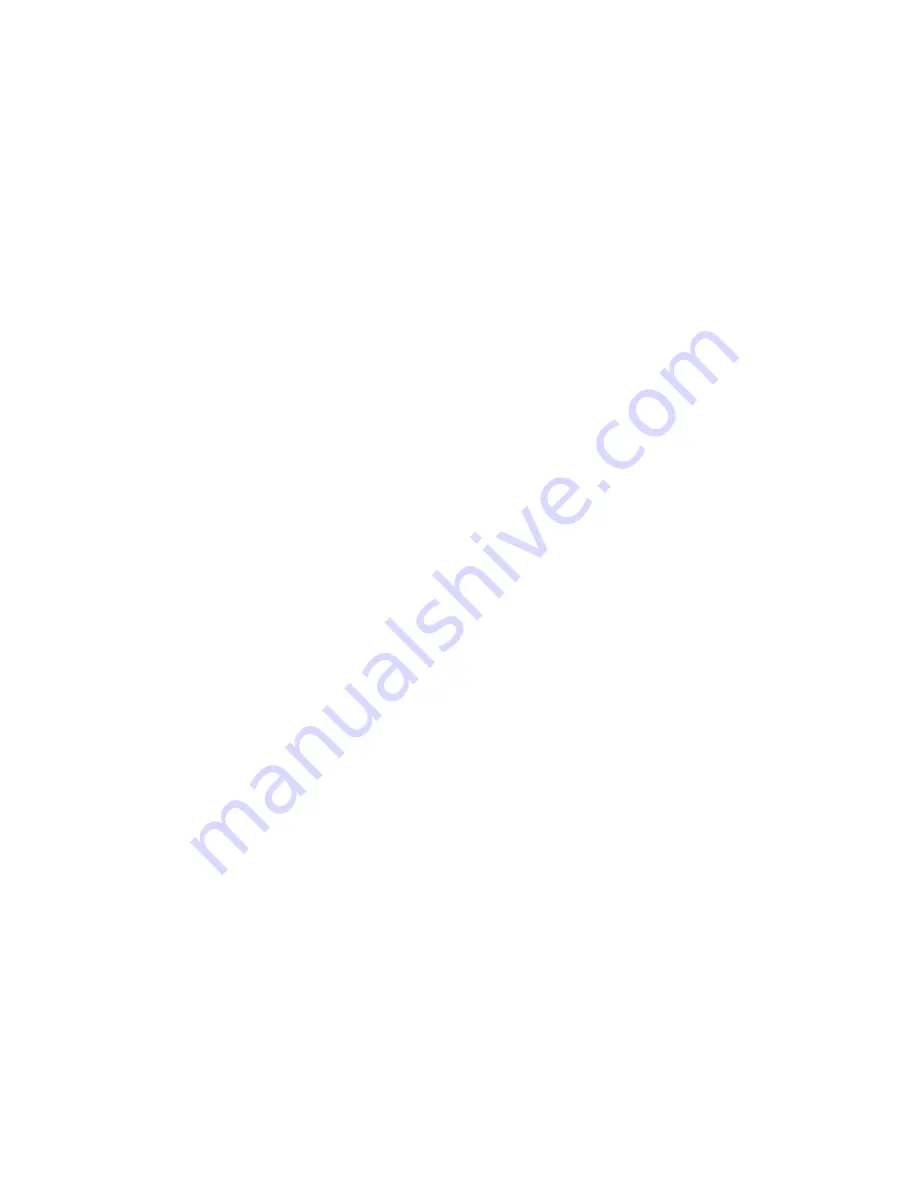
Assembly/Disassembly Instructions - Continued
7.
Position the end of the
18594
Pinion Gear on the tool plate of the arbor press and place the rear bearing/plate assembly on the rear bearing journal of
the rotor.
Note
: Make sure that the cylinder line-up pin
18572
aligns with the hole in the rear bearing plate.
8.
Use the raised inner portion of the
96240
Bearing Press Tool and the arbor press to push the
18555
Bearing along with the rear bearing plate down onto
the rotor until the bearing plate touches the cylinder. This should create a snug fit between the bearing plates and the cylinder. If the fit is too loose, add
a slight bit more press (preload).
Note
: A “snug” fit allows the cylinder to be shifted back and forth with a small amount of finger pressure. However, the
fit should not be loose or sloppy.
9.
Use the
96343
Retaining Ring Pliers to install the
18567
Retaining Ring onto the rotor.
10.
Hold the
18552
Housing in a vise with bronze or aluminum jaws so that the motor opening is pointing up.
1
1.
With the bearing plates and the cylinder aligned, apply a film of oil to the outside diameter of the motor. Orient the motor according to the exhaust
passage in the
18552
housing and the
18579
Valve Housing. Carefully slide the motor into the
18552
Housing.
Note
: It may be necessary, warm the
housing with a “Hot Air Gun”. This will expand the housing and facilitate the installation of the motor.
12.
Install the
18576
Gasket,
18577
Spacer and
18578
Gasket. These must align with the
18572
Pin, air inlet and exhaust openings.
13.
Orient and install the
18579
Valve Housing so that the air inlet and exhaust openings align correctly.
14.
Use the
95331
(4mm) Hex Key to fasten the valve housing to the
18552
Housing with the
18559
Washers (4) and the
18580
Screws (4).
(Torque to 10.75 N
•
m/95 in. lbs.)
15.
Install the
18601
Grip onto the
18579
Valve Housing.
Note
: A “Hot Air Gun” can be used to warm the
18601
Grip, making it more flexible.
16.
Install an air fitting into the
18591
Inlet Bushing and connect to the air supply. Test the air motor for proper operation.
Motor Assembly Complete.
Right Angle Gear Assembly:
1.
Wipe off the surface of the
96231
Tool Plate to make sure that it is clean. Place the open side of the
18561
Bearing on the tool plate so that the inner
race is supported. Position the spindle into the bearing so that the threaded end is pointing up. Press the spindle and the bearing together.
2.
Place the
18902
Spindle Cap on the tool plate so that the open side of the bearing pocket is facing up.
3.
Position the spindle with the bearing on the spindle cap so that the threaded end of the spindle is pointing up. Press the spindle with bearing all the way
into the spindle cap.
4.
Use the
96343
Retaining Ring Pliers to install the
18562
Retaining Ring.
5.
Clean the keyway of the spindle with a swab moistened with acetone. Also, clean the
18563
Key with acetone and apply a small amount of
Loctite
®
#380 (or equivalent) to the keyway. Install the key and let the adhesive set.
6.
Install and press the
18593
Bevel Gear onto the spindle. Apply a small amount of the
95542
Grease to the bevel gear and pinion.
7.
Install the
18557
Wave Washer and use the retaining ring pliers to install the
18556
Retaining Ring.
8.
Place the threaded portion of the spindle on the tool plate of the arbor press and use the raised center portion of the
96240
Bearing Press Tool
to press the
18555
Bearing onto the spindle.
9.
Install the
18554
Spacer into the
18552
Housing so that the raised outer portion of the spacer will be against the outer race of the
18555
Bearing.
10.
Orient the air bleed notch of the spindle cap toward the throttle lever and install the spindle assembly into the housing. Check the fit of the gears and
for smooth rotation.
11.
Use the
95331
(4mm) Hex Key to install the
18560
Screws (4), and
18559
Washers (4). (Torque to 9 N
•
m/80 in. lbs.)
12.
Apply 3 plunges of the
95542
Grease through the grease fitting with the
95541
Lubrication Gun initially, and after every 100-hour interval of use.
Right Angle Gear Assembly Complete.
Orbital Head Assembly:
1.
Slide
61394
Switch Shaft into the housing so that it is in the rotary (unlock) position.
2.
Install
61935
Switch Spring,
61393
Pin,
61397
Spring, and
61396
Locking Pin Insert.
3.
Apply a small amount of the Loctite #242 (or equivalent) to the external threads of
61398
Locking Pin Bushing and install into the orbital head using the
96364
Slotted screwdriver.
4.
Wipe all oil and grease for the outside diameter of the
57069
Balancer Shaft with a clean cloth. Wipe all oil and grease from the inside diameter of the
56052
Bearing.
5.
Apply a small amount of the Loctite #609 (or equivalent) to the outside diameter of the
57069
Balancer Shaft.
6.
Place the
57069
Balancer Shaft on the tool plate of the
96232
#2 Arbor Press. Position the sealed side of the
56052
Bearing on the balancer shaft and
use the
57091
Bear Press Tool to install the bearing onto the balancer shaft.
7.
Wipe all oil and grease from the outside diameter of the
56052
Bearing and the bearing pocket of the orbital head. Apply a small amount of the Loctite
#609 (or equivalent) to the outside diameter of the bearing and install the balancer shaft and the bearing into the orbital head
8.
Apply a small amount of the Loctite #242 (or equivalent) to the threads of the three
95235
Screws and install these into the orbital head
(Torque to 5.7 N•m/50lb-in.).
9.
Use the
95823
21mm Wrench to install the orbital head assembly on the spindle.
10.
Slide
61394
Switch Shaft to the lock position.
11.
Assemble the washers and spacer as shown on page 4 and place the backing pad on the
57069
Balancer Shaft. Use the
95823
21mm Wrench to hold
the head stationary while installing the
96168
Screw with a 3/16" hex key (Torque to 11.3 N•m/100lb-in.).
12.
Connect the polisher to the air supply hose and check for the proper operation.
Orbital Head Assembly Complete. Polisher Assembly Complete.
Please allow 30 minutes for adhesives to cure before operating tool.
Important:
Motor should now be tested for proper operation at 90 PSIG. If motor does not operate properly or operates at a higher RPM than marked on the
tool, the tool should be serviced to correct the cause before use. Before operating, place 2-3 drops of Dynabrade Air Lube (P/N
95842
) directly into air inlet
with throttle lever depressed. Operate tool for 30 seconds to determine if tool is operating properly and to allow lubricating oils to properly permeate motor.
Right Angle Gear Lubrication Instructions:
•
Apply 3 plunges of the
95542
Grease through the grease fitting with the
95541
Lubrication Gun after every 100-hour interval of use.
6
Loctite
®
is a registered trademark of Loctite Corp.