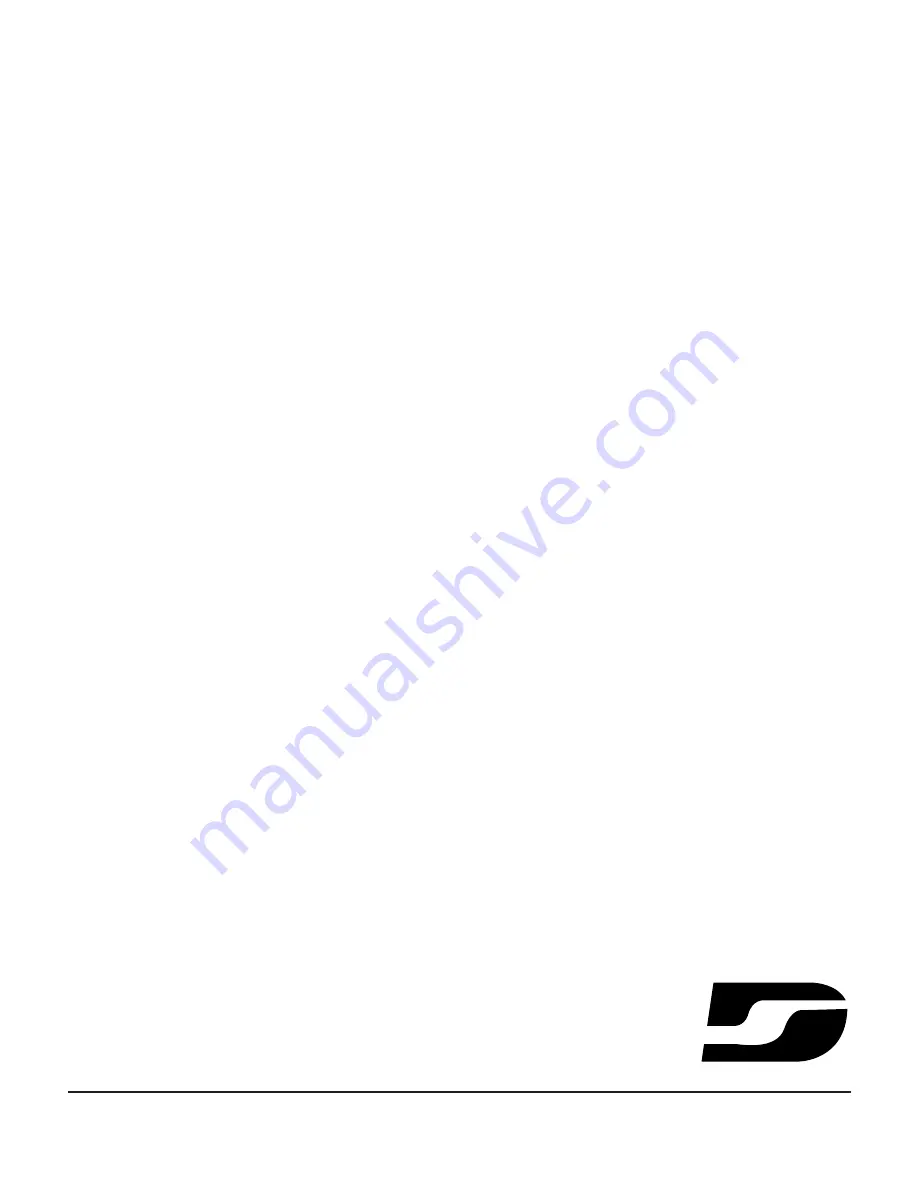
DYNABRADE, INC.,
8989 Sheridan Drive
•
Clarence, NY 14031-1490
•
Phone: (716) 631-0100
•
Fax: 716-631-2073
•
International Fax: 716-631-2524
DYNABRADE EUROPE S.àr.l.,
Zone Artisanale
•
L-5485 Wormeldange—Haut, Luxembourg
•
Telephone: 352 76 84 94
•
Fax: 352 76 84 95
© DYNABRADE, INC., 1996
PRINTED IN USA
DYNABRADE
®
Disassembly/Assembly Instructions (continued)
Spindle Disassembly:
1. Remove the (5)
95897
Cap Screws from the retainer.
2. Remove the
52091
Retainer.
3. Grip onto the spindle and pull evenly away from housing.
4. Remove
52089
Washer,
52088
Spacer and
50412
Felt Ring.
5. Secure
52117
Spindle into vise using wrench flats and remove
52118
Spindle Nut (right hand thread).
6. Remove
50431
Bearing.
7. Secure bevel gear into a soft jaw vise and press spindle through the gear.
8. Remove
12152
Bearing by pressing the
50424
Bearing Washer through the housing.
Note:
Replace by pressing on outside diameter of the bearing.
Motor Reassembly:
Important:
Be certain all parts are cleaned, properly greased and in good repair before reassembly.
1. Slide
07119
Front Bearing Plate with
01036
Front Bearing in place on to
07106
Rotor (see step 4).
2. Place
50435
Key onto rotor shaft.
3. Press bevel pinion into place. Secure
95939
Ring in place.
4. Place the correct number of shims from the
01277
Shim Pack between the front bearing and front bearing plate to achieve a .0015 inch spacing between
the front bearing plate and
07106
Rotor when forward pressure is applied to both the bearing plate and the rotor toward the bevel pinion.
5. Place the blades into rotor slots.
Note:
Blades should be lightly lubricated with Dynabrade Air Lube P/N
95842
(or equivalent) before installation in rotor slots.
6. Place cylinder over rotor and blade assembly. The scalloped end goes towards the front plate.
7. Place the
07114
Rear Bearing Plate (with
01007
Bearing pressed into place) over the rotor and line-up short pin on cylinder with the small hole in the
rear plate and press into place.
8. Place the bevel pinion into a soft jaw vise and tighten the governor assembly
(07124
Governor Cage) to 9.0 N•m (80 lb. – In.) (left hand thread).
9. Place complete motor assembly into housing.
10. Tighten
02626
Adjustment Bushing into
52090
Adapter to 50 N•m (450 lb. – In.). Add 2 drops of #271 loctite or equivalent to threads of adjustment
bushing before tightening.
11. Tighten
52090
Adapter into housing with 39.5 N•m (350 lb. – In.).
12. Secure inlet bushing into vise. Replace
02631
Nut and
01746
O-Ring. Swivel
07141
Valve Body to desired throttle lever position. Tighten
02631
Nut to 45
N•m (400 lb. – In.).
13. Unroll 07136 Grip back into place.
Spindle Reassembly:
1. Press bevel gear into place on
52117
Spindle.
2. Press
50431
Bearing up against shoulder.
3. Tighten
52118
Spindle Nut to 34 N•m (300 lb. – in.).
4. Place
52088
Spacer up against the bearing.
5. Mount
50412
Felt Ring over spindle nut and down inside
52088
Spacer.
6. Place
52089
Washer with the deeper counter bore toward the felt ring.
7. Slide the spindle assembly down into the housing lining up the small end of the spindle into the
12152
Bearing.
8. Place the correct number of shims from the
52120
Shim Pack checking for backlash (back and forth clearance in the gear teeth while pressing down into
the housing).
Note:
Minimal backlash of the gear set is recommended.
9. Replace
52091
Retainer. Line up 5 hole pattern and secure with (5)
95897
Screws.
Note:
Always check tool RPM before mounting any wheel, disc or accessory, with a tachometer, while maintaining 90 PSIG at the tool inlet under a no load
condition. If tool is operating at a higher speed than the RPM marked on the tool, the tool should be serviced to correct the cause before use.
Tool assembly is complete.
Important:
The regular maintenance of any air tool will contribute to greater efficiency of tool and will prolong tool life. The failure of quality pneumatic air motors can most
often be traced to an unclean air supply or the lack of lubrication. Air pressure easily forces dirt or water contained in the air supply into motor bearings
causing early failure. It often scores the cylinder walls and the rotor blades resulting in limited efficiency and power. Frequent drainage of water traps in air
lines is recommended. Each tool on each drop should also be equipped with a secondary air processing unit. This consists of an in-line Filter-Regulator-
Lubricator. All Dynabrade air tools must be used with a Filter-Regulator-Lubricator to maintain all warranties. Our warranty obligation is contingent upon proper
use of our tools and cannot apply to equipment which has been subject to misuse such as unclean air, wet air or a lack of lubrication during the use of the tool.
Loctite® is a registered trademark of the Loctite Corp.