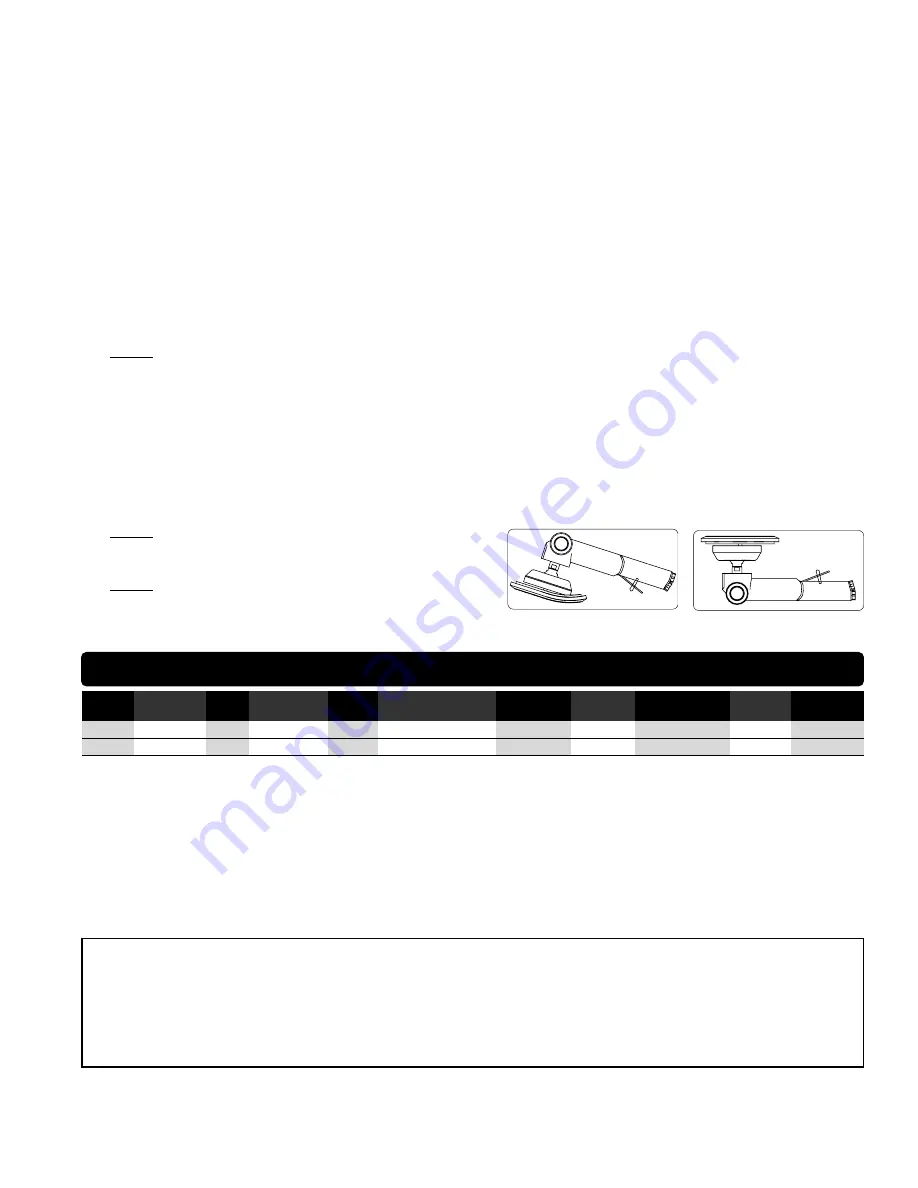
Model
Motor
Motor
Pad Dia.
Sound
Maximum Air Flow
Hose I.D. Size
Air Inlet
Weight
Length
Height
Number
hp (W)
RPM
Inch (mm)
Level
CFM/SCFM (LPM)
Inch or (mm)
Thread
Pound (kg)
Inch (mm)
Inch (mm)
10784
.7 (522)
2,500
8 (177)
87 dB(A)
3/27 (765)
3/8 or 10
1/4" NPT
6.4 (2.9)
14-3/8 (366) 5-13/16 (148)
10786
.7 (522)
2,500
8 (177)
87 dB(A)
3/27 (765)
3/8 or 10
1/4" NPT
6.4 (2.9)
14-3/8 (366) 5-13/16 (148)
Additional Specifications: Air Pressure 90 PSIG (6.2 Bar)
Sound Level is the pressure measurement according to the method outlined in ISO regulation ISO-15744
Maintenance Instructions
Important:
A preventative maintenance program is recommended whenever portable power tools are used. The program should include inspection of air
supply lines, air line pressure, proper lubrication and repair of tools. Refer to ANSI B186.1 for additional maintenance information.
•
Use only genuine Dynabrade replacement parts to insure quality. To order replacement parts, specify
Model#
,
Serial#
and
RPM
of your air tool.
•
It is strongly recommended that all Dynabrade rotary vane air tools be used with a Filter-Regulator-Lubricator to minimize the possibility of misuse due
to unclean air, wet air or insufficient lubrication. Dynabrade recommends the following:
11405
Air Filter-Regulator-Lubricator (FRL) – Provides accurate
air pressure regulation and two stage filtration of water contaminants. Operates 40 SCFM @ 100 PSIG with 3/8" NPT female ports.
•
Apply 3 plunges of 95542 Grease through grease fitting located on side of angle head with 95541 Grease Gun after every 100 Hours of use.
•
Dynabrade recommends one drop of air lube per minute for each 20 SCFM (example: if the tool specification states 40 SCFM, set the drip rate on the
filter-lubricator to 2 drops per minute). Dynabrade Air Lube (P/N
95842
: 1 pt 473 ml) is recommended.
Routine Preventative Maintenance:
•
Check the free speed of 8" Random Orbital Polisher by using a tachometer on regular basis.
•
BEFORE MOUNTING AN ACCESSORY, after all tool repairs and whenever a 8" Random Orbital Polisher is issued for use, check tool RPM
(speed) with tachometer with air pressure set at 90 PSIG while the tool is running. If tool is operating at a higher speed than the RPM marked on the
tool housing, or operating improperly, the tool must be serviced and corrected before use.
•
Mineral spirits are recommended when cleaning the tool and parts. Do not clean tool or parts with any solvents or oils containing acids, esters,
ketones, chlorinated hydrocarbons or nitro carbons.
•
DO NOT clean or maintain tools with chemicals that have a low flash point (example: WD-40
®
).
•
A Motor Tune-Up Kit (P/N
98224
) is available which includes high wear and medium wear motor parts.
•
Air tool labels must be kept legible at all times, if not, reorder label(s) and replace. User is responsible for maintaining specification information i.e.:
Model #, S/N, and RPM. (See Assembly Breakdown)
•
Blow air supply hose out prior to initial use.
•
Visually inspect air hoses and fittings for frays, visible damage and signs of deterioration. Replace damaged or worn components.
•
Refer to Dynabrade's Warning/Safety Operating Instructions Tag (Reorder No.
95903
) for safety information.
After maintenance is performed on tool, add a few drops of Dynabrade Air Lube (P/N
95842
) to the air line and start the tool a few times to lubricate air motor.
Check for excessive tool vibration.
Handling and Storage:
Tool Resting Position:
•
DO NOT rest tool on pad. (See Tool Resting Position Diagram)
•
Use of tool rests, hangers and/or balancers is recommended.
•
Protect tool inlet from debris (see Notice below).
•
DO NOT carry tool by air hose, or near the tool throttle lever.
•
Protect abrasive accessories from exposure to water, solvents,
high humidity, freezing temperature and extreme temperature changes.
•
Store accessories in protective racks or compartments to prevent damage.
Notice
All Dynabrade motors use the highest quality parts and materials available and are machined to exacting tolerances. The failure of quality pneumatic motors
can most often be traced to an unclean air supply or the lack of lubrication. Air pressure easily forces dirt or water contained in the air supply into motor
bearings causing early failure. It often scores the cylinder walls and the rotor blades resulting in limited efficiency and power. Our warranty obligation is
contingent upon proper use of our tools and cannot apply to equipment which has been subjected to misuse such as unclean air, wet air or a lack of
lubrication during the use of this tool.
One Year Warranty
Following the reasonable assumption that any inherent defect which might prevail in a product will become apparent to the user within one year from the
date of purchase, all equipment of our manufacture is warranted against defects in workmanship and materials under normal use and service. We shall
repair or replace at our factory, any equipment or part thereof which shall, within one year after delivery to the original purchaser, indicate upon our
examination to have been defective. Our obligation is contingent upon proper use of Dynabrade tools in accordance with factory recommendations,
instructions and safety practices. It shall not apply to equipment which has been subject to misuse, negligence, accident or tampering in any way so as to
affect its normal performance. Normally wearable parts such as bearings, contact wheels, rotor blades, etc., are not covered under this warranty.
Machine Specifications
3
CORRECT Resting Position
INCORRECT Resting Position